Because stainless steel has unique strength, high abrasion resistance, superior corrosion and rust resistance, and other excellent characteristics, it gives people a “rust-free, clean, hygienic and high-grade” good impression. It is widely used in the chemical industry, food machinery, environmental protection, household appliances, tableware, and other industries.
According to the different characteristics of the products and customer groups, the aesthetic concept and the surface treatment of stainless steel products are different.
Different patterns and surface treatment effects can give a person the feeling of roughness or delicate and present the stainless steel three-dimensional sense of metal to elaborate the product’s deep cultural connotation and get more and more users of the favor.
Choosing a suitable surface treatment for the enterprise’s own stainless steel products is a relatively important research topic; the following introduces several common surface treatments.
1.Mechanical surface treatment
1.1 Polishing
For stainless steel sheet metal parts of one or both sides of the grinding, the formation of the surface of the non-directional texture, reflective (that is, presenting snowflake pattern or short filament) of the 4 surface.
For flat polishing, generally use a flatbed sander; through the sanding belt high-speed sanding, the surface presents a snowflake pattern texture. As shown in Figure 1, a flatbed sander includes a drawing machine, a laminating machine, and three sections of the roller table, a stainless steel plate relying on the positioning wheel of the feeding roller table, feeding into the sander as the sander for the whole belt drawing, including the entire large plane, not only high efficiency and polishing consistency, straightness is also perfect.
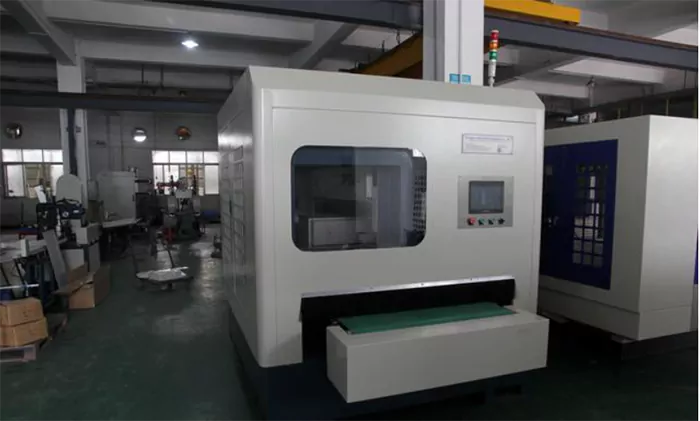
Fig. 1 Flatbed sander
For welded-formed stainless steel products can be polished in the triangle drawing machine (see Figure 2). In the triangle drawing machine, according to the dimensions of the workpiece, the production of jigs and fixtures can be processed on irregular surfaces, suitable for molding after the box, and the products of the surface of the polishing process can also be used handheld polishing machine, by adjusting the speed of the polishing machine, to get a different polishing texture.
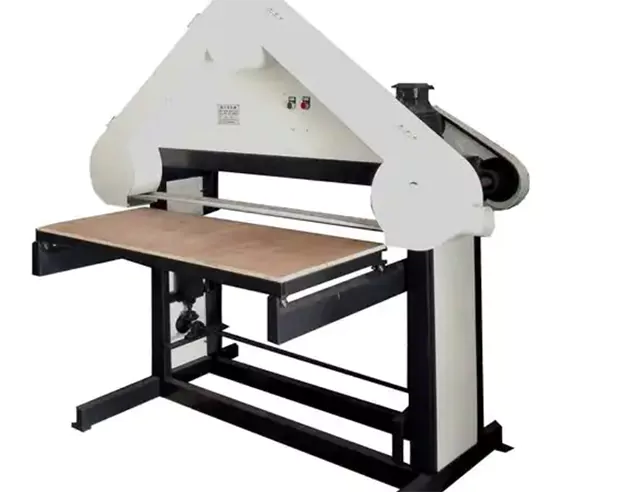
Fig. 2 Triangular Wire Drawing Machine
1.2 Drawing
The use of appropriate particle size of the abrasive material, the polished stainless steel sheet metal parts on one side or both sides of the 4 # surface for chipping, so that the surface shows continuity of the line pattern, the formation of HL-surface, referred to as wire drawing.
The effect produced is different in the drawing process, using different particle sizes. The coarser the grain size, the stronger the sense of metal; the finer the grain size, the more delicate the product. In a business setting, a reference sample can typically be created.
We need to use a flat sanding machine for flat wire drawing to realize low-speed belt sanding. The stainless steel surface shows a continuity line pattern to achieve the grain requirements.
For welded stainless steel products, use the triangle wire drawing machine, replace the abrasive belt with a nylon belt, and apply uniform pressure through the graphite press or the press on the wire drawing machine to obtain a consistent drawing texture.
The use of handheld wire drawing machines is difficult to ensure the direction of the texture and color consistency due to the artificial strength of different, different back-and-forth speeds. In the pursuit of stainless steel products of higher grades, handheld wire drawing machines will be triangle wire drawing machines or special wire drawing machines instead.
The outer surface of stainless steel products with brushed wire should be flat, with no scratches or obvious traces of wire mending, a clear and uniform texture, consistent color, and fine geometric modification. Fig. 3 shows the appearance of the KDF4 filter rod molding machine, and Fig. 4 shows the appearance of the upper part of the KDF filter rod molding machine.
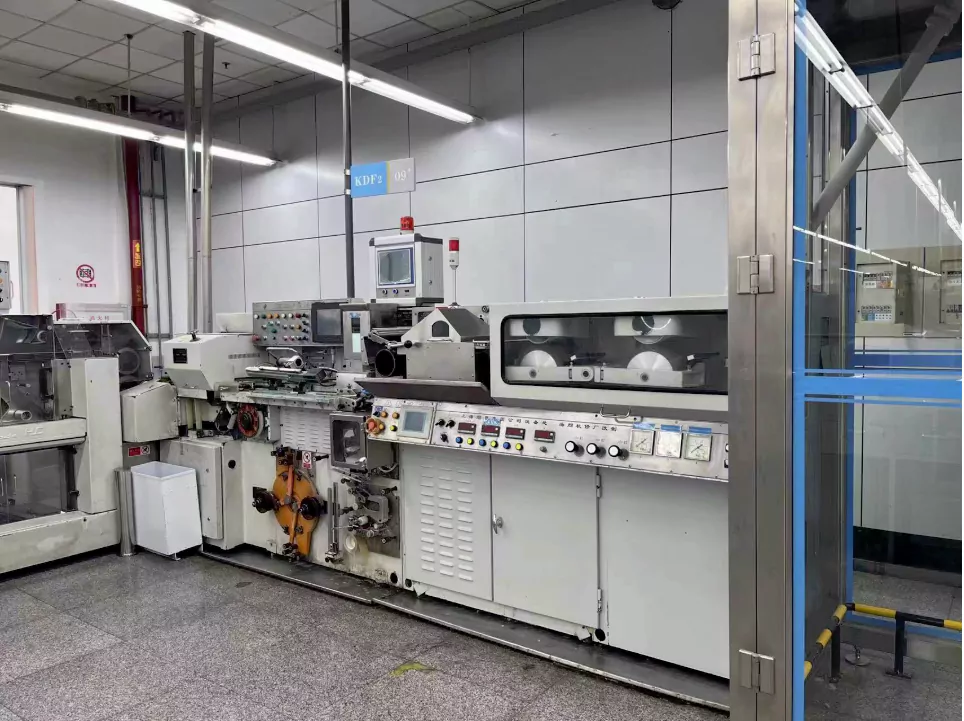
Fig. 3 Appearance of KDF4 Filter Rod Forming Machine
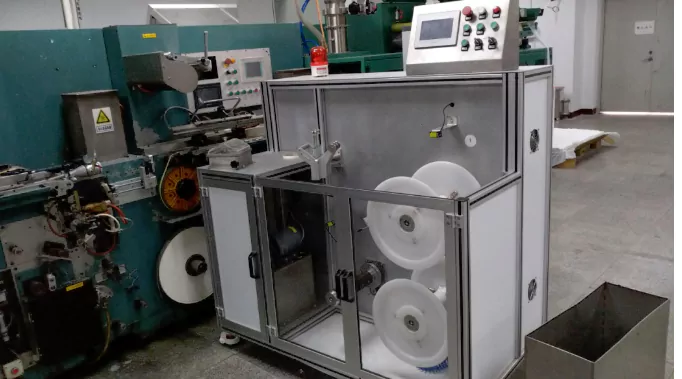
Fig. 4 Appearance of parts on KDF filter rod molding machine
1.3 Mirror finish
Mirror surface treatment involves gradually refined abrasive polishing and extremely fine ferroan rubbing, which rubs a lot into the surface of the non-directional texture, high reflectivity, and image clarity without leaving any traces of abrasion. Mirror-finish stainless steel plates are commonly used in molded products and high-quality decorative panels.
The simple shape of the parts can be purchased through the market mirror plate direct processing; for the complex shape of the parts, assembly welding, the surface will be polished into a mirror, but artificial polishing time is too long, and the efficiency is also very low.
For artificial polishing mirror parts, you can use the high-speed angular polishing machine in 2B stainless steel plate or polished plate material; the first use of coarse-grained polishing disc polishing, the surface has reached the degree of research and grinding, the use of wool wheels, with the corresponding polishing wax for mirror polishing, the completion of the use of microfiber wipes, stainless steel cleaner powder, to remove the polishing wax and other spoils.
1.4 Glass bead blasting
Spray glass beads is the use of specialized sandblasting equipment; with the help of compressed air pressure, glass beads high-speed spray to the surface of the parts, the use of glass beads on the surface of parts produced by the solid scouring effect, eliminating the stainless steel products’ surface burrs, weld slag, and dirt and other debris, so that the surface to achieve the effect of matting or surface snapping.
Usually, the glass bead spraying process is applied as a pre-treatment to a surface. If the spray treatment is used as the final treatment, the spray treatment surface should be avoided in the machine operating range or visual range. The effect of glass bead spraying on a part is shown in Figure 5.
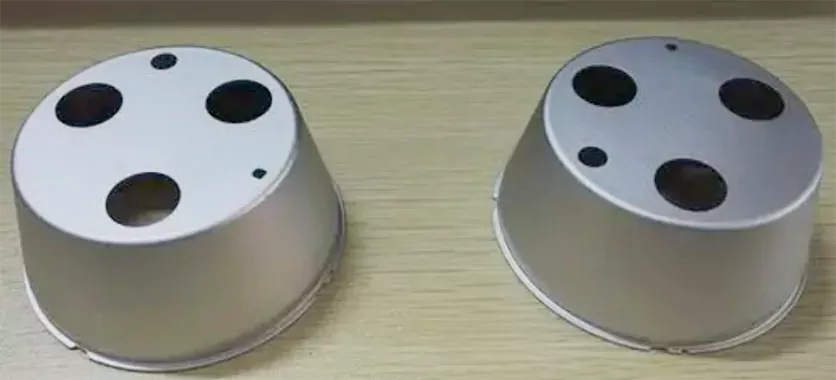
Fig. 5 Effect of parts sprayed with glass beads
Surface anti-fingerprint treatment
Even if stainless steel products’ surfaces are stunning, dust and oil can easily attach, especially in transit and assembly processes. Various forms of finger touch will leave traces, affecting the appearance of stainless steel products’ quality; therefore, the pre-treatment of stainless steel products should be fingerprint-proof. For anti-fingerprint treatment, use anti-fingerprint paint, passivation, electrolytic polishing, and other processes.
2.1 Anti-fingerprint paint
Use anti-fingerprint paint to improve the anti-fingerprint contamination ability of stainless steel products. This process is widely used in the elevator industry and home appliance industry.
1)In the elevator industry, the general use of assembly line processing, the process flow is: the use of automatic sanding machine polishing or drawing → cleaning a brush with anti-fingerprint paint → baking → strong cold → film packaging.
2)In the tobacco machinery industry, the process of using anti-fingerprint paint flows as follows: a. Cleaning: a degreasing agent is used to remove the surface to ensure that it does not have any impurities; b. Spraying anti-fingerprint paint: the ratio of paint and thinner is 1: (1.5 ~ 3); the thickness of the film is 10 ~ 20 μm; c. Baking: 150 ~ 180 ° C, the time is 12 ~ 15 min.
During the whole process, there can’t be any dust in the construction environment because after the cleaned surface parts meet the dust, the dust will adhere to the inside of the coating, which easily causes the coating to be uneven and not smooth.
Anti-fingerprint paint, after coating, requires good transparency, high gloss, good adhesion, high hardness paint smoothness, hand sweat resistance, anti-scribbling, and easy cleaning.
2.2 Passivation
After welding or necessary subsequent heat treatment, should be pickled, grinding, brushed or spraying treatment; complete removal of oxide skin and metal temper color stainless steel pure metal surface can achieve its optimized corrosion resistance for complex parts, one of the most commonly used at the same time can also be used for the most complex parts to remove the oxide skin is the method of pickling passivation in the acid mixture.
If the area to be pickled on the part is small or the part is very bulky, pickling paste can be used for pickling passivation. Stainless steel products pickling passivation parts shown in Figure 6.
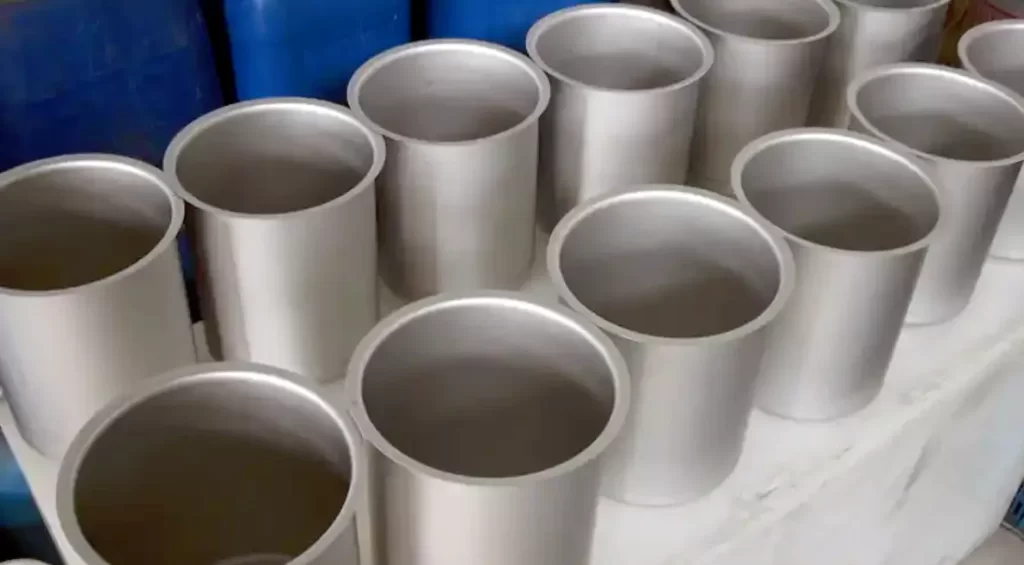
Figure 6 Stainless steel products pickling passivation parts
The effective degree of pickling is affected by the following factors.
1)The composition of steel, organizational structure, and workpiece shape for ferritic stainless steel and pickling should be strictly controlled parameters. Because ferritic stainless steel’s corrosion resistance is poor, excessive pickling and damage to the product’s surface are easy to cause. Due to good corrosion resistance, the operation range is larger for austenitic stainless steel and ferritic stainless steel.
2)Acid composition, temperature, and aging of the pickling tank. During the pickling process, the temperature of the pickling tank is between 20 and 90°C.
The temperature of the pickling tank is between 20 and 90°C. Constant agitation of the acid and higher temperatures may cause the acid’s evaporation, reducing the pickling process’s effectiveness and possibly causing serious injury to the operator.
For the acid solution, the composition of the pickling solution should be regularly checked, and timely additions of new acid solution should enhance its effectiveness.
2.3 Electrolytic polishing
At present, high-grade equipment and stainless steel products surface are electrolytic polishing processes, such as a new generation of high-speed, ultra-high-speed tobacco machinery and equipment using stainless steel products, the appearance of the quality of the very beautiful, smooth surface, showing silver-white.
The electrolytic polishing process is used in many tableware, medical equipment, home appliances, and other industries to deal with stainless steel high-grade products, which is a better choice. The appearance of the stainless steel products of the coiling unit is shown in Figure 7.
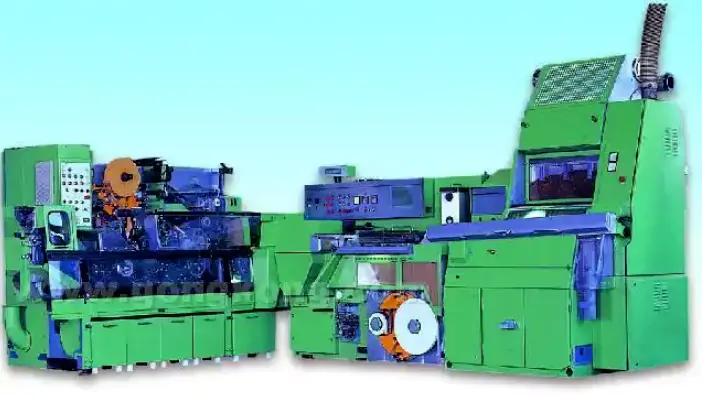
Fig. 7 Appearance of stainless steel products of coil jointing unit
Electrolytic polishing, also known as electrochemical polishing, is to be thrown workpiece for the anode, insoluble metal for the cathode, the two poles at the same time immersed in an electrolytic tank through the direct current and selective anodic dissolution phenomenon, so that the anode on the microscopic part of the priority of the dissolution of the protruding to form a bright, smooth surface of the method.
On many occasions, electrolytic polishing can be used to replace complicated mechanical polishing, especially the shape of the more complex and difficult-to-process parts with mechanical polishing. The electrolytic polishing device diagram is shown in Figure 8, and the electrolytic polishing principle diagram is shown in Figure 9.
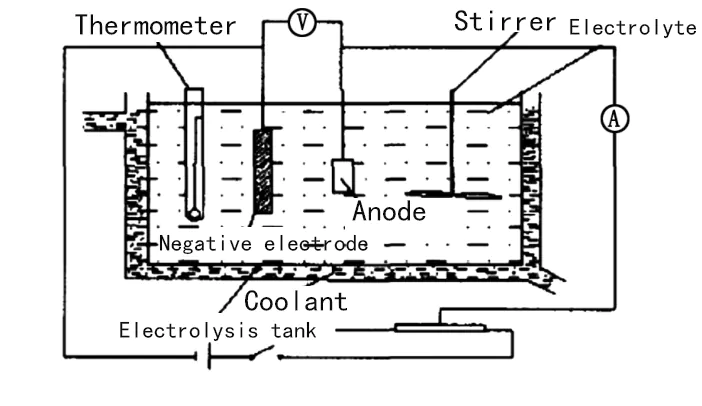
Fig. 8 Electrolytic polishing device diagram
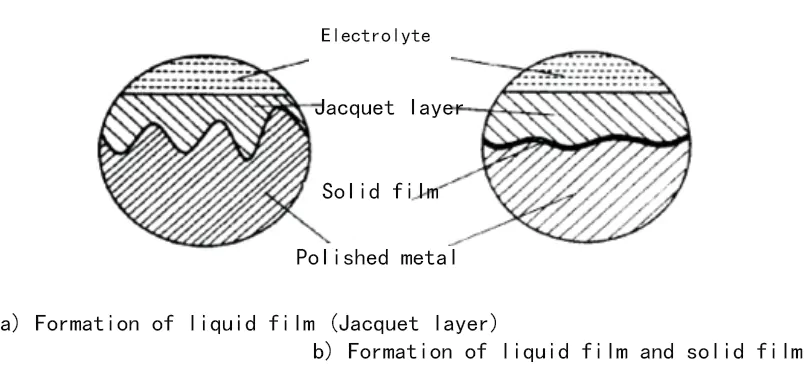
Figure 9 Schematic diagram of electrolytic polishing
Electrolytic Polishing Process: Degreasing Tank→Water Cleaning Tank an Electrolytic Polishing Tank>Water Cleaning Tank→Nitric Acid Tank→Water Cleaning Tank→Neutralization Tank→Pure Water Tank→Pure Water Tank→Anti-fingerprinting Treatment→Drying.
Conclusion
Different treatment methods present different surface effects. Enterprises should be based on the characteristics of the product, make a reasonable choice of stainless steel treatment methods, improve the grade of stainless steel products, thus reflecting the cultural connotation of the product, and maximize the trust of customers.