In the process of developing the modern manufacturing industry, CNC machine tools are key equipment for machining. As the precision and complexity of mechanical parts and components continue to improve, manufacturers must use machine tools to meet higher processing efficiency requirements.
At this stage, companies mainly conduct research on improving CNC machine tool machining efficiency at the management level. It analyzes the factors affecting machining efficiency from the perspective of daily equipment management, personnel operation, etc., and proposes countermeasures to strengthen the management of the machining production process.
However, the processing technology adopted directly affects the actual CNC machine tool production efficiency. Therefore, we should explore in depth how to enhance the machining efficiency of machine tools and promote the development of CNC machining technology.
1. CNC machine tool machining efficiency improvement necessity
Machinery manufacturing is an important pillar of the national economy, in the context of increasingly fierce competition in the international market, Southeast Asian countries in the field of machinery manufacturing have gradually lost the advantage of labor costs, prompting the development of machining in the direction of high efficiency and low cost.
Enhancing the efficiency of CNC machine tool machining, first of all, can shorten the product production cycle, and improve enterprise capacity utilization, to help enterprises respond faster to market diversification needs, by providing differentiated products to obtain core competitiveness.
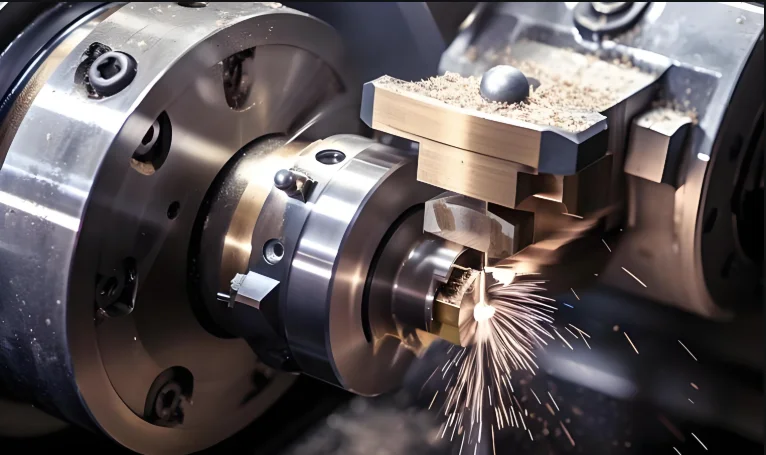
Secondly, the introduction of modern science and technology to promote the development of CNC machining technology, improve the efficiency of machine tool machining, through scientific and technological innovation for industry empowerment, and further realize the deep processing of various mechanical products, precision processing, enhance the added value of the product, to create more industrial value.
Finally, CNC machine tool machining efficiency, meaning that the domestic manufacturing industry has gradually reached the international level, you can use high-grade CNC machine tools to achieve machining, with low manpower, material, and other cost inputs to obtain the optimal production results, and effectively save resources at the same time, reflecting the technological advancement.
Therefore, whether from the micro, meso, or macro point of view, it is necessary to improve the efficiency of CNC machine tool machining, to promote the sustainable development of the modern manufacturing industry.
2. CNC machine tool machining efficiency improvement technology analysis
2.1Adoption of efficient CNC machining technology
The emergence of digital technology has promoted the development of CNC machining technology innovation, prompting the emergence of a variety of efficient CNC machining technologies.
In the workpiece cutting process, you can use high-speed cutting CNC machine tools, feed and cutting speed can reach 5 to 10 times the ordinary machine tools, the line speed of 400m/min or more, the spindle speed of 10,000r/min or more, you can cut the efficiency of 3 to 5 times.
Increasing the cutting speed reduces the cutting force by 30%, prevents the deformation of parts, and simultaneously takes away the cutting heat through high-speed chip discharge, which avoids thermal deformation of parts and improves machining accuracy.
When applying high-speed cutting machine tools, manufacturers should use supporting tool systems to ensure reliable clamping of the tool and workpiece. They must also monitor spindle speed and tool wear in real time to prevent safety accidents caused by parts and tools splashing. In machining, combined with the structural characteristics of the product, economic, and other requirements, choosing the appropriate CNC machining technology can improve product processing efficiency.
For example, for simple structures but high machining accuracy requirements of the parts, you can use multi-axis machining technology, the use of multi-axis machine tools, hybrid tools, and other simultaneous machining of different parts of the parts, through the merger of processes and shorten the time to change the tool to improve machining efficiency.
For complex parts, such as those with column surfaces, rotary surfaces, and other characteristic curved surfaces, manufacturers can use a CNC milling machine to process the parts. Introducing curved surface CNC high-speed milling processing technology improves machining efficiency.
Under the support of CAD/CAM and other technologies, the use of CNC milling technology needs to establish an automatic tool exchange system, with a tool changer robot, tool recognition device, and other institutions, through the tube heat shrinkable collet to achieve efficient connection of the tool, to be able to obtain a better concentricity, clamping force, and to reduce the centrifugal force, to improve the efficiency of CNC machining.
2.2Improve the CNC machining process
In the improvement of the CNC machine tool machining process, you can start from the perspective of optimizing the tool route, by looking for the shortest machining route to reduce the cutting stroke, as far as possible, through a tool to complete the part contour.
When optimizing the tool route, manufacturers should minimize the rate of empty tools, shorten the tool positioning time, and ensure that the roughness of the machined workpiece contour meets the specified requirements while improving workpiece machining efficiency.
When planning the tool route for internal cavity processing using the line-cutting method, the goal should be to remove the internal space allowance. Considering that residual height often appears between the line’s starting point and endpoint, switch the tool along the circumferential direction when initially using the line-cutting method.
In the fixed-width cut method for machining, the tool cutting force is constant. Tool path optimization should reduce the width of cut and increase the depth of cut to make full use of the side edges, thus improving the cutting capacity.
Improving CNC machining methods allows for centralized machining of the parts’ surfaces with a single clamping. This approach merges and reduces the machining processes, shortens the auxiliary time, and enhances machining efficiency.
When optimizing the workpiece clamping method, according to the size and shape of the workpiece, a reasonable choice of mechanical clamping, hydraulic clamping pneumatic clamping, and other different ways. For example, hydraulic clamping stabilizes the clamping force for large workpieces, preventing vibration and displacement during machining.
For complex-shaped workpieces, design the clamping system to ensure it evenly distributes the clamping force across the workpiece surface, maintaining machining stability.To this end, you can use quick-change fixtures to achieve parts clamping, use specially designed outer or inner diameter stops in the diameter direction to control the parts stringing and shorten the parts to find the right time.
Such as the use of a zero-point positioning ball self-locking mounting system, the use of universal chassis and machine tool disc link can take the pneumatic way to realize the positioning of different parts and fixtures connected to the machine tool to reduce the machine tool stopping time through the rapid dismounting fixtures, and effectively improve the efficiency of machining.
2.3Updating the programming technology of CNC machine tools
The level of personnel programming directly affects the machining efficiency when using CNC machine tools for machining. To improve the efficiency of CNC machining, you can introduce new programming technology to promote the benign development of the CNC system.
Such as the use of CAD, CAM, and other functions as one of the CAXA manufacturing engineers, you can use macro programming technology to achieve integrated programming of parts and components production, according to the different processing needs of parts and components to develop new machining procedures.
In the CNC programming stage, macro programming starts with machining planning to create a design model that combines solids and surfaces and can use multiple algorithms to cope with complex parts and generate efficient and reliable machining programs.
The actual preparation of the CNC program, through the use of continuous processing of the tool path, reducing the tool lift and other actions, and according to the shape of the workpiece reasonable selection of cutting methods, the use of multi-axis linkage and other functions to complete complex operations, then can improve the processing efficiency.
The use of macro programming technology can further enhance the ability of CNC machine tools to sense, analyze, etc. By monitoring data such as the amount of deformation of the machine tool product to establish a compensation processing program, and develop a special analysis program to analyze abnormal processing values, it is possible to complete numerical analysis and determine the machining action according to the preset categories.
For example, preparing an automatic machine tool state detection program allows the operator to simulate the guideway before executing the new CNC program. This step helps check the program’s correctness and promptly identify issues, such as changes in the coordinate system. The operator ensures the dimensional accuracy of the parts by automatically adjusting the processing coordinate system and completes the adjustment of the coordinate system values to maintain processing continuity through the debugging program.
Therefore, through reasonable programming, so that the CNC machine tool according to the amount of machining deviation automatically adjusts the machining parameters, improve the overall process adaptability of the machine tool at the same time, you can enhance the efficiency of machining.
2.4Optimize the application of machine tool selection
In the process of CNC machine tool machining, the effect of tool use directly affects the processing efficiency, therefore, the reasonable selection and application of tools can achieve the purpose of improving machining efficiency.
2.5Integration of modern information technology
In machining, promoting the development of CNC machine tools in the direction of automation and intelligence can integrate various modern information technologies, such as big data and the Internet, to comprehensively improve the efficiency of machinery manufacturing.
In the machining technology upgrade, first of all, you can use the automatic clamping and tool change system to shorten the tool replacement time, prevent errors in tool clamping operations, and enhance the continuity of machining. With the use of the tool library management system, you can realize the intelligent management of the tool, reasonable setting of the tool cutting volume, and other parameters, so that the tool to achieve a better cutting effect.
3 Conclusion
Technological innovation and upgrading in the CNC machining industry will drive the development trend. This will effectively improve production efficiency, create more benefits, and promote the industry’s high-quality transformation.
In the practice of CNC machine tool machining, should accelerate the promotion and application of CNC technology such as high-efficiency cutting, and improve the machining process from the perspective of tool path planning, take reasonable programming and the use of new tools and other means to maintain the efficient operation of the machine tool, and ultimately through the comprehensive use of big data and other technologies to optimize the overall production efficiency of machining, to promote the enhancement of the level of production technology in the manufacturing industry.