The aviation manufacturing industry is important in promoting scientific and technological progress and economic development. It faces the challenge of processing high-precision, high-quality, and complex structural parts. Traditional processing methods cannot meet the aviation manufacturing industry’s demand for parts processing, and technical bottlenecks are gradually emerging. The introduction of high-precision machining technology can improve production efficiency and product quality, reduce costs, and enhance corporate competitiveness.
The development history of high-precision machining technology
1. Evolution of technical requirements for aviation manufacturing
With the rapid development of the aviation industry, the service life and safety of aircraft have become the focus of the aviation manufacturing industry. According to statistics, as the annual average growth rate of global civil aviation passenger traffic exceeds 5% (Figure 1), the average service life of aircraft is also increasing. At present, the service life of a large passenger aircraft has exceeded 20 years.
Therefore, the aviation manufacturing industry has placed higher requirements on the durability and reliability of components. For example, the fatigue life requirement of an aircraft fuselage structure is usually more than hundreds of thousands of flight cycles, while the reliability requirement of an aircraft engine is at the one-in-a-million level.
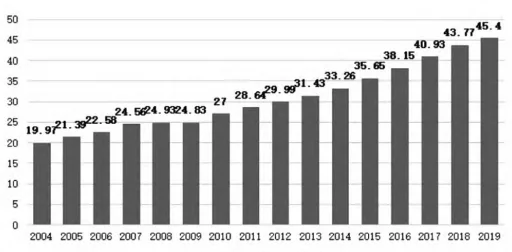
Figure 1 Global civil aviation passenger traffic from 2004 to 2019
2. Development history of high-precision machining technology
We can trace the development history of high-precision machining technology back to the Industrial Revolution. With the rise of the machinery industry and technological advancement, various machining equipment began to gradually appear.
The earliest mechanical processing equipment mainly operated manually, such as manual milling machines and manual lathes. Craftsmen relied on manual operation to complete the processing of workpieces, with low precision and low production efficiency.
It was not until the end of the 18th century that, with the advancement of the Industrial Revolution, the invention and application of the steam engine promoted the development of machining technology, and the first steam-driven mechanical lathe appeared, marking an important step in the direction of machining technology from manual operation to mechanized automation.
Commonly used high-precision machining equipment and tools
1. Characteristics and applications of CNC machine tools
Computers control CNC machine tools, determining the motion trajectory and processing parameters based on pre-input program instructions. Aviation manufacturing widely uses CNC machine tools, which exhibit high precision, high efficiency, and strong flexibility.
High precision. Through computer control systems, CNC machine tools can achieve high-precision processing that strictly requires the accuracy of parts in aviation manufacturing. For example, CNC machine tools can meet the processing needs of high-precision parts, such as aircraft engine blades, aerospace structural parts, etc., and achieve micron-level size control and surface roughness processing.
High efficiency. CNC machine tools have high processing speed and short processing cycles, which can greatly improve production efficiency. Compared with traditional mechanical processing equipment, they have great advantages. CNC machine tools can realize automatic continuous processing in aviation manufacturing, which greatly shortens the processing cycle, improves production efficiency, and reduces production costs.
In aviation manufacturing, the flexibility of CNC machine tools can meet the processing needs of different parts and improve the flexibility and adaptability of production, because there are many types of parts and different production batches.
2. The role and development of cutting tools in aviation manufacturing
Cutting tools are crucial tools in mechanical processing. CNC machine tools directly process the shape and surface of parts, playing a vital role in ensuring processing quality and efficiency. In aviation manufacturing, the role of cutting tools is particularly prominent, and its development has also experienced great progress.
The continuous development of aviation materials, such as the widespread application of high-strength steel and titanium alloy composite materials, places higher requirements on cutting tool materials and processes.
Traditional high-speed steel tools can no longer meet the processing requirements of high-hardness and high-strength materials. Therefore, various new tool materials have emerged, such as carbide tools, ceramic tools, super-hard tools, etc. The new tool materials have the characteristics of high hardness, strong wear resistance, good high-temperature resistance, etc., which can meet the processing requirements of complex materials.
For example, the emergence of new tool structures such as multi-edge tools and adjustable tools has significantly improved the processing efficiency and stability of tools, which can meet the requirements of different processing needs and processing environments.
3. The influence of processing technology on high-precision machining
Processing technology plays a vital role in high-precision machining, which directly affects the quality, efficiency, and cost of parts processing. First of all, the choice of processing technology.
Different processing technologies have different requirements for processing accuracy and surface quality, and it is necessary to make reasonable selections based on the requirements of the part’s shape, material, accuracy, etc.
For example, high-precision equipment such as CNC machine tools are usually used to process parts that require high-precision processing to ensure stable and consistent processing accuracy.
Secondly, the processing quality and processing efficiency, stability, and controllability of the processing technology are essential. A good processing technology should have the characteristics of stable processing technology and controllable processing parameters and can ensure parts with stable and consistent processing accuracy and stable and consistent surface quality.
Parameters such as processing speed, feed speed, cutting depth, etc. need to be reasonably set during the CNC machine tool processing process to ensure the processing quality and efficiency of the parts.
Finally, to improve processing efficiency and quality, innovation, and improvement of processing technology are also essential.
Application of New Processing Technology in Aviation Manufacturing
1. Laser processing technology
Laser processing technology is an advanced processing method that uses high-energy-density laser beams to process materials on workpieces.
The principle is to use the laser beam generated by the laser, focus the laser through a lens or a reflector, and concentrate its energy density into a very small area, to achieve instantaneous heating, melting, or evaporation of the material, thereby realizing processing operations such as cutting, punching, and engraving, so that the energy density of the laser reaches a smaller intensity, as shown in Figure 2.
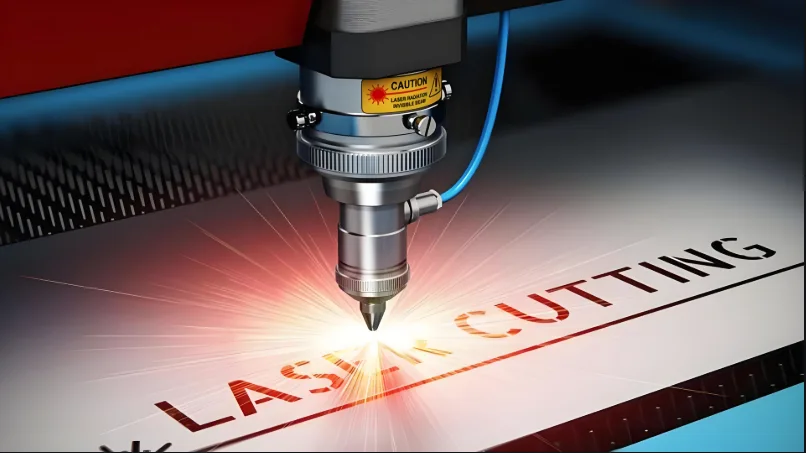
Figure 2 Laser processing technology
The significant advantages of laser processing technology are as follows:
(1)Laser processing has extremely high precision. The beam diameter can reach tens of microns. After focusing, it can form a tiny cutting point, which meets the processing requirements of high-precision parts in aviation manufacturing, such as engine blades and turbine disks.
(2)Laser processing is suitable for metals, non-metals, and composite materials, such as steel, aluminum, titanium alloys, ceramics, and plastics, and can meet the processing requirements of complex materials in aviation manufacturing, such as cutting, drilling,g and surface treatment of high-strength and high-hardness materials.
(3)Laser processing has a small heat-affected zone. Laser processing is a non-contact method. The laser beam acts directly on the workpiece surface, avoiding tool contact and reducing the effects of thermal deformation and mechanical stress. The heat-affected zone is usually only a few microns, which can finely process materials, reduce deformation, and improve processing accuracy.
2. Electrochemical machining technology
Electrochemical machining technology plays an important role in the processing of complex parts, especially in aviation manufacturing. It is not limited by the shape of the workpiece and can precisely process complex parts such as turbine blades to meet high precision and surface quality requirements, thereby improving processing efficiency and quality.
Microhole processing is common in aviation manufacturing, such as engine jet holes and turbine blade cooling holes. Electrochemical machining technology can precisely process micro holes, control the hole diameter and shape, and improve processing quality and performance. This technology is suitable for high-hardness materials such as titanium alloys and high-strength steel, improving processing accuracy and surface quality, and reducing costs and working hours.
Application and Prospects
With the continuous development and technological progress of the aviation industry, the demand for parts is becoming more and more complex. First, the requirements for processing accuracy and surface quality are getting higher and higher. Second, the widespread application of new materials such as composite materials and ultra-high strength steel will continue to increase the requirements for processing technology.
High-precision machining technology will become one of the important development directions of future aviation manufacturing.
Summarize
High-precision machining technology can not only meet the high requirements of aircraft parts for accuracy and surface quality but also promote the sustainable development and progress of the aviation manufacturing industry.
In the future, with the continuous advancement of aviation manufacturing technology and the continuous development of high-precision machining technology, I believe that high-precision machining technology will play a more important role in the field of aviation manufacturing, inject new vitality into the development of aviation manufacturing industry, promote the continuous improvement of aircraft performance, and make greater contributions to the aviation industry.