If you’ve come across the terms “Turning” and “Milling” while exploring the CNC machining process, you might be wondering about their specifics and how they differ from each other. To shed light on these manufacturing processes, we’ll provide you with vital insights into their workings and the ideal applications for each. Continue reading to grasp a clear understanding of turning and milling, their respective capabilities, and which process might best suit your project.
What is CNC Turning?
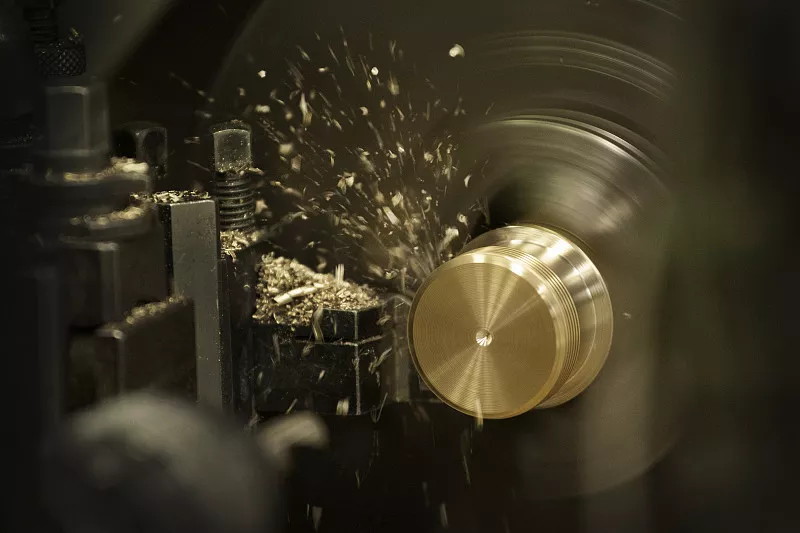
Despite the misconception that CNC turning is a recent innovation, it is, in fact, rooted in one of the oldest and simplest methods of part fabrication – the use of lathes. These machines come in horizontal or vertical configurations, chosen based on the workpiece’s weight, tolerance, and the raw materials used, which are typically round but can also be square or hexagonal in shape.
The primary function of a full CNC machine or turning center is to rotate or “turn” the workpiece, while its tools move in to remove excess material, shaping it as required. The initial step involves securing the material with a device known as a “chuck,” which then rotates at various speeds as specified by the machine.
In the past, lathes were operated manually, utilizing a series of turn wheels to move the chuck and workpiece back and forth for cutting. However, with modern advancements, CNC turning machines are now using computer numerical control, eliminating the need for constant manual supervision.
CNC turning is particularly well-suited for creating cylindrical parts, such as custom hollow tubing and shafts. Although it is possible to manufacture these components using 5-axis machining, opting for the turning method proves to be much more cost-effective and efficient.
What is CNC Milling?
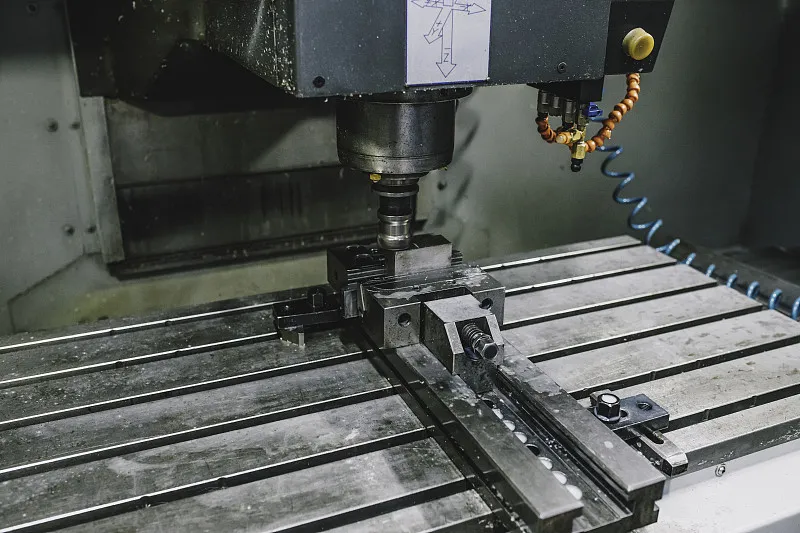
In contrast to CNC turning, which typically employs a single-point cutting tool, CNC milling utilizes multiple axes. The most conventional of these is the 3-axis system, allowing the cutting tool to move in three directions designated as X, Y, and Z.
While this 3-axis setup imposes some limitations on the geometry of the manufactured part, it is still sufficient for the majority of milling processes. Furthermore, there exists a diverse array of milling tools, each offering different cutting methods like end milling, hollow milling, and face milling.
For even greater flexibility, many CNC milling processes can be performed on four or more axes, which includes the rotation of both the tool and the worktable. Five-axis machines are particularly common, capable of fabricating a wide range of complex shapes and components that fall under the purview of CNC machining.
However, it’s essential to note that employing a five-axis machine is more expensive compared to its three-axis counterpart. Your precision engineering supplier can guide you through the decision-making process, ensuring that the chosen machine aligns with your project requirements, thus preventing unnecessary expenses.
Thanks to its remarkable capabilities, CNC milling is highly suitable for crafting intricate components such as custom tooling, complex mechanisms, enclosures, and engine parts.
Differences between CNC Turning and Milling
CNC Turning:
Cutting Tools
Primarily uses single-point cutting tools, such as inserts or drills.
Directions of Movement
The workpiece rotates on a spindle, while the cutting tool moves linearly along the axis parallel to the workpiece’s rotational axis (Z-axis). Some turning machines may also allow movement along the X-axis for additional operations.
Geometric Limitations
CNC turning is well-suited for creating cylindrical and symmetrical parts. It excels in producing components with circular cross-sections, such as shafts, pins, and cylinders. Turning is not ideal for complex shapes with multiple features and irregular geometries.
Part Complexity
CNC turning is better suited for relatively simple parts with straightforward geometries. It is efficient for producing parts that require rotational symmetry and minimal contouring.
Lower Setup Costs
CNC turning generally involves simpler setups and requires fewer tooling changes compared to milling, resulting in lower initial setup costs.
Faster Production
Turning operations can be faster for certain types of parts, especially those with rotational symmetry, as the continuous rotation of the workpiece allows for efficient material removal.
Material Savings
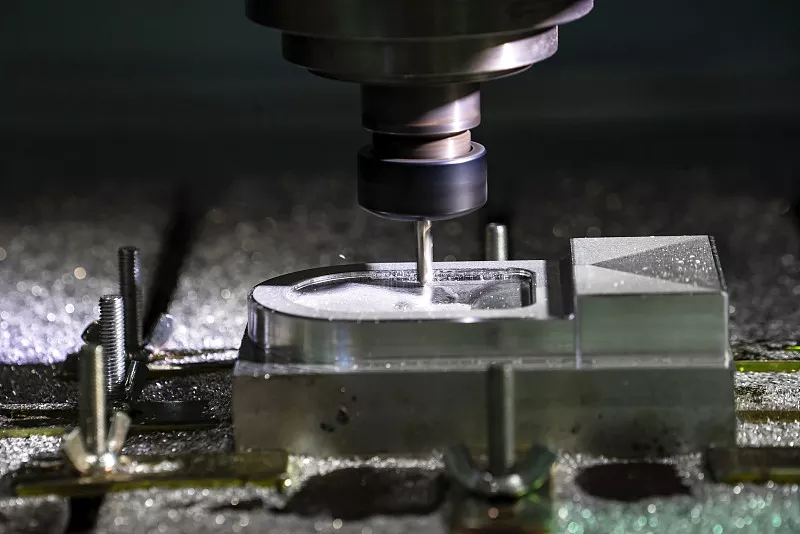
Turning typically generates less waste material, leading to potential material savings, especially for cylindrical parts.
CNC Milling:
Cutting Tools
Employs various cutting tools, including end mills, face mills, and special cutters, each suited for specific machining tasks.
Directions of Movement
CNC milling machines can move along three primary axes – X, Y, and Z. The X-axis represents horizontal movement from left to right, the Y-axis represents movement from front to back, and the Z-axis represents vertical movement up and down. Additionally, CNC milling machines may have 4th and 5th axes, enabling rotary movement of the cutting tool and workpiece, respectively, offering increased versatility.
Geometric Limitations
CNC milling offers greater geometric flexibility compared to turning. It can create a wide range of complex shapes, including pockets, slots, contours, and intricate 3D features. Milling allows for the production of parts with diverse geometries, making it suitable for more complex and customized components.
Part Complexity
CNC milling is capable of handling highly complex part designs. It is well-suited for the manufacturing process of intricate components with irregular shapes, undercuts, and features that require multi-axis movement. Milling excels in producing custom parts that demand precise and diverse machining operations.
Higher Setup Costs
CNC milling often requires more complex setups, multiple tool changes, and precise alignment for multi-axis operations, leading to higher initial setup costs compared to turning.
Longer Production Time
Milling operations may take longer due to the need for multiple tool changes, repositioning of the workpiece, and intricate cutting paths, especially for parts with complex geometries.
Material Waste
Milling processes can generate more waste material, particularly when removing excess material from intricate shapes, potentially leading to higher material costs.
Suitable Applications for CNC Turning
Cylindrical Parts
CNC turning is ideal for producing cylindrical components, such as shafts, rods, and pipes, due to its ability to create rotational symmetry with high precision.
Simple Symmetrical Parts
Turning is well-suited for manufacturing parts with straightforward symmetrical shapes, such as discs, washers, and bushings.
High-Volume Production
For projects involving high quantities of identical or similar parts, CNC turning’s efficient setup and rapid production make it a cost-effective choice.
Small to Medium-Sized Parts
Turning is advantageous for producing smaller to medium-sized components, as it can achieve high accuracy and surface finish in this size range.
Low to Medium Complexity
While not suitable for highly complex parts, CNC turning is effective for components with moderate complexity that can be achieved through rotational operations.
Suitable Applications for CNC Milling
Complex Geometries
CNC milling is the preferred method for creating intricate and complex shapes, such as contours, pockets, undercuts, and free-form surfaces.
Custom Parts
Milling allows for the production of highly customized parts tailored to specific design requirements, making it suitable for one-off or low-volume production.
Multi-Axis Machining
Projects that demand simultaneous cutting along multiple axes, including 4th and 5th-axis rotations, benefit from CNC milling’s versatility.
Prototype Development
Milling is well-suited for rapid prototyping and iterative design processes, enabling the creation of functional prototypes for testing and validation.
Larger Parts
CNC milling can handle larger workpieces, making it suitable for manufacturing components that exceed the capacity of CNC turning machines.
Materials with Complex Properties
Milling is effective for working with materials that require specific cutting techniques due to their hardness, brittleness, or composite nature.
Conclusion
The decision between CNC machining services should be based on the specific requirements of the project, including part complexity, batch size, budget constraints, and desired features. By understanding the strengths of each process, manufacturers can make informed choices to optimize efficiency, precision, and cost-effectiveness in their CNC machining endeavors. CapableMachining is able to help you select the right process for each project and ensure the successful realization of high-quality components that meet the needs of diverse industries and applications!
For more information on the differences between our CNC machines, milling and turning or to inquire about our other services, please contact us or request a quote.