In recent years, parts manufacturing techniques have undergone significant advancements to meet the evolving demands of various production sectors. Among these techniques, machining plays a fundamental role, involving the precise removal of material to craft high-precision components. This post delves into the distinctions between 3, 4, and 5-axis CNC machining, offering insights on selecting the appropriate CNC machine for your specific machining projects. Read on to discover the key differences and make informed choices for your manufacturing needs.
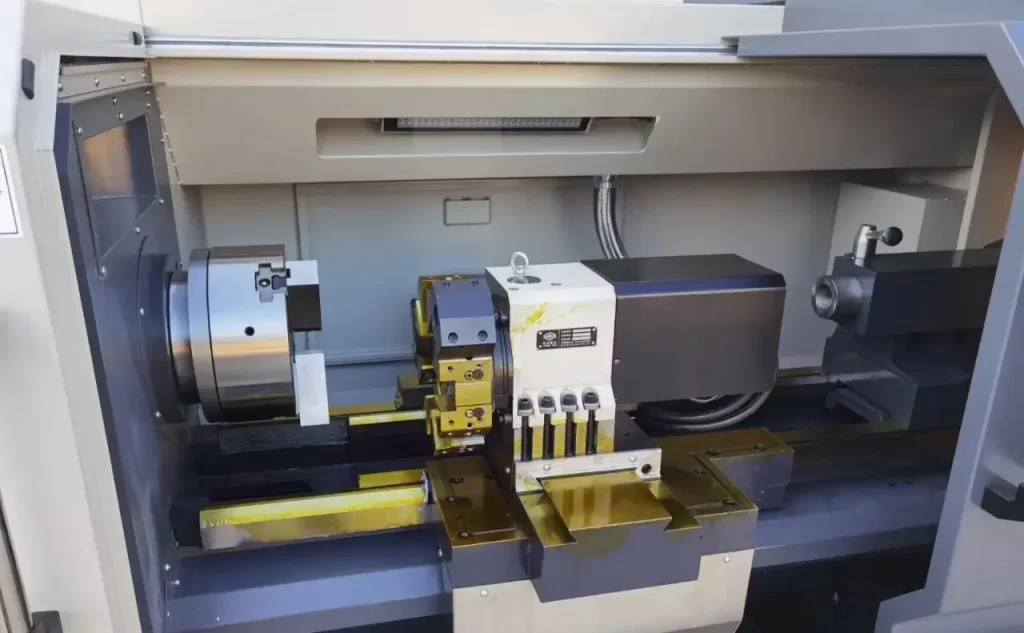
What is 3-Axis Milling:
3-axis milling is a machining process used in manufacturing to create parts and components by removing material from a workpiece. It is called “3-axis” because it involves the movement of a cutting tool along three primary axes: X, Y, and Z. Here’s what each axis represents:
X-Axis: This axis allows the cutting tool to move horizontally from left to right or right to left.
Y-Axis: The Y-axis permits the tool to move horizontally from front to back or back to front.
Z-Axis: The Z-axis enables the tool to move vertically, typically up and down.
3-axis milling is commonly used for a wide range of applications, including metalworking, woodworking, plastic fabrication, and more. It is suitable for producing parts with relatively simple geometries, flat surfaces, and slight contours. While it is a fundamental milling technique and widely applied, it may have limitations when working with highly complex or contoured workpieces. To machine more intricate shapes, 4-axis or 5-axis milling may be necessary to provide additional flexibility and precision in tool movement.
Advantages of 3-axis Milling:
Simplicity
3-axis milling is relatively straightforward to set up and program, making it accessible for a wide range of machining applications.
Cost-Effective
It is typically more cost-effective compared to higher-axis milling techniques, both in terms of machine costs and operation.
High Accuracy
While not as versatile as higher-axis milling, 3-axis machines can achieve high levels of precision, making them suitable for many common machining tasks.
Wide Applicability
4-axis milling can handle a variety of materials, including metals, plastics, and wood, and is used in diverse industries such as aerospace, automotive, and general manufacturing.
Reliable for Simple Parts
It is highly reliable for producing parts with flat or slightly contoured surfaces, such as plates, brackets, and basic components.
Ease of Maintenance
These machines are generally easier to maintain and repair due to their simpler design.
Short Learning Curve
Operators and programmers can become proficient relatively quickly, reducing training time and costs.
Widely Available
3-axis milling machines are readily available, making them accessible to many manufacturers.
Overall, the primary advantage of 3-axis milling is its simplicity and cost-effectiveness for manufacturing parts with straightforward geometries. It remains a foundational and valuable technique in the manufacturing industry for a wide range of applications.
What is 4-Axis Milling
4-axis milling is a machining process used in manufacturing to create parts and components by removing material from a workpiece. Unlike 3-axis milling, which operates along three primary axes (X, Y, and Z), 4-axis milling introduces an additional rotary axis, typically referred to as the A-axis. The key features of 4-axis milling include:
Three Linear Axes (X, Y, Z)
Just like in 3-axis milling, 4-axis milling retains the ability to move the cutting tool along three linear axes, enabling horizontal and vertical movement and cutting.
One Rotary Axis (A)
The A-axis introduces a rotary movement, allowing the cutting tool to tilt or swivel. This rotation can be continuous or limited to a specific range, depending on the machine’s design.
Multiple Sides Machining
The A-axis enables the tool to access and machine different sides of the workpiece, which is particularly valuable for complex parts that require machining from various angles.
5-axis milling is often employed when parts have features that cannot be accessed with traditional 3-axis machines, or when multiple faces of a workpiece need to be machined without manual repositioning. It is commonly used in industries like aerospace, automotive, and mold making, where intricate and three-dimensional components are prevalent. This milling technique strikes a balance between complexity and cost, offering versatility for a broader range of part geometries compared to 3-axis milling while remaining more affordable than 5-axis milling.
Advantages of 4-axis Milling:
Access to Multiple Sides
The additional rotary axis (A-axis) allows the cutting tool to access and machine different sides of a workpiece without repositioning, saving time and improving accuracy.
Complex Geometry
4-axis milling can handle more complex part geometries compared to 3-axis milling, making it suitable for components with undercuts and features that require machining from various angles.
Reduced Setup Time
Minimizing the need for workpiece repositioning or fixture changes reduces setup time, increasing overall efficiency.
Improved Surface Finish
The ability to approach parts from multiple angles can result in a better surface finish and improved overall part quality.
Versatility
It offers a balance between complexity and cost, providing versatility for a broader range of part geometries compared to 3-axis milling.
Suitable for Aerospace and Automotive Industries: 4-axis milling is commonly used in industries like aerospace and automotive, where complex and three-dimensional components are prevalent.
Reduced Manual Intervention
It reduces the need for manual intervention and repositioning of the workpiece, enhancing automation and accuracy in production processes.
Overall, 4-axis milling is a valuable technique for manufacturers who need to machine parts with complex geometries and multiple features but want to maintain cost efficiency. It strikes a balance between the capabilities of 5-axis milling and the simplicity of 3-axis milling.
What is 5-Axis Milling
5-axis milling is an advanced machining process used in manufacturing to create parts and components with intricate, complex, and highly contoured geometries. Unlike 3-axis and 4-axis milling, which operate along three primary linear axes (X, Y, Z) and one rotary axis (A), 5-axis milling introduces a second rotary axis (B), allowing for even greater flexibility in tool movement. The key features of 5-axis milling include:
Three Linear Axes (X, Y, Z)
Like 3-axis and 4-axis milling, 5-axis milling retains the ability to move the cutting tool along three linear axes, enabling horizontal, vertical, and depth movement.
Two Rotary Axes (A and B)
The additional B-axis provides rotational movement in addition to the A-axis, allowing for intricate and simultaneous tool movements. This means the tool can approach the workpiece from virtually any angle.
Complex and Contoured Geometries
5-axis milling is ideal for producing parts with complex shapes, undercuts, and intricate features, such as turbine blades, medical implants, aerospace components, and mold cavities.
Reduced Setup Time
Complex parts can often be machined in a single setup, reducing the time and effort required for workpiece repositioning and fixture changes.
Improved Surface Finish
Access to various angles results in a better surface finish, reducing the need for additional finishing processes.
5-axis milling is widely used in industries that demand precision and complex part geometries, such as aerospace, medical, automotive, and mold making. While it offers unparalleled capabilities, it is also more complex to program and operate than 3-axis or 4-axis milling and may require advanced CAD/CAM software and highly skilled machinists.
Advantages of 5 Axis Machining
In contrast to 3 and 4-axis milling machines, a 5-axis machine offers significantly enhanced design versatility. With five axes of movement, it can seamlessly maneuver around any corner or surface, enabling the creation of products that would be impractical on traditional 3 or 4-axis machines. Moreover, 3 and 4-axis machines rely on only two cutting tools: a horizontal spindle tool positioned above another swiveling vertical tool. Consequently, when working on projects like carving an apple using a CNC router or mill, the burden falls entirely on the horizontal spindle tool. It must maintain perfect parallelism along its X, Y, and Z axes while consistently engaging with the material. Conversely, a 5-axis machine boasts a total of three tools, comprising one vertical tool and two horizontal spindles. This setup allows for much more intricate and precise cuts, as it can utilize both right angles on a single piece of material to achieve superior results.
Conclusion
In conclusion, the distinctions between 3-axis, 4-axis, and 5-axis milling represent a spectrum of capabilities in the manufacturing industry.
3-axis milling, with its simplicity and cost-effectiveness, is suitable for producing basic parts with flat or slightly contoured surfaces but is limited in tackling intricate geometries.
4-axis milling introduces an additional rotary axis, enabling access to multiple sides of the workpiece and handling more complex parts, striking a balance between cost and versatility.
5-axis milling, the most advanced of the three, offers unparalleled freedom in machining highly complex, contoured components, making it indispensable in precision-critical industries. However, it requires advanced programming and expertise.
The choice among these techniques hinges on the specific requirements of a project, with 3-axis, 4-axis, or 5-axis milling being selected based on the complexity of the part, precision demands, and budget constraints. These milling methods collectively cater to the diverse needs of modern manufacturing, ensuring the production of a wide range of parts and components.