Since CNC (Computer Numerical Control) machining technology emerged in the 1950s, engineers have
developed it from simple lathes into advanced multi-axis machine tools. This development has greatly enhanced machining capabilities. CNC technology reduces human error, improves precision, and ensures consistent quality. It plays a key role in raising the overall quality of mold manufacturing.
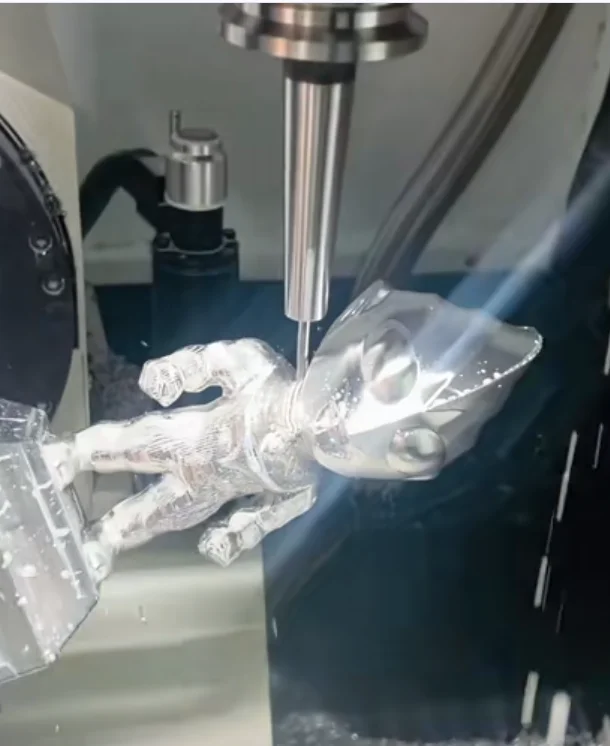
1 Basic Principles of CNC Machining Technology
CNC machining uses computer programs to guide machine tools. It provides automation and high precision. The system includes several main components:
CNC System: The computer processes instructions. Control software and hardware interfaces transmit these instructions to the machine.
Processing Software: This software uses CNC codes to give commands.
Servo System: Servo motors and drivers move the spindle, tool, and worktable along specific paths.
2 Requirements for CNC Machining in Mechanical Mold Manufacturing
2.1 Defining Processing Technology
Engineers must select the right tools and cutting techniques based on the material. Complex mold structures require advanced methods. These include five-axis machining, EDM, and milling. These technologies handle detailed surfaces and shapes better.
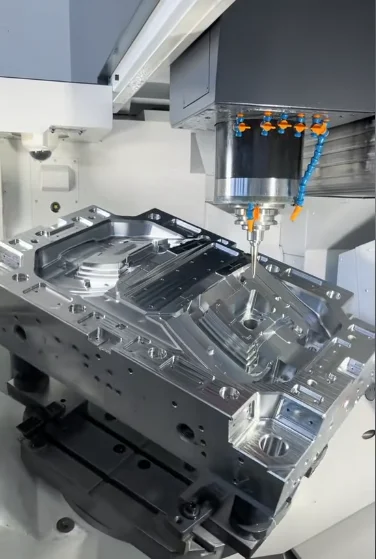
2.2 Setting Processing Parameters
Operators must set precise parameters to ensure accuracy and reduce waste. They use CAD/CAM to confirm 3D models. Then, they choose processing methods based on material stability and wear resistance. These steps help extend mold life.
2.3 Manufacturing Principles
Most molds are custom-made. So, programmers must write accurate programs to avoid repeated mold adjustments. They follow clear steps and control cutting parameters to reduce errors. They also select suitable clamping methods to keep the workpiece stable.
3 Applications of CNC Technologies in Mold Processing
3.1 CNC EDM (Electrical Discharge Machining)
EDM machines hard materials with high precision. This technique is ideal for complex molds, such as engine parts. It improves accuracy and solves problems that traditional tools cannot.
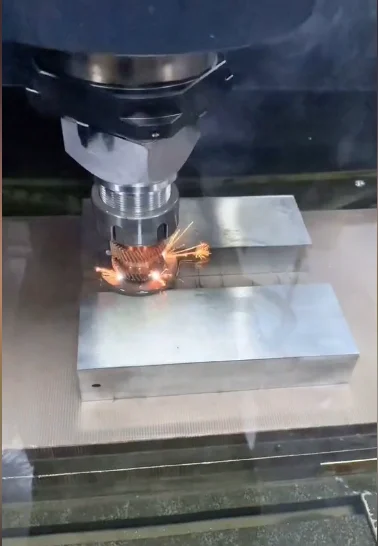
3.2 CNC Milling
Operators use milling to shape surfaces and edges. It offers high flexibility and precision. It works well for detailed mold components.
3.3 CNC Turning
Turning machines create external surfaces, holes, and threads. This method provides high speed and accuracy. It’s especially useful for aerospace engine and gearbox parts.
3.4 Electrochemical Machining
Technicians apply electric current to remove impurities from the metal surface. They also use CNC control to apply current for electroplating. This process creates corrosion-resistant coatings and detailed patterns.
3.5 Ultrasonic Technology
Machines use high-frequency vibration to clean tools and perform cold welding. This process extends tool life. It also enables plastic welding through heat and friction.
4 Key Applications of CNC in Mold Making
4.1 Processing Database Management
Engineers record tools, cutting conditions, and machining time in a database. This helps them work more efficiently and spot problems early. They use the data to improve future processing.
4.2 Geometric Error Control
Workers use measuring tools and adjust the machine to reduce shape errors. They apply compensation techniques to fine-tune the tool path. They also simulate the machining process to detect and fix problems in advance.
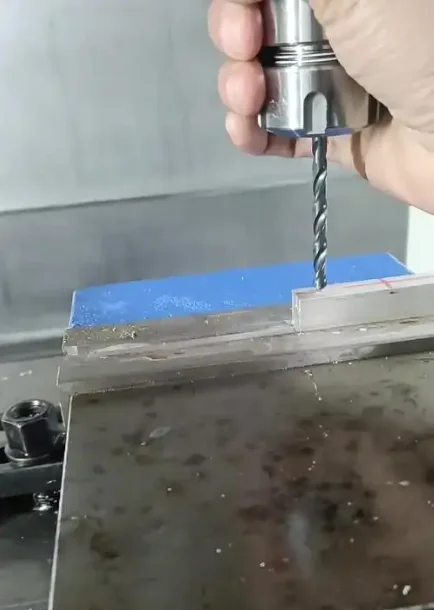
4.3 Mold Information Collection
Technicians monitor temperature and vibration with sensors. They adjust the cutting speed and cooling in real time. This prevents deformation and reduces the risk of equipment failure.
4.4 Tool Path Optimization
Operators plan tool paths carefully to improve efficiency. They use AI and simulation tools to optimize movement. They also consider the fixture’s shape and structure to keep the mold stable during machining.
5 Conclusion
CNC machining plays an essential role in modern mold manufacturing. When used properly, it increases precision, lowers costs, and improves production efficiency. This makes CNC a valuable tool for advancing the mechanical mold industry in China.