In the context of a substantial increase in the level of science and technology, industrial production in various fields began to widely use CNC machine tools, with the overall level of CNC machine tools increasingly improving, in the field of machining to bringing great economic and social benefits, in the production of CNC machine tools, to measure its overall quality, efficiency, an important indicator is the quality of machining. At present, the quality of CNC machine tool processing is closely related to the influence of more factors, such as the machine itself, processing methods, site management, etc., and to maximize the quality of machining, it is necessary to combine the various aspects of the influence of the factors to explore the corresponding means of prevention and control, to ensure that the function of the CNC machine tool, the role of the full play.
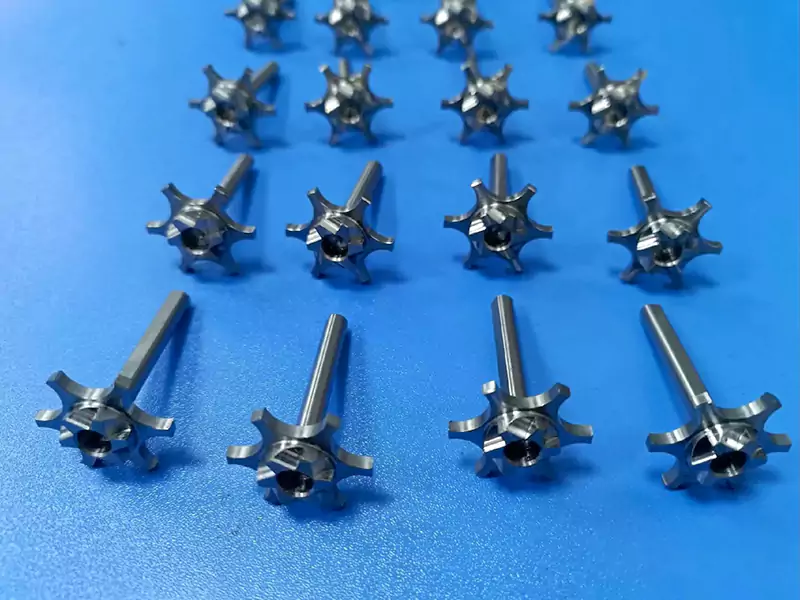
1. CNC machine tool processing quality factors
1.1 People and Process Factors
From the human factor aspect, in mechanical manufacturing, the essential composition contains people, and the human quality exists in an uneven situation, if the CNC machining operator’s skills and quality do not meet the actual requirements, will inevitably affect the quality of CNC machining. From the current point of view, in most of the CNC machining factories, a common problem is the grass-roots operator quality, the level in the state to be improved, the operation of the technology is not good enough, the attitude towards work there are certain problems, so to the quality of CNC machining has an impact. From the machining process point of view, the quality of CNC machining has a major influence is the machining process. Nowadays, all aspects of society have fully popularized computers, affected by this factor, traditional human-oriented processing technology has begun to change dramatically. From the point of view of the current processing technology, the main way is the combination of manual and computer, in which the impact of human quality can not be ignored. But in the context of the further development of information technology, will gradually improve the level of the CNC machining process, when the impact of human factors can be greatly avoided, and ultimately gradually improve the level of CNC machining quality.
1.2 Machine factors
First, the fixture. This equipment is mainly used for mold clamping operations. CNC machine tools, clamping molds to have high-precision features. Generally speaking, before the operation of the machine tool, the operator should fix the workpiece on the fixture, on this basis, start the machine tool, based on the set parameters to carry out production and processing operations. In this process, if the fixture for the mold for the clamping process, error is too large, the problem of processing the workpiece is not standard will arise, or even scrap. In addition, the operator clamping link, by the personnel factors affecting the fixture is too loose a phenomenon is very easy to appear, and the impact of this aspect of the problem to the processing quality should not be underestimated. Improper selection of fixtures or quality problems that exist, will also have an impact on processing quality. Second, the tool. In CNC machining, the “front line” is the tool and tool quality is closely related to the quality of the processed workpiece. The impact of the tool is mainly reflected in the following aspects:
① tool precision. In CNC machining, one of the main requirements is for the tool precision, to combine different precision requirements of the workpiece, the targeted selection of tools.
② tool material. Processing of different workpieces, the selected tool material should also show targeted. From the current point of view, super-hard materials metal ceramics, and other relatively widely used tool materials, once the material selection is not scientific, the quality of the processed workpiece will inevitably be affected.
③ tool size. CNC machining involves more types of workpieces, and the different shapes of workpieces, also need to take targeted tool size. If the size does not match the actual situation of the workpiece, it will restrict the processing of orderly progress.
④Tool shape. Processing workpiece has a variety of shapes, so the shape of the tool also has some special requirements. In the case of a curved surface workpiece, for example, to choosing a ball end milling cutter, if the shape of the selected tool does not meet the actual requirements, the corresponding workpiece processing is naturally difficult to carry out.
1.3 Error factors
A common factor affecting the quality of CNC machining is error, some of the error belongs to the objective existence, so the complete and total elimination of the goal is difficult to achieve, and these errors can only be based on artificial, technical, and other basis, so that the error is gradually reduced. At present, the machine, control system, processing, and other errors are common errors affecting the quality of CNC machining content.
① machine error. With the current CNC machine tools, and technological advances, the generation of error has been gradually reduced, but it is worth noting that the machine tool speeds up, and down, the time error is easy to appear, once such a situation occurs, the problem of overtraveling will arise, affecting the quality of machining.
② control system errors. The current CNC machine tools, involving open-loop, semi-closed-loop, and closed-loop three control systems, the accuracy of the above system for the incremental relationship. In the open-loop system, mostly used in economic machine tools, no position for system detection, and effective position detection is difficult to carry out, and even more unable to feedback workpiece displacement. In the case of low-precision workpiece processing, quality problems are very easy to appear. For semi-closed-loop systems, the table changes position and so on, it is very easy to affect the machine tool, a crisis in the quality of the workpiece. Closed-loop systems have high precision, but the rotation distance error is very easy to appear, resulting in the emergence of processing quality problems.
(iii) Errors in machining. Most of the error in this area is due to the tool as the main source, in general, in the case the tool is difficult to closely fit, the workpiece line deviation will appear, and the deviation is not due to the operation of the problem, which has existed in the design process, so it will cause a direct impact on the quality of machining.
2 CNC machining quality factors affecting the prevention and control measures
2.1 Strengthen the first-line operator training
The main body of the operation of CNC machine tools is the first-line operators, personnel skills, and literacy level will directly affect the quality of CNC machining. Therefore, the relevant enterprises should strengthen their efforts in personnel training and recruitment of professional operators.
① To recruit good personal qualities of the front-line personnel, and to ensure that the introduction of the front-line personnel with hard-working spirit, good attitude, and cultural level. At the same time, but also the need for enterprises from the first-line operators, targeted training, education, training to technical skills, professionalism, personal qualities, and other major content, plus the implementation of the necessary assessment, and then in the case of personnel through the assessment, to be arranged to the specific work position.
② Because the current CNC machine tool technology is in a state of gradual development, the factory has begun to appear some new technologies, new equipment, etc., at this time to make the new technologies, new equipment to be effective in the application of the new technology, to once again train the front-line staff, daily life should pay attention to the regular opening of the training courses to consolidate the personnel efficient, high-quality application of new technologies, new equipment basis for the enhancement of the efficiency of the factory for the smooth advancement of production to provide a guarantee. production to provide a guarantee for the smooth progress of production. In addition, due to the relative prominence of the dangers in CNC machining, so the regular opening of training, we should pay more attention to the issue of production safety, we should remind the front-line personnel to pay attention to production safety, based on the protection of personal safety, for the enterprise to create more efficient and effective, and to obtain to contribute to their own strength.
2.2 Selection of precision suitable CNC machine tool equipment
CNC machine tool precision in the processing of workpieces precision plays an important role in determining if the application of CNC machine tools does not have a high degree of accuracy, at this time in the processing of workpieces with high precision requirements, quality problems are bound to occur. At the same time, due to the differences in the control system of different precision CNC machine tools, the environment also has higher requirements. In this case, the factory needs to be based on different precision, for the appropriate precision CNC machine tools for selection.
From the current stage of the actual situation, some professional instruments are still mainly imported, but most of the independent production has been realized. From the current stage of most factories in the procurement of CNC machine tools, the cost control requirements are relatively stringent, some factories in order to prevent cost overruns from being circumvented, may not have a rigorous examination of the selected CNC machine tool manufacturers, unable to ensure that the accuracy of CNC machine tools to meet the processing of the actual needs of this time is also very difficult to process the perfect workpiece. In addition, in the case of the application of high-precision CNC machine tools, pay attention to the creation of a professional operating environment, such as a professional equipment room, etc., to create good conditions for the smooth operation of the machine tool.
2.3 Reasonable selection of tools and tool programs
In CNC machining, an extremely important and indispensable component is the tool, in the selection of tool science, is reasonable, and applicable, in order to maximize the quality of CNC machining, so operators need to carefully select the tool. CNC machine tools involve a wide range of types of tools, and different tool sizes, sizes, materials, shapes, etc. There are also differences, the operator needs to be based on the actual situation, will be the right tool to choose. From the current point of view, the relatively widely used tool material is the hard paper material, this type of material tool can be used in the workpiece processing with high precision requirements, but also has an idealized cutting speed.
But it is worth noting that not all CNC machining can choose this material tool to apply, the reason is that in some CNC machining in the application of this material props, the difficulty of the machining process may increase, ultimately leading to the emergence of the processing quality problems, so it is necessary to combine with the actual selection. In addition, the choice of tool walking program should not be ignored, because the basic guarantee of CNC machining accuracy is the tool walking program.
For CNC machining in the traditional knife program, its shortcomings in the current are increasingly prominent, resulting in CNC machining in the quality of the chances of a substantial increase in the problem. In the background of the increasing level of CNC machine tool technology, while the development of tool walking program. But it is worth noting that, because each knife program has the corresponding limiting factors, so to lay a solid foundation for the quality and accuracy of the workpiece, pay attention to the integration of a variety of roughing applications, based on the play of different advantages of different ways, so that the respective shortcomings can be effectively avoided to ensure that the accuracy of the requirements of the meet, so that the quality of the problem is effectively avoided.
2.4 Optimize the clamping mode of the mold
In CNC machining, one of the most important parts is the fixture, fixture strength size will give impact machining accuracy, so the clamping of the mold link, strictly control the clamping strength, so that the cutting error is effectively avoided. Adjustment of clamping force in the process, should be based on the mold material, low hardness mold, for example, to avoid applying too much clamping force, otherwise it can not provide a certain guarantee for the machining accuracy; and high hardness molds, you can increase the clamping force, to create favorable conditions to promote the normal operation of the mold, so that the accuracy of the appropriate workpiece cutting objectives effectively achieved.
In CNC machining, the operator needs to full and detailed understanding of the size and material of the mold, hardness, and other aspects of the situation, and then the mold clamping force to determine a good, but also to fully grasp the clamping position, so that the location of the improper impact of the mold balanced force, and ultimately damage to the mold and affect the quality of the phenomenon of the processing of the actual avoidance. For different molds, it is difficult to distinguish with the help of the naked eye its existing weak areas, so in the case of receiving a new mold, the need for professional and technical staff to determine the actual situation of the mold in a timely manner, and then based on a reasonable clamping position of the mold for the operator to facilitate the actual operation, to ensure the efficient operation of the machine tool. In general, in the case of improper mold clamping or damage to the mold, the operator’s personal safety will be jeopardized, and even serious accidents can be triggered. Therefore, it is necessary for the factory to take the mold clamping position as a foothold, will be a sound workflow to develop a good, so that improper operation caused by quality, safety, and other issues to minimized.
2.5 Compensation and prevention of errors in processing
In CNC machining, there are often objective errors that are difficult to avoid, so it is necessary to prevent and compensate in advance. Such as the surrounding environment, the machine tool location of high temperature and high humidity, high pressure, and other issues are actively avoided, to avoid the above factors to the normal advancement of CNC machining caused by the impact. For the operator, to fully understand the machine tool equipment, combined with the requirements of standardized, orderly operation of the corresponding operation, so as to effectively prevent and control improper operation, operating errors, and other errors. In addition, CNC technology thanks to the progress of science and technology, development began to gradually improve, and CNC machining also put forward more and more high precision requirements, standards, etc., at this time for some of the errors that can not be eliminated, you can with the technical means will cooperate to achieve the purpose of compensation. Such as pitch compensation, CNC machining due to the tool is difficult to close the line of motion deviation caused by the problem, you can use the technology to achieve the purpose of compensation, to promote the improvement of workpiece accuracy. However, it is worth noting that the application of the above technology still can not guarantee the complete elimination of errors, it can only achieve the purpose of substantial compensation. Another example is coordinate error compensation.
In CNC machining, the outermost part of the coordinate point position is not allowed to occur very easily, which ultimately leads to the resulting error. Based on the sensor detects the temperature of the position of the machine tool, and position changes in the coordinate point value recorded, and then gives full play to the function of its own analytical tools to achieve the goal of obtaining the corresponding compensation data, based on which a way to compensate for the machine tool control system is the compensation of the coordinate error. In addition to the above compensation measures, geometry, decoupling, and other compensation are also very common, but it is worth noting that this type of compensation should be used in conjunction with other means of compensation, so as to ensure a good compensation effect. However, the application of the above compensation methods, only to a certain extent to compensate for the error, is not able to make the error completely avoided. But from the current point of view, thanks to the increasing level of science and technology, CNC technology development, progress is accelerating, under this start, the error is getting smaller and smaller, and parts and components of the degree of refinement are also increasing, this time naturally able to gradually reduce the processing quality problems.
2.6 Focus on CNC machine tool programming design
CNC technology development so far has been and many technologies to achieve the goal of integration, such as computers, and based on the development of computer programming system control and other technologies, the role played in the processing of CNC machine tools can not be ignored. Among them, the application of programming technology can make the processing efficient, and quality is effectively controlled, but also convenient processing. However, it should not be ignored that programming still involves the operation of personnel, so the ability of personnel, and programming software effectiveness in CNC machining quality has a certain decisive role. To avoid the processing of quality problems effectively, the programming staff and programming software requirements are high.
① Programming personnel. The need for the factory to recruit a strong technical level, good personal qualities of the talent, and at the same time to the current stage of the new technology is constantly updated based on the necessary technical training to carry out the normal promotion of the programming work to provide a guarantee that this time can also be based on the programmer of the CNC machining process to be gradually optimized.
Programming software. At present, there are many programming software on the market, and the effect of different software also has a difference, the need for programmers in the programming software targeted selection, to ensure its quality at the same time, the smooth programming work, maintenance of processing quality, such as cimatron and other programming software, has been popularized in many of the CNC processing.
3. Conclusion
In the manufacturing industry, an extremely important part of the process is CNC machining, and the quality of CNC machining plays a decisive role in the development of the manufacturing industry. From the current stage of the CNC machining situation, the existence of various factors to the processing quality caused by the impact, so it is necessary to analyze and explore the impact factors, corresponding prevention and control means, and multi-pronged approach to protect the quality of processing.