CNC milling machines are indispensable tools in modern industry due to their ability to deliver precision, productivity, flexibility, and efficiency across a wide range of manufacturing applications. CNC milling machine cited in the general milling machine on the basis of the development of the two processing technology is basically the same, the structure is also somewhat similar, but the CNC milling machine is relying on the program control of automatic processing machine tools, so its structure is also very different from the ordinary milling machine.
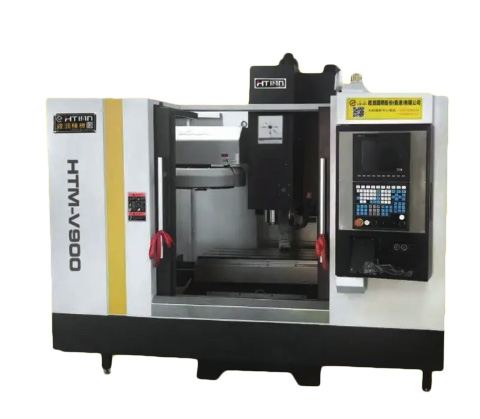
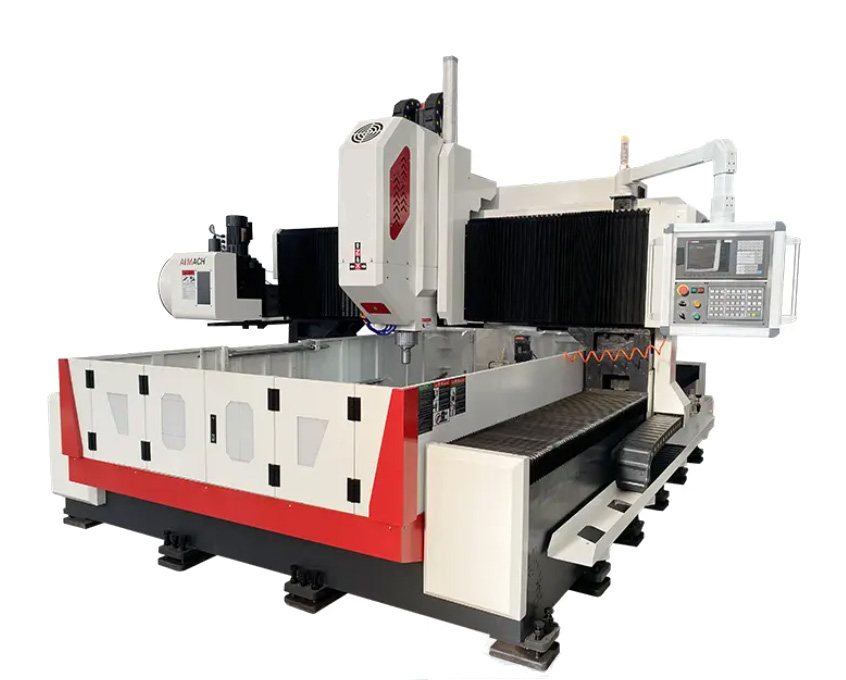
Main system description
Spindle box
Including the spindle box and spindle drive system, used to clamp the tool and drive the tool rotation, spindle speed range and output torque has a direct impact on machining.
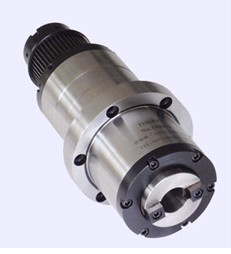
Feed servo system
It consists of feed motor and feed actuator to realize the relative motion between tool and workpiece according to the programmed feed speed, including linear feed motion and rotary motion.
Control system
The center of motion control of CNC milling machine, executing CNC machining program to control the machine for machining.
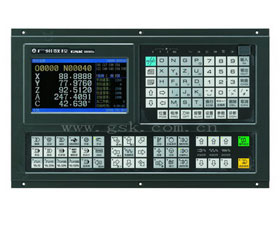
Auxiliary devices
Such as hydraulic, pneumatic, lubrication, cooling system, chip removal and protection devices.
Machine tool base parts
Usually refers to the base, column, beam, etc., which is the foundation and framework of the entire machine tool
Features of CNC milling machine
1, the adaptability of parts processing, good flexibility, can process the contour shape is particularly complex or difficult to control the size of the parts, such as mold parts, shell parts.
2, can process ordinary machine tools can not be processed or very difficult to process parts, such as mathematical models to describe the complex curve parts and three-dimensional space surface parts.
3, can process a clamping and positioning, need to carry out multi-processing parts.
4、High machining precision, stable and reliable processing quality.
5, high degree of production automation, can reduce the operator’s labor intensity. Favorable to production management automation.
6, high production efficiency.
7, from the cutting principle, either end milling or circumferential milling belongs to the intermittent cutting mode, not like turning as continuous cutting, so the requirements of the tool is higher, with good impact resistance, toughness and wear resistance. In dry cutting conditions, also requires good red hardness.
The basic structure of CNC milling machine
CNC milling machine in various forms, the following XK5040A CNC vertical lift table milling machine as an example to introduce its composition. The machine tool consists of six main parts. That is, the bed part, milling head part, table part, cross feed part, elevating table part, cooling, lubrication part.
(1) bed
The internal layout of the bed is reasonable, with good rigidity, the base is equipped with four adjusting bolts to facilitate horizontal adjustment of the machine tool, cutting fluid storage rags are located inside the machine base.
(2)Milling head section
The milling head consists of two parts, namely, step (or stepless) gearbox and milling head. The spindle of the milling head is supported on high-precision bearings. Ensure that the spindle has a high rotary accuracy and good rigidity; spindle equipped with a quick tool change nut, the front end of the taper using 1 $ 0505 taper; spindle mechanical stepless speed, its wide range of adjustment, smooth transmission, easy to operate. The brake mechanism can make the spindle brake quickly, which can save the auxiliary time. When braking, the spindle is braked immediately by braking the stop ring through the brake handle. When starting the main motor, care should be taken to release the spindle brake handle. The milling head part is also equipped with servo motor, internal gear pulley, ball screw and spindle sleeve, which form the vertical direction (z-direction) feeding transmission chain, so that the spindle makes vertical linear motion.
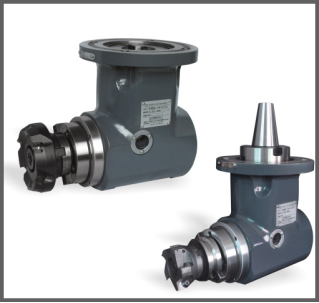
(3)Worktable
The worktable and the bed saddle are supported on the wide horizontal guideway of the lifting platform, and the longitudinal feeding of the worktable is driven by the servo motor installed at the right end of the worktable. Through the internal gear pulley drive precision ball screw cuts, so that the table to obtain longitudinal feeding. The left end of the table is equipped with a handwheel and dial for manual operation. The longitudinal and transverse guide surfaces of the bed saddle are TuRcllE B pasted with plastic surfaces, which improves the wear resistance of the guide, smoothness of movement and accuracy retention, and eliminates the phenomenon of low-speed crawling.
(4) Lifting table (lateral approach part)
The front of the lifting table is equipped with AC servo motor. Drive the bed saddle for transverse feeding movement, the transmission principle is the same as the longitudinal feeding of the table. In addition. In the front of the transverse ball screw is also equipped with a feed handwheel, can be realized manually feed. The left side of the lifting table is equipped with a locking handle, and the front end of the shaft is equipped with a long handle, which can drive the bevel gear and the lifting table screw to rotate, so as to obtain the lifting movement of the lifting table.
(5) Cooling and lubrication device
① Cooling system. The cooling system of the machine tool is composed of cooling pump, outlet pipe, return pipe, switch and nozzle, etc. The cooling pump is installed in the inner cavity of the base of the machine tool, and the cooling pump pumps the cutting fluid from the reservoir in the base to the outlet pipe, and then sprays it out through the nozzle to cool the cutting zone.
② Lubrication system and method. The lubrication system is composed of manual lubrication oil pump, oil distributor, throttle valve, oil pipe and so on. The machine tool adopts cycle lubrication mode, using manual lubrication oil pump, through the oil distributor to lubricate the spindle sleeve, longitudinal and transverse guideway and three-way ball screw, in order to improve the service life of the machine tool.
CNC milling machine mechanical structure
From the digital control technology characteristics. As a result of effective control of machine tools using servo motors, the application of digital technology to achieve a direct control of the machine tool executing parts of the working order and motion displacement, the traditional machine tool gearbox structure was canceled or partially canceled, and thus the mechanical structure is also greatly simplified. Digital control also requires the mechanical system has a high degree of transmission rigidity and no transmission gap to ensure the implementation of control instructions and the realization of the quality of control. At the same time. As the computer level and control capabilities continue to improve, the same machine tool allows more functional components at the same time to perform the various auxiliary functions required has become possible, and thus the mechanical junction of the CNC machine tool hollowing out more than the traditional machine tool has a higher integration of functional requirements.
From the requirements of the development of manufacturing technology, with the emergence of new materials and new processes, as well as market competition for low-cost requirements, metal cutting process is moving towards cutting speed and accuracy is increasingly high, more and more efficient and more reliable system development direction. This requires the development of traditional machine tools on the basis of CNC machine tools with higher precision. Drive power is more too, the mechanical mechanism dynamic ‘static, thermal stiffness is better, more reliable, can realize long time with continuous operation and as little downtime as possible. Typical CNC milling machine mechanical structure mainly consists of basic parts, the main drive system, feed drive system, rotary table and other mechanical functions accessories and other parts.
Selection of CNC milling machine
Size selection
Smaller specifications of the lifting table type CNC milling machine, the width of the table is more than 400mm below, it is most suitable for small and medium-sized parts processing and complex surface contour milling tasks. Larger specifications such as gantry milling machine, the table in 500-600mm above, used to solve the processing needs of large-size complex parts.
Selection of Machining Characteristics
For the machining part is a box-shaped plane or unequal steps at all levels, then the choice of point – linear system of CNC milling machine can be. If the machining part is a curved surface contour, it should be decided to choose two-coordinate linkage and three-coordinate linkage system according to the geometry of the surface. Can also be based on parts processing requirements, in general, on the basis of CNC milling machine, increase the CNC indexing head or CNC rotary table, this time the machine tool system for the four-coordinate CNC system, you can process the spiral groove, blade parts and so on.
CNC milling machine function
- the main functions of CNC milling machine
1) Point control function The point control of CNC milling machine is mainly used for hole processing of workpiece, such as center drill positioning, drilling, reaming, countersinking, reaming and boring, and other various hole processing operations.
2) Continuous control function Milling and processing the plane and surface of the workpiece through the linear interpolation, circular interpolation or complex curve interpolation movement of the CNC milling machine.
3) Tool radius compensation function
If directly programmed by the workpiece contour line, in the processing of the inner contour of the workpiece, the actual contour line will be larger than a tool radius value; in the processing of the outer contour of the workpiece, the actual contour line is smaller than a tool radius value. The use of tool radius compensation method, the CNC system automatically calculates the tool center trajectory, so that the tool center deviates from the contour of the workpiece a tool radius value, so as to process the contour in line with the requirements of the drawing. Utilizing the function of tool radius compensation, changing the amount of tool radius compensation can also compensate for the amount of tool wear and machining errors, to achieve roughing and finishing of the workpiece.
4)Tool Length Compensation Function Changing the compensation amount of tool length can compensate the length deviation value of the tool after tool change, and can also change the plane position of cutting machining to control the axial positioning accuracy of the tool.
5)Fixed cycle machining function By applying the fixed cycle machining instruction, the machining program can be simplified and the programming workload can be reduced.
6)Subroutine function If the shape of the workpiece is the same or similar part of the machining, it is written as a subroutine, which is called by the main program, so as to simplify the program structure. The function of referencing subroutines makes the processing program modular, and it is divided into a number of modules according to the process of processing, which are written as subroutines and called by the main program to complete the processing of the workpiece. This modular program is convenient for processing debugging, optimization of the machining process.
7) Special function Configuration of profiling software and profiling device on the CNC milling machine, using sensors to scan and collect data on the physical object, after data processing to automatically generate NC programs, and then realize the profiling of the workpiece to achieve reverse machining engineering. In short, after configuring certain software and hardware, it can expand the function of CNC milling machine.
CNC milling machine processing range
1) plane processing: CNC machine milling plane [1] can be divided into the horizontal plane of the workpiece (XY) processing, the positive plane of the workpiece (XZ) processing and the side plane of the workpiece (YZ) processing. As long as the use of two-axis half-control CNC milling machine can be completed so that the plane of the milling process.
2) surface machining: if milling complex surfaces need to use three-axis or even more axis linkage CNC milling machine.
CNC milling machine equipment
1) fixture CNC milling machine general-purpose fixtures are mainly flat jaws, magnetic suction cups and pressure plate device. For processing, large quantities or complex shape of the workpiece is to design a combination of fixtures, if the use of pneumatic and hydraulic fixtures, fixtures through the program control, to achieve the automatic loading and unloading of the workpiece, it can further improve work efficiency and reduce labor intensity.
2) Cutting tool Commonly used cutting tools are end milling cutter, face milling cutter, molding milling cutter and hole processing tool.