Steel powder is a high-volume product extensively used in powder metallurgy. We use it not only in iron-based products but also widely in welding rods, soft magnetism, the chemical industry, metallurgy, food, and environmental protection. In recent years, major industrial countries worldwide have significantly focused on their research and development, continuously improving both production scale and technology.
1 Development of the foreign steel powder industry
In 2017, North American iron powder sales were 429,000 short tons, an increase of about 2% year-on-year. Among them, 394,000 short tons were used for powder metallurgy parts, and the rest were used for non-metallurgical purposes such as welding. However, these non-metallurgical applications are gradually decreasing (see Figure 1).
Figure 1: North American iron ore sales and applications from 2006 to 2017
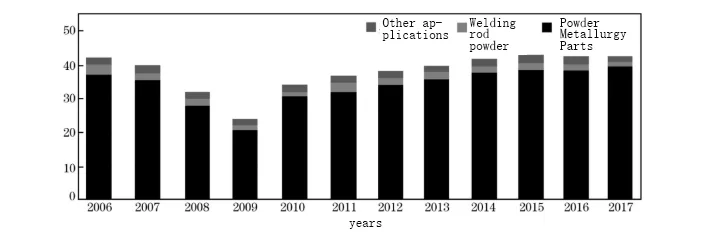
1.2 Development of the European Steel Powder Industry
Europe’s powder metallurgy industry is highly advanced, second only to North America, and it maintains a robust management system. In recent years, powder production and sales have grown steadily, allowing the industry to gradually overcome the financial crisis’s impact. To promote industry development, the European Powder Metallurgy Association actively provides education and training, presents awards, and fosters international cooperation. In 2015, the industry transported a total of 190,000 tons of metal powder, and iron-based parts constituted 81% of that volume (see Figures 2 and 3).
Figure 2 Metal powder shipments in Europe, 2004-2017
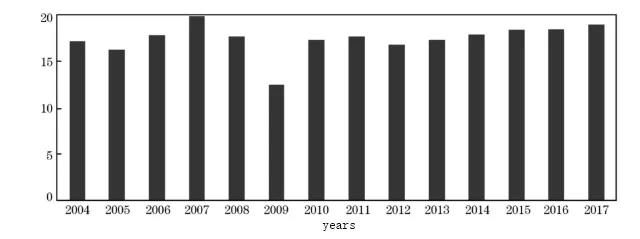
Figure 3: Distribution of metal powder applications in Europe
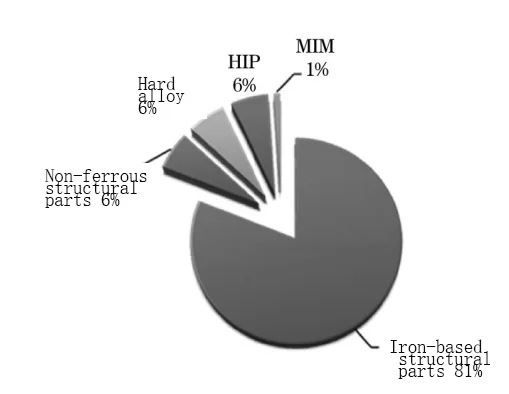
1.3 Development of Steel Powder Industry in Japan and Other Asian Countries/Regions
Japan’s powder metallurgy industry leads Asia. It offers advantages in market development, production management, quality, and alloy technology, particularly excelling in manufacturing lightweight and complex parts. In 2017, Japan produced and sold 102,000 tons of metal powder. South Korea produced about 70,000 tons, India 40,000 tons, and Taiwan over 30,000 tons. Other Asian regions produced less than 20,000 tons (see Figure 4).
Figure 4 Production and sales volume of metal powder in Japan from 2004 to 2017
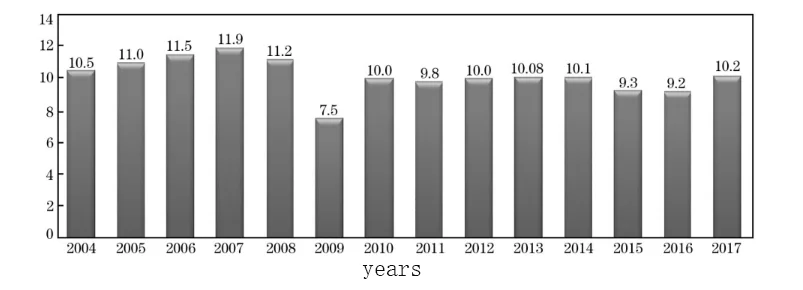
2 Development of China’s steel powder industry
China’s in-depth research into powder metallurgy materials has significantly expanded steel powder’s application scope across the country. The rapid development of the automobile industry has particularly driven this, leading to considerable progress in sales volume, variety, and quality.
In 2017, China sold 552,900 tons of steel powder, marking a 14.2% increase from the previous year. Auto parts primarily drove this growth. Additionally, both import and export volumes saw significant increases, as the table illustrates.
Table 1 Statistics on China’s steel powder production from 2005 to 2017
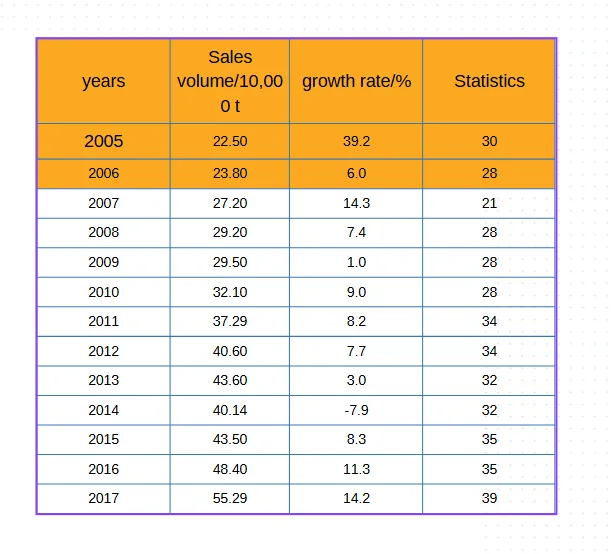
Table 2 Sales volume of different types of steel powder in China from 2006 to 2017
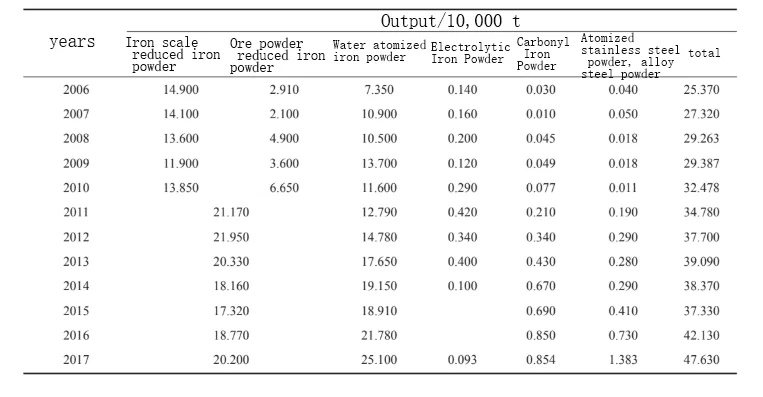
3 China’s steel powder market and technology development trends
3.1 Development Status of the Powder Metallurgy Products Industry
The China General Machinery Parts Industry Association reported that in 2017, the powder metallurgy parts industry saw its sales revenue increase by 11.4% and its sales volume by 8.8%. Within this sector, automobile parts experienced a decrease, while home appliance parts recorded a slight increase, and motorcycle parts a minor decrease. Despite these individual changes, these three categories still held the majority of the market share, as Figure 7 illustrates.
3.2 Development Trend of Steel Powder Market
Recently, as the country has stepped up its environmental protection efforts, this has affected some companies that produce reducing powder and atomized powder. Larger, more standardized companies are generally managing better. However, it has hit smaller, less standardized companies harder, causing a sharp drop in their production capacity for medium and low-level reducing powders.
The country’s requirements for safety and environmental protection continue to increase and have become normalized. The improvement of safety and environmental protection standards will inevitably lead to an increase in industry entry barriers and the exit of some small companies from the market: the increase in safety and environmental protection investment will lead to an increase in corporate production costs.
3.3 Technological development trends of steel powder products
In recent years, the price of atomized iron powder has dropped sharply, causing reduced iron powder to reach a low point. It simply lost its cost advantage. However, its unique particle morphology gives it excellent forming properties, so it remains suitable for friction materials, low-density specialized parts, and high-performance oil-containing bearings.
3.4 Development Trends of Steel Powder Process Technology and Equipment
Coal gas or natural gas tunnel kilns, measuring about 170 meters long, have become the primary equipment for producing reduced iron powder. A single kiln can achieve an annual output of 20,000 tons, nearing international advanced levels. This type of kiln has significantly improved its automation, intelligence, production efficiency, and product quality. For the future, the industry aims to replace coal gas with natural gas and adopt automated tunnel kilns longer than 200 meters.
4 Conclusion
China’s steel powder industry needs to prioritize improving powders’ comprehensive performance and quality stability. This includes developing low bulk density, high-performance reduced iron powder, and high-purity, high-compressibility water-atomized pure iron powder. At the same time, the industry must enhance its pre-alloyed steel powder system, expand into special powders, and shift from price competition to competition based on variety, quality, and service. This will enable it to transform from a material supplier to a material service provider.