Within machining, an Automatic Tool Changer (ATC) is an invaluable addition to Computerized Numerical Control (CNC) machine tools. Its primary function is to enhance both production efficiency and the tool-carrying capacity of the machine. ATCs facilitate rapid tool changes, minimizing unproductive downtime. Typically, these systems are employed to bolster a machine’s capacity for utilizing various tools and also play a vital role in replacing worn or damaged tools. In essence, they represent a significant stride toward achieving full automation in machining processes.
The Development of Automatic Tool Changers
With the development of CNC technology, machining centers with automatic tool changer systems play an increasingly important role in modern manufacturing, which can shorten the product manufacturing cycle, improve the machining accuracy of products, suitable for flexible machining. An automatic tool changer system generally consists of a tool magazine, robot and drive device. The capacity of the tool magazine can be large or small, and the number of tools installed is between 20-180. The function of the tool magazine is to store the tools and send the next tool to be used to the tool change position accurately for the tool change robot to complete the exchange of new and old tools.
Importance of Automatic Tool Changers
Automatic Tool Changers (ATCs) are devices or mechanisms used in manufacturing, particularly in CNC (Computer Numerical Control) machines, to automate the process of changing cutting or machining tools during the production of parts. These tool changers play a fundamental role in enhancing the efficiency, productivity, and versatility of CNC machines. Here’s how they work and why they are important:
Automated Tool Changes
ATCs are designed to replace the need for manual tool changes in CNC machines. They can hold multiple tools simultaneously and automatically select and change the appropriate tool for a specific machining operation.
Tool Storage
ATCs typically have a tool storage magazine or carousel where a variety of cutting tools, such as end mills, drills, taps, and more, are stored. The magazine can hold a range of tool types and sizes.
Tool Selection
When a CNC machine requires a tool change to perform a different operation, the ATC selects the correct tool from the storage magazine. This selection is based on the tool required for the next step in the machining process.
Tool Change Process
The ATC then manipulates or moves the selected tool to the machine’s spindle, where it is securely clamped or installed. This process is precise and rapid, minimizing production downtime.
Improved Productivity
One of the primary benefits of ATCs is the significant reduction in non-productive time associated with manual tool changes. CNC machines equipped with ATCs can operate continuously, increasing productivity.
Enhanced Precision
ATCs ensure that tools are changed with high precision and consistency, reducing errors and contributing to the quality of the finished parts.
Versatility
The ability to store and switch between multiple tools enables CNC machines to perform a wide range of operations without manual intervention. This versatility is valuable for complex machining tasks.
Reduced Labor Costs
With ATCs, operators are not required to be present for every tool change, leading to reduced labor costs. It also minimizes the risk of human error during the tool change process.
Safety
ATCs promote workplace safety by eliminating the need for operators to handle heavy tools or perform frequent tool changes, reducing the risk of injuries.
Tool Monitoring
Some ATCs are equipped with tool monitoring systems that can detect tool wear or breakage. This proactive monitoring extends tool life and reduces the likelihood of producing defective parts.
Types of Automatic Tool Changers
Automatic Tool Changers (ATCs) come in several different types, each with specific mechanisms and features tailored to various CNC (Computer Numerical Control) machine applications. Here are some common types of ATCs:
Carousel (or Rotary) Automatic Tool Changer
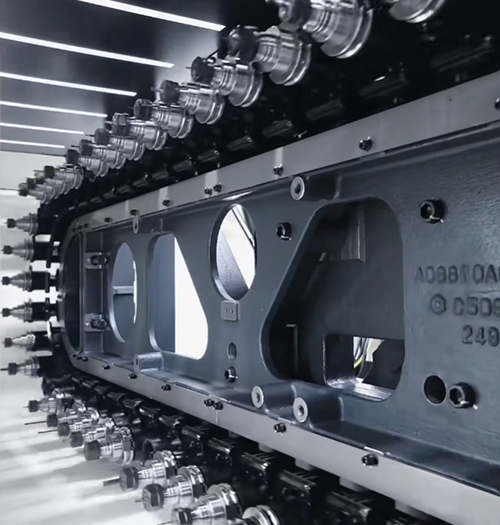
The Carousel Automatic Tool Changer also referred to as a Rotary ATC, is characterized by a horizontal circular tool magazine, resembling an umbrella, hence its umbrella-type designation.
Typically, this type of ATC is capable of accommodating a tool inventory ranging from 16 to 20 tools. During a tool change, the entire tool magazine moves below the spindle.
As the spindle tool slot aligns with the corresponding slot in the tool magazine, the spindle ascends, moving away from the tool. Concurrently, the tool magazine begins to rotate. When the tool changer reaches a position directly beneath the spindle, the spindle descends, allowing the tool to enter the taper hole of the spindle. Once the tool is securely clamped, the tool magazine returns to its initial position.
Carousel ATCs are lauded for their compact design, making efficient use of space within the CNC machine’s workspace. With a moderate tool capacity, they are well-suited for small to medium-sized CNC machines.
The choice of ATC type depends on the specific requirements of the CNC machine, including its size, the number of tools needed for the machining processes, available space, and the desired level of automation and tool change speed. Different industries and applications may prefer specific types of ATCs based on their unique needs and operational demands.
Gripping-type Automatic Tool Changer
The Gripping Type Automatic Tool Changer is a front-mounted tool magazine commonly found in CNC tapping centers. Small machining centers, such as those manufactured by Fanuc and Brother, often utilize this particular ATC design.
This type of automatic tool changer typically offers a tool capacity of either 16 or 21 pieces. It employs one-piece tool holder sets made from aluminum alloy, enabling swift assembly and replacement.
Notably, the Gripping Type ATC distinguishes itself by its direct tool change mechanism, located between the spindle and the tool magazine. Unlike other ATC designs with separate tool change arm structures, this arrangement reduces auxiliary tool change time.
As a result, the Gripping Type ATC boasts a relatively fast tool change speed, with adjacent tools being exchanged in under 1 second.
Arm-type Automatic Tool Changer
Arm ATC is the most common type of tool changer we see in vertical machining centers.
This type of ATC usually has a moderate tool capacity, 24 to 30PCS, and can accommodate a variety of spindle tapers, BT40 or BT50.
Arm-type tool changers feature a double-arm mechanism that allows for simultaneous tool exchange.
While one arm delivers the new tool to the spindle, the other arm retrieves the previously used tool from the spindle. Usually the tool change time is within 2 seconds.
This design enables faster tool changes, reducing the machine’s idle time. Arm-type tool changers are suitable for various CNC machines, including milling, turning, and multitasking centers.
Chain-type Automatic Tool Changer
Chain tool changers are equipped with a linear magazine, where tools are arranged in a chain-like formation.
Notably, they represent the most capacious automatic tool changers ever manufactured. The tool changer arm traverses along the chain to select the desired tool and deliver it to the spindle.
Chain tool changers typically offer a significantly larger tool capacity compared to carousel-style tool changers, making them suitable for accommodating larger tools. These Chain ATCs often provide a tool capacity ranging from 60 to 200 pieces, and they are typically customized to align with the specific requirements of the CNC machine in use.
These types of automatic tool changers are commonly employed in extensive machining setups such as large vertical machining centers, 5-axis machining centers, horizontal machining centers, double column machining centers, and similar applications.
Automatic Tool Changer Mechanism
Automatic Tool Changers employ various mechanisms to facilitate the automatic changing of tools in CNC (Computer Numerical Control) machines. The specific mechanism used can vary depending on the type of ATC and the design of the CNC machine. Here are some common mechanisms:
Rotary Carousel Mechanism:
- In this mechanism, tools are stored in a circular carousel or magazine.
- The carousel rotates to bring the selected tool to the spindle.
- The spindle or tool holder then clamps the tool in place.
Linear Magazine Mechanism:
- Tools are stored in a linear or rectangular magazine.
- The magazine moves vertically, horizontally, or rotationally to access the tools.
- The chosen tool is retrieved and clamped into the spindle.
Robotic Arm Mechanism:
- A robotic arm or robotic-like mechanism is employed to fetch and replace tools.
- The arm moves to the tool storage area, grasps the desired tool, and delivers it to the spindle for clamping.
Drum Mechanism:
- Tools are stored in a cylindrical drum or drum-like container.
- The drum rotates to position the required tool at the spindle.
- The spindle then locks the tool in place.
Swing-Arm Mechanism:
- A pivoting swing arm swings into the tool storage area to retrieve tools.
- It carries the selected tool to the spindle, where it is clamped.
Double-Arm Mechanism:
- This mechanism employs two robotic arms or grippers to exchange tools.
- The two arms can work in tandem to speed up the tool change process.
Shuttle Mechanism:
- Tools are stored on shuttle-like platforms or carriages.
- The shuttle moves to the spindle location, allowing for tool changes.
- It may use a linear or rotational motion to access the spindle.
Random-Access Mechanism:
- In this system, tools are arranged in separate stations, each housing a specific tool.
- The machine can access and change tools in any order, offering flexibility in tool selection.
The choice of mechanism depends on the design and size of the CNC machine, the number of tools required, the available space, and the desired speed and efficiency of the tool change process. Each mechanism has its own advantages and limitations, and CNC machine manufacturers select the most appropriate mechanism for a specific machine’s needs. Automatic tool changers significantly reduce downtime and increase the efficiency of CNC machining operations by allowing the machine to change tools without operator intervention.
Safety Measures
Safety measures are essential in any workplace to protect employees, machinery, and the environment. In industrial settings, especially those involving heavy machinery and potentially hazardous materials, implementing proper safety measures is of paramount importance. Here are some key safety measures commonly practiced in industrial environments:
Employee Training
Properly train all employees in the safe operation of equipment and machinery. Make sure they understand safety protocols and know how to respond to emergencies.
Protective Equipment
Provide and mandate the use of personal protective equipment (PPE), such as helmets, safety glasses, ear protection, gloves, and safety shoes, as needed.
Safety Signage
Clearly label hazardous areas, equipment, and materials with appropriate warning signs and instructions. This includes marking emergency exits and fire extinguisher locations.
Proper Ventilation
Ensure proper ventilation systems to remove dust, fumes, and other potentially harmful substances from the work environment. This is essential in environments with airborne contaminants.
Conclusion
In summary, CNC machine automatic tool changers are indispensable components that enhance the efficiency and capabilities of CNC machining processes. These systems streamline tool changes, reduce downtime, and improve precision, ultimately leading to increased productivity and the ability to handle diverse machining tasks. Automatic tool changers play a pivotal role in modern manufacturing, enabling machines to perform with consistency, versatility, and efficiency while minimizing the need for manual intervention.