CNC machining, short for Computer Numerical Control machining, is a highly automated and precise manufacturing process used to create custom parts and components from various materials, such as metal, plastic, wood, and more. In CNC machining, computer programs and numerical control systems control the movement of cutting tools and machinery, allowing for the accurate and repeatable production of complex and detailed parts. It contains various machining techniques.
In this blog, we will discuss CNC turning, milling, and compound machining differences.
What Is Turning-milling Compound Machining?
Compound machining, often called turn-milling, is an advanced cutting process that combines turning and milling. This method leverages the milling cutter’s and workpiece’s simultaneous rotary motion to shape the workpiece with precision, meeting customers’ specific requirements, including shape accuracy, positional accuracy, and overall surface quality.
Turn-mill machining goes beyond merely combining turning and milling on a single machine; it utilizes the simultaneous and continuous motion of turning and milling to process various surfaces. By employing turn-mill services, customers can efficiently obtain CNC precision-machined parts in a shorter time frame and at a reduced cost. This versatile machining technique is also well-suited for mass production.
What Is A Turning-Milling Machine?
A turning milling machine, often referred to as a “turn-mill machine” or “mill-turn machine,” is a type of multi-axis CNC (Computer Numerical Control) machining center that combines both turning and milling capabilities in a single piece of equipment. These machines are designed for the efficient and simultaneous or sequential production of parts and components with complex geometries that require both rotational and axial machining operations.[1]
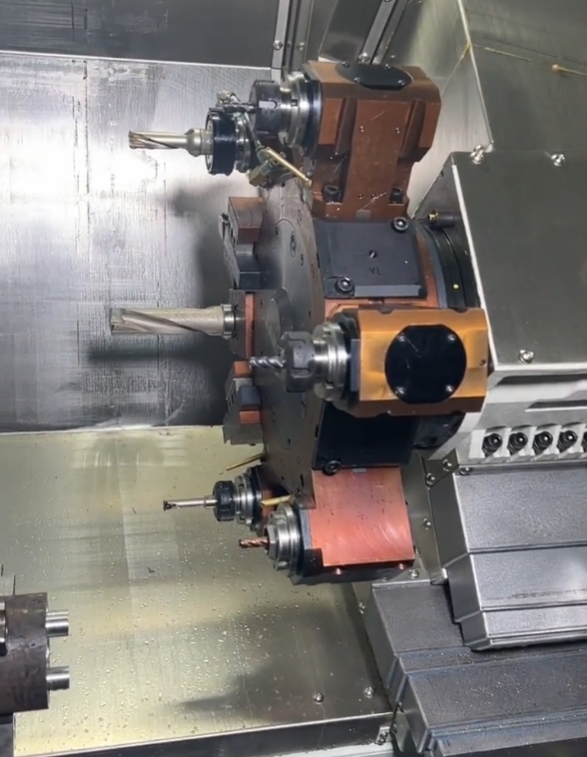
The movement of a turning-milling compound machine indeed involves four fundamental motions, each serving a specific purpose in the machining process:
Milling Cutter Rotation
This refers to the rotation of the milling tool or cutter, which is used for cutting and shaping the workpiece. The speed and direction of the cutter’s rotation can be controlled to determine the type of milling operation (e.g., face milling, profile milling, or contour milling).
Workpiece Rotation
Typically clamped in a chuck or other work-holding device, the workpiece can be rotated in the turning-milling machine. This rotation allows for turning operations, creating cylindrical or conical features on the workpiece. Workpiece rotation can be controlled in terms of speed and direction.
Milling Axial Feed
Milling axial feed refers to the milling tool’s linear movement along the workpiece’s axis. It controls the depth of cut during milling operations and removes material to create various features on the workpiece.
Radial Feed
Radial feed, also known as transverse feed, is the linear movement of the milling tool perpendicular to the workpiece’s rotational axis. It controls the width or profile of the material being removed during milling, and it is essential for achieving precise shapes and dimensions.
These four basic movements are carefully coordinated and controlled by the CNC system to perform turning and milling operations simultaneously or sequentially, depending on the specific requirements of the part being machined. Managing these movements precisely is a key advantage of turning-milling compound machines, enabling the efficient production of complex parts with diverse geometries.
Advantages of Turning-Milling Compound Machining:
The advantages of turning and milling compound machining are as follows:
Versatility: Turn-mill machines are highly versatile and capable of handling various part geometries and materials, offering flexibility to adapt to changing manufacturing needs.
Reduced Workpiece Handling: Since the workpiece remains secured in one setup during compound machining, there’s a reduced need for workpiece handling and repositioning, minimizing the potential for mishaps and improving overall efficiency.
Complex Geometry: Compound machining suits parts with intricate and complex geometries. This versatility is particularly valuable in aerospace, automotive, and medical industries, where complex shapes are common.
Reduced Setup Time: The one-clamping approach in compound machining significantly reduces setup times. This means less downtime and a faster transition from one operation to another. Additionally, it minimizes the potential for errors associated with workpiece transfers between different machines or setups.
Cost Savings: While the initial investment in a compound machining setup can be substantial, it often leads to cost savings in the long run. The reduction in setup times, improved overall efficiency, and the ability to create complex parts with a single machine can result in significant cost savings, particularly for complex components and larger production runs.
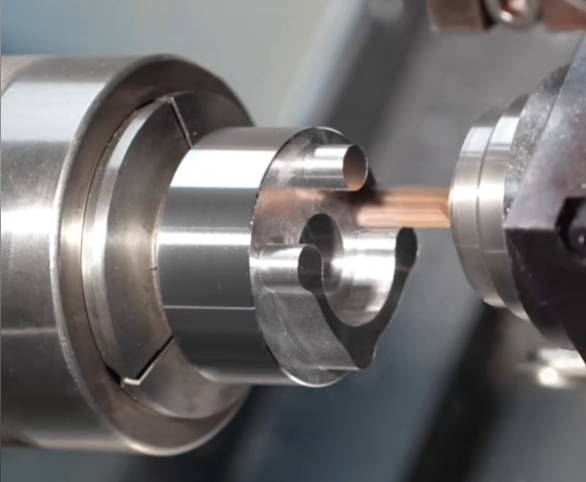
Applications and Industries
CNC turning and milling compound machining finds applications in a wide range of industries, particularly where high precision and versatility are essential. Some of the key industries and applications include:
Aerospace Industry
Components for aircraft engines and structures, such as turbine blades, landing gear parts, and airframe components. The ability to efficiently produce complex parts with tight tolerances is crucial in aerospace manufacturing.
Automotive Industry
Production of engine components, transmission parts, and suspension components. Complex components like crankshafts, camshafts, and gears benefit from the precision and efficiency of compound machining.
Medical Device Manufacturing
Surgical instruments, orthopedic implants, and medical equipment components. This industry’s ability to create intricate and custom-shaped medical devices is essential.
Energy Sector
Turbines, generators, and heat exchangers are parts of power generation equipment. For efficient energy production, complex shapes and high precision are required.
Die and Mold Making
Molds and dies are produced for various industries, including injection molding, die casting, and forging. Compound machining allows for the efficient production of complex molds and dies.
Tool and Die Industry
Manufacture of cutting tools, milling cutters, and complex tooling. Precision and versatility are crucial for producing high-quality tools and dies.
Defense and Military Manufacturing
Parts for military vehicles, weapons systems, and other defense-related equipment. The ability to create precision components is vital in this sector.
Electronics and Semiconductor Industry
Components for electronic devices and semiconductor manufacturing equipment. Compound machining benefits electronic components by allowing for the high precision and fine detail required.
Oil and Gas Industry
Production of components for drilling equipment, pumps, and valves. Complex shapes and precision are essential in harsh and demanding environments.
General Machining and Custom Parts
Custom components for various industries, including those requiring intricate shapes and features. Compound machining is used where high precision and the ability to handle complex geometries are essential.
Differences Between Turning-Milling Compound Machining and Other Machining
Turning-milling compound machining is distinct from other machining processes in several ways. Here are the key differences between turning-milling compound machining and some other standard machining techniques:
Precision and stable quality
The CNC turning and milling compound machine operates automatically, following a predefined program without manual intervention, eliminating the potential for human errors by the operator. Furthermore, the CNC machine tool boasts exceptional rigidity, accuracy, and the ability to maintain precise standards, contributing significantly to the stability of part quality during the machining process. Additionally, software can be harnessed to apply error compensation and correction, further enhancing the precision of CNC machining.[2]
Adaptability and flexibility
The CNC turning and milling compound machine tool employs CNC machining program control and offers the flexibility to automatically process new parts simply by modifying the CNC machining program. This adaptability addresses the ever-evolving demands of the competitive market, particularly in the context of continuous product enhancements.
Additionally, it effectively resolves the automation challenge posed by multi-variety, single-piece, and small-batch production. Notably, it fulfills the machining requirements for complex-shaped and profiled components in various manufacturing sectors, including aircraft, automotive, shipbuilding, power equipment, and more.
Production efficiency
The feed movement and most of the main movements of the CNC turning and milling compound machine tool feature stepless speed regulation. This offers a broad speed range to facilitate the selection of optimal cutting and feed speeds. It also enables real-time monitoring to prevent interruptions in CNC machine tool processing.
Automatic tool changes and the exchange of worktables are implemented to minimize tool change times. Simultaneous workpiece loading and unloading allow for one-clamping multi-face and multi-process processing, reducing auxiliary tasks like workpiece clamping and tool setup.
Consolidating processes in CNC machining decreases part turnaround time, resulting in high productivity, with general parts seeing up to a three to fourfold increase and complex parts experiencing even greater gains, potentially by tenfold or more.[3]
Modern production and management
The CNC turning and milling compound machine tool employs continuous speed adjustment for the feed and most primary motions, offering a wide speed range that allows for selecting appropriate cutting and feed speeds.
Online monitoring prevents downtime during CNC machine tool operations. Automatic tool changes and worktable exchanges minimize tool change times. Simultaneous workpiece loading and unloading enable one-clamping multi-face and multi-process processing, reducing ancillary tasks like workpiece clamping and tool setup.
Concentrating processes in CNC machining reduces the turnaround time for parts. As a result, CNC machining delivers high productivity, with general parts seeing a potential increase of three to fourfold and complex parts experiencing substantial gains, potentially by a factor of ten or even more.
Technical requirements for use and maintenance
The CNC turning and milling compound machine tool represents the culmination of various disciplines and innovative technologies. It commands a high price, with substantial upfront equipment investment. Consequently, the machine tool demands elevated standards for operation and maintenance. To ensure the holistic economic advantages of CNC machining, users and maintenance personnel must possess a high level of professional expertise.
Conclusion
In conclusion, CNC turning and milling compound machining represents a sophisticated and efficient manufacturing process that combines the capabilities of turning and milling in a single setup. This integration streamlines production, reduces setup times, and enhances efficiency, making it well-suited for industries that demand high precision and versatility.
Its ability to handle intricate part geometries, maintain consistent workpiece positioning, and minimize the need for workpiece handling underscores its significance in aerospace, automotive, and medical fields. While the initial investment may be substantial, the long-term benefits, including cost savings, higher productivity, and superior quality, make CNC turning and milling compound machining a vital technology in modern manufacturing.
References:
[1] Design of VLM20-FMC-Type Inverted Spindle CNC Turning-Milling Compound Flexible Machining Cell
[2] Error modeling and sensitivity analysis of turning-milling compound CNC machine tools