1. Introduction
Injection molding depends heavily on injection molds. These molds play a vital role in the molding industry. They determine the final quality of molded products. By using them, manufacturers can achieve high precision, consistency, efficiency, and low material loss. These features help ensure structural integrity and dimensional accuracy.
However, many molds have complex shapes and easily worn surfaces. Using only traditional materials and hardening methods cannot meet the increasing demands for longer mold life and better performance.
Today, many manufacturers apply laser surface treatment technology to plastic mold production. This technology increases surface hardness and reduces deformation. It also improves wear and scratch resistance. As a result, laser-treated molds often last several times longer than those treated with traditional quenching.
Laser treatment does not require cooling media. It offers a cost-effective and environmentally friendly way to improve mold durability.
2. Exploration of Laser Surface Treatment for Injection Molds
2.1 Mechanism of Laser Surface Treatment
(1) Working Principles of Laser Technology
Laser surface treatment includes several methods. These include phase transformation hardening, laser cladding, alloying, remelting, and shock hardening. This paper focuses on phase transformation hardening. In this method, the laser quickly heats the surface and lets it cool by itself. This rapid heating and cooling cause a martensitic transformation. This change increases the surface hardness.
Engineers use various types of laser equipment. These include CO₂ lasers, semiconductor lasers, and YAG lasers. Each type suits different part sizes and applications. To choose the right laser, users must consider power, beam diameter, shape, pulse width, and frequency.
YAG lasers use yttrium aluminum garnet crystals. Their performance depends on the ions used, the pumping method, and the system design. These lasers send high-energy pulses to the surface. The heat causes quenching, welding, or cutting.
Semiconductor lasers create radiation using semiconductors. They operate through electric injection, optical pumping, or high-energy electron beams.
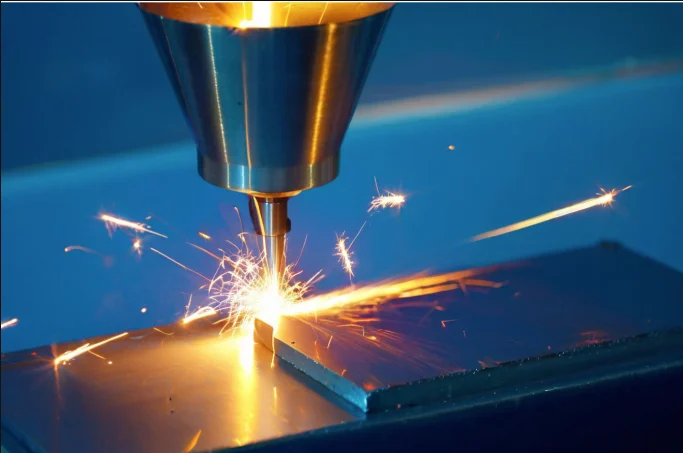
(2) Overview of Laser Surface Technology
Laser surface treatment can turn a regular material surface into a high-performance one. This technology combines low-cost manufacturing with improved functionality. It increases surface hardness by around 15%. It causes little deformation and leaves only a small machining allowance. It does not need a cooling medium.
Digital control systems manage the laser energy output. With this control, operators can accurately harden complex shapes or small, difficult areas.
This method improves the performance of low-grade materials. It also lowers mold manufacturing and maintenance costs. As a result, it fits well with modern mold applications.
2.2 Main Failure Modes of Injection Molds
Injection molds include cavities, cores, inserts, and other parts. These components directly shape the final plastic parts. During operation, the mold surface faces repeated high temperatures and pressures. The temperature usually reaches around 200 °C, and the pressure can go up to 140 MPa, depending on the plastic used.
The plastic melt flows at high pressure and causes surface wear. Demolding also increases surface damage. The wear becomes more serious when the plastic contains fillers like silica, glass fiber, or carbon fiber.
The mold surface also experiences frequent temperature changes. These range from 50 °C to 340 °C. These cycles lead to thermal fatigue cracks, stress concentration, and fatigue failure.
Some plastics release corrosive gases, such as HCl and HF, during molding. These gases corrode the mold surface and cause further damage. Common failure types include abrasive wear, fatigue cracks, scratches, deformation, and corrosion. These problems directly affect plastic parts’ appearance, size, and surface quality.
To reduce failure and ensure stable production, engineers must choose suitable mold materials. They should also apply laser surface treatment to improve surface strength.
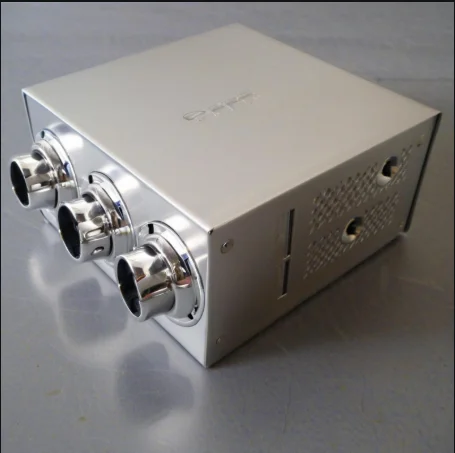
2.3 Case Studies of Laser Treatment in Mold Applications
P20 Steel
P20 is a pre-hardened plastic mold steel. Its factory hardness ranges from 30 to 42 HRC. It is easy to cut and polish, and many manufacturers use it for automotive mold cavities.
Wang Jianjun and his team used laser quenching after normalizing the material. Their results showed that the treatment formed needle- and lath-shaped martensite. The hardness increased from 245 HV to 520 HV. The hard layer reached a depth of about 0.93 mm. Increasing the laser power made the martensite coarser. However, it also strengthened the material and improved its wear resistance.
718 Steel
718 steel is similar to 3Cr2NiMo in China. It has a hardness of 41–47 HRC and polishes well. It also supports EDM machining. Flame hardening can raise its hardness to 52 HRC. Mold manufacturers often use it for injection molds without additional heat treatment.
In one example, a company used 718 steel to make a brake handle mold. They molded over 320,000 parts using glass fiber-reinforced PC. The mold surface became heavily worn and lost its finish. This affected the quality of the later plating process.
Wang Zhenhua applied a YAG laser to the mold surface. He found that a scanning speed of 6.5 mm/s gave the best wear resistance.
45 Steel
45 steel is a low-cost, widely used carbon steel. It performs well and is suitable for mold frames and low-load cavities. Laser quenching significantly improved its performance. The hardness reached up to 1050.3 HK, about three times higher than untreated steel. The hardened layer formed a layered martensite structure. This structure provided clear strengthening and better corrosion resistance.
3 Conclusion
Laser surface quenching is now a proven method in injection mold applications. It solves many problems such as thermal fatigue, surface scratches, deformation, and corrosion. It helps extend mold life, lower production costs, and increase efficiency.
As laser and control technologies continue to improve, the precision and stability of laser processing equipment will rise. At the same time, equipment costs will fall. These changes will make laser surface treatment even more important in future mold manufacturing.