Five-axis CNC machine tools, known as the “industrial mother machine,” are critical in strengthening national industries and advancing manufacturing by enabling the production of complex, high-precision parts.
Among them, five-axis linkage CNC machine tools represent the highest level of technology. They enable the production of complex, high-precision parts. This capability reflects a country’s manufacturing strength and automation level.
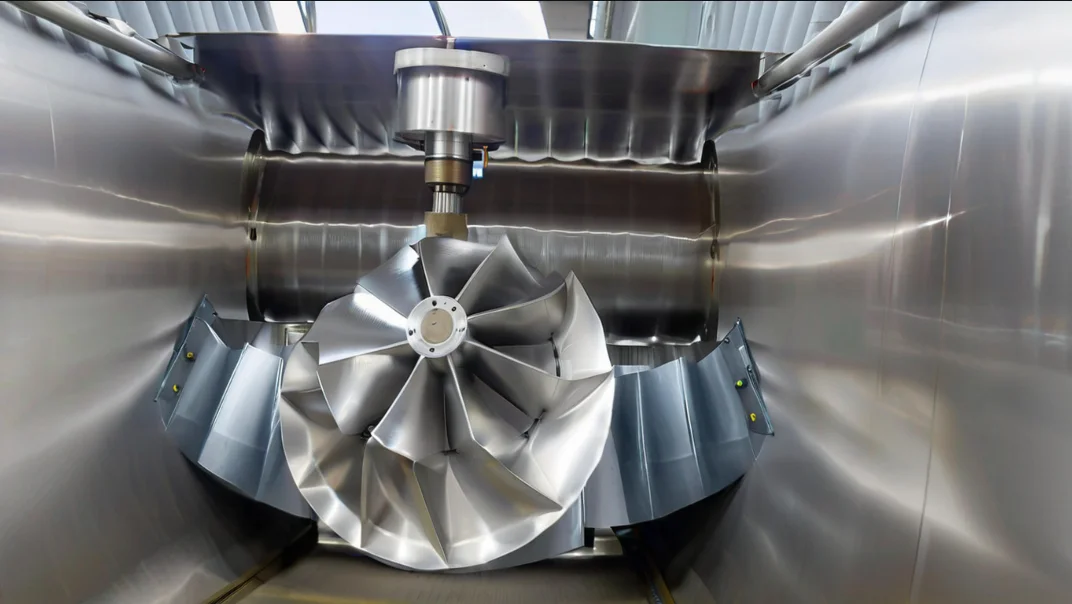
1 Advantages of Five-Axis Linkage CNC Machine Tools
1.1 Complex Workpiece Machining
Five-axis CNC machines can process intricate geometries that three-axis machines cannot handle. They avoid tool interference during machining. These machines use shorter, more rigid tools when producing parts like impellers and turbine blades. This setup improves stability, reduces tool changes, and eliminates the need for specialized cutters.
1.2 Improved Efficiency and Accuracy
Five-axis machines reduce clamping times. They minimize repositioning and require fewer fixtures. These improvements significantly boost machining efficiency and precision.
1.3 High Flexibility and Integration
Five-axis machines can process multiple surfaces in a single setup. This flexibility makes them ideal for industries like aerospace and automotive, where complex parts are common. They shorten development cycles and increase the success rate of new products. As a result, five-axis machines have become a strategic focus in global CNC development.
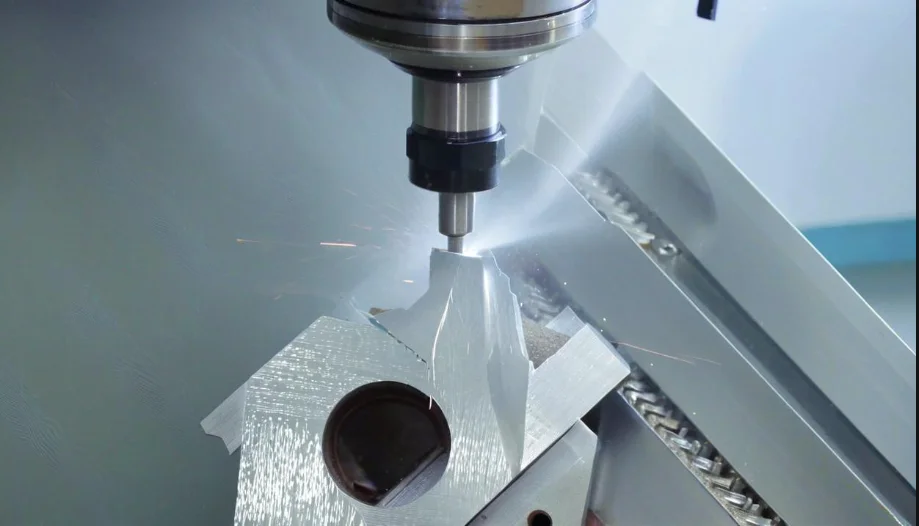
Basic Structure of Five-Axis CNC Machines
Most five-axis CNC machines use a “3+2” setup. They combine three linear axes (X, Y, Z) with two rotary axes (A, B, or C). There are three common structural forms:
Double Rotary Table: The machine uses a 4-axis and C-axis combination. The A-axis rotates around the X-axis, while the C-axis rotates around the Z-axis. This design enables multi-angle machining with a vertical spindle.
Turntable + Swing Head: The machine combines a rotating table with a swiveling head. This setup adapts flexibly to different workpieces. It can handle larger, more complex parts.
Double Swing Head: The machine uses two swiveling heads. This design offers excellent maneuverability. It works well for high-precision, large-scale components.
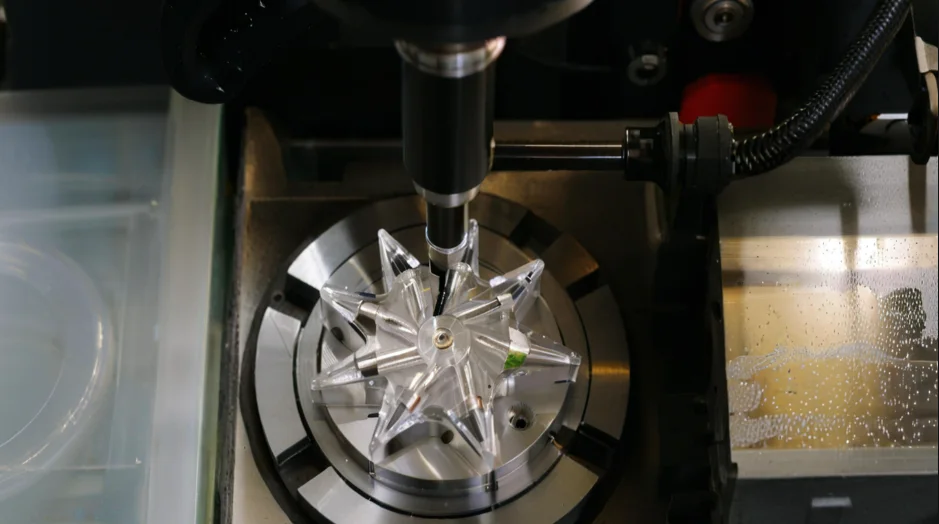
2 Global and Domestic Research Status
2.1 International Development
Countries like Germany, the U.S., and Japan lead in five-axis CNC technology. They continue to push for faster speeds, higher precision, smarter systems, multifunctionality, reliability, and eco-friendliness.
For example:
France’s DIAM machining center combines turning, milling, boring, drilling, gear cutting, and on-machine inspection — all in one setup. This integration maximizes efficiency and accuracy.
South Korea’s Hyundai Wia XF6300 features high-speed, high-precision machining. Its 15,000 rpm spindle reduces vibration and achieves micron-level accuracy.
2.2 China’s Progress
China’s CNC industry has grown rapidly. However, high-end five-axis machines still lag in control systems, key components, reliability, and precision retention. National strategies like “Made in China 2025” are driving change. The industry is moving from R&D and trials to large-scale production. With support from companies and universities, the technology continues to mature.
3 Development Trends and Future Prospects
3.1 Development Trends
High Precision:
CAM software advancements now enable micron-level precision. This ensures dimensional and geometric accuracy for complex parts.
Multifunctionality:
CNC machines are evolving into multitasking centers. They now combine turning, milling, drilling, tapping, and boring in one setup. This reduces cycle times and increases productivity.
Intelligent Control:
AI, big data, and IoT technologies are transforming CNC machines. They now include smart functions like:
Adaptive control to optimize cutting parameters.
Self-diagnosis for quick fault detection and automatic recovery.
Simulation and replay to analyze errors and improve processes.
Intelligent servo systems to enhance performance and stability.
Enhanced Flexibility:
Single-clamp, multi-angle processing reduces the need for repositioning and manual adjustments. Machines are becoming more modular and scalable. This makes them adaptable to different production needs.
4 Future Outlook
Five-axis CNC machines are evolving to become faster, more precise, multifunctional, smarter, and more flexible. International competitors still hold an advantage. However, China is closing the gap. To achieve breakthroughs, domestic manufacturers must take key actions:
Strengthen R&D Collaboration: Companies, universities, and research institutions must work together to speed up innovation.
Invest in Core Technologies: The industry should build national key labs. It must also focus on improving CNC control systems, precision components, and software integration.
Cultivate Skilled Talent: Schools and training programs must align with industry needs. They should emphasize high-end CNC technology and innovation.
Promote Sustainable Manufacturing: Manufacturers should design energy-efficient, eco-friendly machines to meet global green manufacturing standards.
By accelerating technological innovation, nurturing talent, and embracing intelligent manufacturing systems, China aims to achieve independent production of high-end CNC machines. This effort will help position China as a global leader in advanced manufacturing.