Choosing the right tools for CNC machining is crucial for achieving high-quality products. Here are some factors to consider when selecting tools for CNC machining:
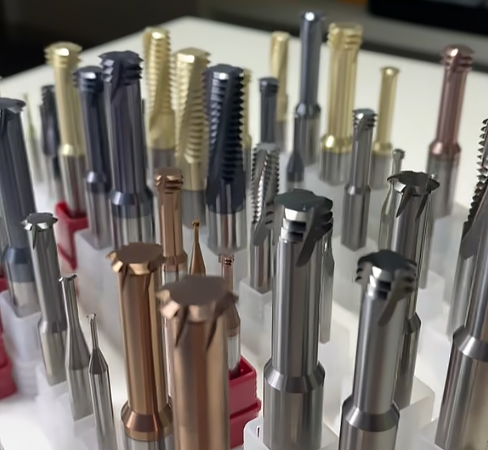
- Material Compatibility: Choose cutting tools that are specifically designed for the material you are machining. Different materials (such as aluminum, steel, plastics, etc.) require different tool geometries, coatings, and cutting parameters for optimal performance.
- Tool Material: Select cutting tools made from high-quality materials such as carbide, high-speed steel (HSS), or ceramic, depending on the material being machined and the desired cutting speed and tool life.
- Tool Geometry: Consider the tool geometry, including flute design, rake angle, helix angle, and cutting-edge preparation. Each of these factors affects chip formation, cutting forces, surface finish, and tool life.
- Coating: Choose cutting tools with appropriate coatings such as TiN (Titanium Nitride), TiCN (Titanium Carbonitride), TiAlN (Titanium Aluminum Nitride), or DLC (Diamond-Like Carbon) coatings. Coatings can improve tool life, reduce friction and built-up edge, and enhance surface finish.
- Tool Size: Select the appropriate tool size based on the machining operation, part geometry, and available spindle power. Using the correct tool size helps maintain rigidity, minimize deflection, and ensure dimensional accuracy.
- Cutting Speed and Feed Rate: Consider the recommended cutting speeds and feed rates provided by the tool manufacturer based on the material being machined, tool material, and tool geometry. Optimize cutting parameters to balance material removal rate with surface finish and tool life.
- Toolholder and Collet: Use high-quality tool holders and collets that provide secure clamping and accurate tool runout. Proper tool holder selection can minimize tool vibration and improve machining accuracy.
- Tool Life and Cost: Balance tool life with tool cost to achieve the most economical solution. Consider the total cost of ownership, including initial tool cost, tool life, and productivity gains.
- Coolant Requirements: Determine if the machining operation requires coolant or lubrication and select tools that are compatible with the coolant type and application method.
- Tool Manufacturer Reputation: Choose cutting tools from reputable manufacturers known for their quality, consistency, and innovation. Look for manufacturers that provide comprehensive technical support, application assistance, and tool reconditioning services.
- Application Considerations: Consider the specific requirements of the machining operation, such as roughing, finishing, profiling, drilling, or threading, and choose tools optimized for each application.
- Tool Performance Monitoring: Implement tool wear monitoring systems or use predictive maintenance techniques to monitor tool performance and replace tools before they reach the end of their useful life.
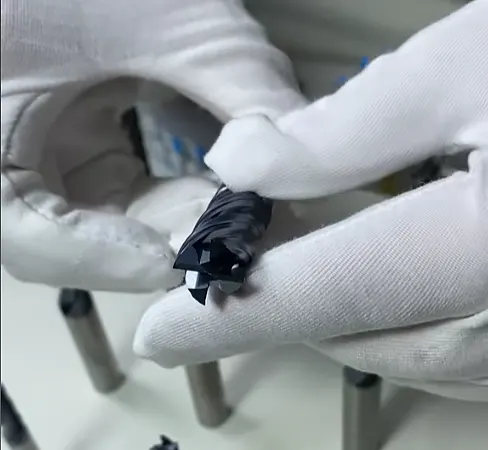
By carefully considering these factors and selecting the right tools for your CNC machining application, you can improve machining efficiency, quality, and overall productivity.