Currently, profile threads are mainly used in production machinery for plastics, rubber and puffed food. This is mainly because the profile thread has the characteristics of high speed, accuracy and stability, which is the important foundation of industrial production [1]. In the basic equipment of the plastics and rubber industries, the profile thread screw is an indispensable component, mainly because the profile thread screw has a high speed, accuracy and stability, which is an important basis for industrial production [1].
Screw in the processing and manufacturing process, can well avoid the problem of pitch change such as slot width; and this kind of shaped thread screw performance is good, more material, at the same time can change the compression ratio, applied in the feeding structure, can realize high-speed conveying and quantitative conveying.
1. Overview of profiled thread
1.1 Characteristics and Classification of Shaped Threads
Shaped thread refers to non-standard threads, that is, the size and shape and parameters of shaped threads are completely different from the existing national thread standards. Shaped threads generally refer to the tooth profile threads, the bottom diameter of the threads, and the traditional triangular threads, trapezoidal threads and so on. Comprehensively all the features of heteromorphic threads can be specifically divided into four categories: first, body heteromorphic threads, i.e., processed threads constituted on non-circular curves; second, tooth-type heteromorphic threads with the top of the tooth as a circular arc; third, variable-pitch threads, i.e., the pitch of the threads will be regularly varied as the helix is rotated; and fourth, the composite of body heteromorphisms, tooth-type heteromorphisms and torque-variable screws, i.e., the ability to satisfy two or three of the above mentioned situations at the same time [2 ].
1.2 Processing methods of shaped threads
(1) Conventional milling and cutting method. Using the helical rotation of the screw, the blade of the helical rod can mill the required thread shape on the part while moving at a variable speed.
(2) The cutting method realized by the variable-speed movement of the tool on an ordinary machine tool, i.e., adding a cam device for shaped threads to an ordinary machine tool, and machining by means of variable-speed movement. Compared with the first operation method, this operation method is simpler to operate and the quality is more stable; the disadvantage is that the change of the thread needs to change with the change of the cam, so it is more suitable for the fixed type of shaped thread [3].
(3) Modification of CNC lathe machining method. The CNC lathe processing method is to process the variable pitch screw by means of multi-coordinate linkage, which is also a more ideal processing method at present. The internal calculation is utilized to calculate the trajectory movement of the function curves of the different stages of the screw, and the corresponding programming system is developed [4]. However, the disadvantage of this processing method is that the cost of processing is high, and is generally only applied to high-precision product processing.
(4) Segmented processing method of variable pitch screw. Segmented processing method is mainly to avoid the use of milling method by the screw length limitations, which causes screw vibration problems. The advantage of the segmented processing method of variable-pitch screws is that after the completion of the processing can be machined inside the keyway or spline groove, and a long shaft with a keyway for connection.
(5) The use of CNC turning centers, that is, on the basis of turning processing with the relevant power tool to process the required shaped threads.
(6) CNC grinding machine, i.e., in the processing of thread surface roughness and high precision of the fit of shaped threads, can be used in the way of CNC grinding machine processing. Through the quenching treatment of the thread profile after the selection of CNC grinding machine for processing. In general, there are various ways of CNC machining of profiled threads, which need to be selected according to their own needs.
2 Features of CNC machining technology for shaped threads
Profiled thread CNC machining technology is currently a wider range of applications, and the practicality of one of the stronger processing technology. Therefore, in the actual operation process, it is necessary to effectively master the characteristics of CNC machining technology of profiled threads, so as to better improve the CNC machining technology of profiled threads. The characteristics of CNC machining technology for shaped threads are specifically reflected in the following five aspects:
(1) It has strong practicality in changing the shape of products. For the contour thread CNC machining technology, when the shape of the product is changed, it is only necessary to re-program the corresponding program on the CNC machining machine to change the original shape of the product and form a new shape. Therefore, shaped thread CNC machining technology is a technology that can quickly change the shape of the parts, providing great convenience for the mass production of parts.
(2) Shaped thread CNC machining technology is more suitable for processing parts with more complex surface shapes. This is mainly because the CNC machine tool has superior computing power, and with the programming software development more and more advanced and perfect, the use of profiled thread CNC machining technology can more accurately calculate the amount of movement of the coordinate axis of each part; and ordinary machine tools can not realize this function, so the profiled thread CNC machining technology in the machining of more complex parts has a greater advantage.
(3) The parts processed by CNC machining technology of profiled thread have higher precision and more stable quality. The CNC machining of shaped threads is programmed based on the coordinates of the nodes of the parts, and the machine tool is operated by the stepping motor driving the ball screw, and the repeated positioning of the machine tool in the process of operation reduces the errors that may occur, so that the parts produced are basically the same. At the same time, in the operation process, only need to ensure that the program is correct, the correct size, can make the mass production of higher accuracy, more stable quality parts.
(4) Higher degree of automation of CNC machining technology for shaped threads. CNC machining is mainly based on parts of the drawing or computer programming to obtain parts processing program. Therefore, it is necessary for the operator of the machine tool to realize the production goal through the control medium or control transmission system [5]. In recent years, with the improvement and development of CNC machining technology for profiled threads, existing CNC machining machines are generally equipped with the corresponding automatic feeding function and automatic chip removal system, which does not require complex manual operation and greatly reduces the intensity of the work of production and processing.
(5) Higher production efficiency of CNC machining technology for shaped threads. With the rapid development of CNC machine tool technology, the spindle speed of CNC machine tools and the range of feed volume is also expanding, each of which can be programmed to choose the optimal amount of cutting for each supply and demand, thus saving the time of maneuvering. In addition, most of the CNC machine tools use acceleration and deceleration control to shorten the time required for positioning and operation, so the efficient way of working also greatly promotes the improvement of CNC machining technology for profiled threads.
3. Selection of cutting parameters for CNC machining of profiled threads
In the process of CNC machining of profiled thread, reasonable selection of cutting parameters is the key to improve product quality, increase production efficiency and reduce production costs. At present, the cutting parameters of CNC machine tools are mostly selected by experience or through the cutting parameters of the manual to choose. Specifically including the parameters used on the CNC inserts are generally labeled with the reference value of the optimal speed of the cutting material. However, in the actual selection process, need to take into account the basic properties of the processed material and the material properties of the selected tool. In the process of selecting the tool, the cutting parameters include three aspects, i.e., back draft, cutting speed and feed, as shown in Table 1.
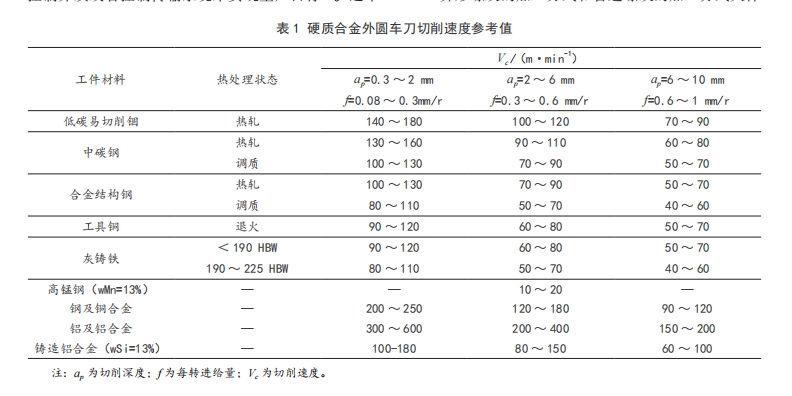
4. Programming mode of CNC machining of profiled threads
The machining mode of shaped thread and the machining mode of common thread are generally the same, but there are differences in the two programming modes of manual programming and computer-aided programming.
4.1 Manual Programming
In the shaped thread CNC machining technology, CNC manual programming refers to the programming personnel to get the corresponding processing parts and drawings, you need to first analyze the parts drawings, and to determine the way of machining process, in the selection and programming instructions, the complete program will be input into the entire CNC system, in the absence of computer-aided software written programming is the CNC machine tool manual programming. In the process of parts processing, if the shape of the part is relatively simple, there is no problem of irregular surfaces, generally can be directly programmed by means of manual programming. This can not only save the time of graphic drawing and selection of parameters, but also eliminate the selection of tools and other unnecessary steps. However, if the shape of the parts to be machined is more complex, it is necessary to take the computer-aided programming approach to improve the stability of CNC machining of shaped threads. This is mainly due to the face of more complex parts, manual programming on the calculation of node coordinates will produce a huge workload, greatly increasing the workload and working time, in the input process will also take more time, and manual calculation of the existence of the error is larger, so the manual programming is not applicable to the more complex parts CNC machining.
(1) Shaped thread CNC machining technology in manual programming has
Certain advantages. First of all, for the programming of CNC machine tools, manual programming is not a high requirement for learners, only need learners to master the corresponding program format, in a short period of time can be flexibly applied to a variety of parts with similar shapes. In terms of cost, compared to automatic computer programming, manual programming processing costs are lower, so manual programming is the basis of programming. Secondly, in the process of manual programming, it is necessary for programmers to have a clearer overall idea of parts processing. Problems occurring in the programming process, the programmer can find out where the problem lies in a timely manner and make modifications. Finally, CNC machining programmers on parts processing ideas can be expressed through the CNC language. Especially with the longer working time, working experience is also more and more rich, programmers in the process of operation can be based on their own experience to select the relevant parameters, and there is no excessive calculation content, so to some extent, the program prepared by hand has the characteristics of safety and effectiveness.
(2) Shaped thread CNC machining technology in terms of manual programming
There are also certain disadvantages. First of all, because the drawings have different requirements on dimension marking and national standards, so in the manual programming of CNC, the programmer needs to find out the corresponding coordinate points through a lot of arithmetic, and the possibility of error in the manual calculation results is higher, which affects the accuracy of the parts processing. Secondly, in the process of CNC machining for the same shape and size of different parts, designers usually use the form of tables or functions to express the size of the parts, which brings greater difficulties in the calculation of CNC manual programmers, if the programming calculation of a large error will lead to the scrapping of the products produced, which will bring greater economic losses to the enterprise, affecting the production schedule and the efficiency of the enterprise. The production schedule and enterprise benefit will be affected.
4.2 Computerized Automatic Programming
Programmers of CNC machining of profiled threads generally use automatic computer programming for profiled thread parts processing, through the computer programming software to draw the contour of the parts on the machining drawings, and according to the software’s menu requirements to select the appropriate processing tools and processing methods, key in the appropriate processing parameters, generate the appropriate tool path, and finally select the appropriate processor to generate the CNC machine tools can recognize the programming language. Programming language that can be recognized.
In the programming language, you need to express the specific shape of the part, and use the CNC system to perform the relevant sequence of actions, especially after determining the parameters of the CNC machining process, you also need to record and program the path and trajectory of the CNC tool. This type of programming can only process simple parts in the form of external machining, but cannot realize the processing of complex parts. In addition, the prepared program is not directly recognized by the profile thread CNC machining system, and thus cannot be used directly. In addition, the programming method needs to be compiled in order to generate a new CNC operating program. This method of programming does not effectively verify that the tool trajectory is consistent with the machining drawings after compilation, thus increasing the risk of the programming control.