The global economy and technology are developing rapidly. As a result, industries like aerospace and automotive are gradually attracting more attention. A key component driving their progress is the tool magazine system, which plays a crucial role in enhancing manufacturing efficiency and precision.
As a leading manufacturing power, China’s manufacturing industry will become one of its pillar industries.
CNC machining centers play a crucial role in mechanical production. The automatic tool changer is an important part of CNC machining centers. It offers continuous tool changes and reduces tool change time.
The automatic tool changer improves productivity and reduces production costs. It cuts non-cutting time, boosting the productivity of both the machine tool and the entire production line.
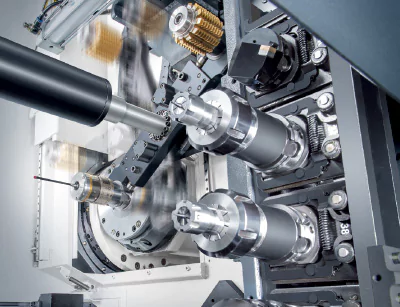
In the future, developers will focus on improving CNC machine tools. They will aim for high performance, high precision, and high reliability. These improvements will enhance the precision, operating speed, and reliability of automatic tool changers.
Currently, developed countries have successfully created five-axis and six-axis linkage machine tools. These machines significantly improve processing efficiency and precision.
China is also pushing forward the development of its equipment manufacturing industry. The country has set a strategic goal for the independent development of CNC machine tools. This goal aims to shorten the R&D cycle and raise the technical level.
At the same time, Chinese scholars are focusing on the performance of CNC machine tools and their components. They have formed independent R&D teams to create high-performance CNC machine tools with independent intellectual property rights.
However, domestic auxiliary manufacturing components still face challenges. Automatic tool changers, automatic inspection devices, and computerized control systems often suffer from low precision, inaccurate performance, and unreliable operation. These issues need urgent resolution.
Overview of tool changer system
A tool magazine system is an automated machining device responsible for storing and changing tools. This system includes a tool magazine that stores multiple tools and an automatic tool changer. The tool magazine prepares the required tools before machining. It also provides storage space for unused tools.
1. Working Principle
The computer program controls the operation of the tool magazine. When the system receives the tool change command, it starts the drive device. Then, it runs the tool magazine.
During this process, the position detection device sends the tool’s position to the computer.
When the tool reaches the specified position for the tool change, the computer receives the stop signal. The tool change device then works with the robot to complete the tool change operation.
After the tool change is completed, the drive device continues to work, and the tool magazine to the standby state.
2. The relationship between the tool magazine and the tool change mechanism
An important part of the tool magazine system is the tool changer. It is responsible for replacing tools. Tool magazines and tool changers complement each other. Both are indispensable.
Without a tool magazine, tool change time increases. This results in longer non-cutting time. Without a tool changer, the tool cannot reach the tool change position. Productivity cannot improve.
4. Influence of tool magazine system
In recent years, people have gradually realized the importance of the tool magazine system in the machining process.
Its impact on machining efficiency is becoming more obvious. It is no longer seen as an auxiliary part of the machine tool. Instead, it is playing a larger role in the field of technology.
Currently, the global development direction of CNC machine tools focuses on high performance, high precision, and high reliability. The quality of the tool magazine system directly affects the overall performance of CNC machine tools.
Types of tool magazines
According to different designs and functions, tool magazines can usually be categorized into the following main types.
1. Bucket type tool changer
- Characteristics: This small tool magazine usually holds up to 24 tools and is compact.
- Principle of operation: During tool change, the tool magazine moves toward the spindle. When the tool on the spindle enters the tool slot in the magazine, the spindle relaxes the clamping device and moves upward, leaving the tool in the magazine.
- After the tool magazine rotates to the correct position, the spindle moves downward to clamp the new tool and complete the tool change.
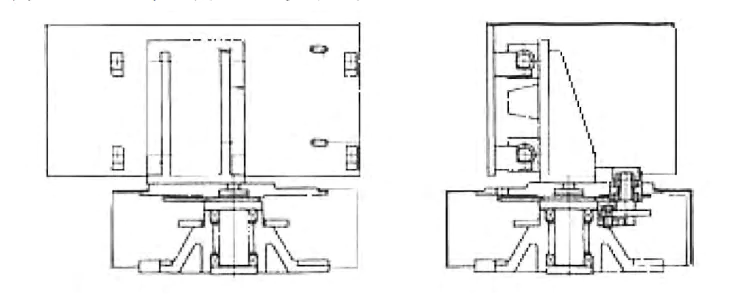
Figure 1 Bucket hat type tool magazine
2. Disc type tool magazine
- Characteristics: Also known as disk-type tool magazine, usually used in small vertical integrated processing machines, with a tool capacity of about 30.
- Principle of operation: the general diameter of the tool magazine is 1 meter, the tool magazine rotation will be selected to move to the tool position, at the same time the spindle also moved to the correct position, the robot clamped the tool in use and the selected tool to complete the tool change.
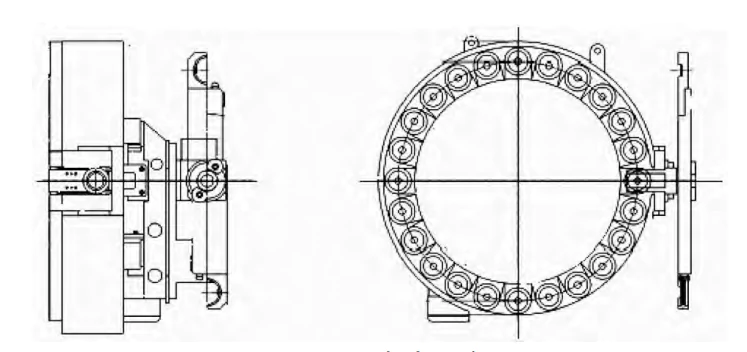
Figure 2 Disc type tool magazine
3. Chain-type tool changer
- Features: This type of tool magazine has a large tool capacity, usually up to 120, suitable for large machining centers.
- Principle of operation: chain tool magazine through the drive device driven sprocket rotation, the chain will be transferred to the correct position of the tool, by the knife device with the robot to complete the tool change action.
- With the robot to complete the tool change action. The drive device is usually a hydraulic or mechanical drive, with high efficiency and flexibility.
4. Side-mounted tool magazine
- Characteristics: The tools are hung vertically or obliquely, which is convenient for quick change and management of tools.
- Application: This type of tool magazine is often used in the need for frequent replacement of tool processing occasions, such as mold processing.
5. Automatic tool magazine
- Features: Integrated with robot technology, it can automatically recognize and change tools.
- Advantages: Increased speed and accuracy of tool change, suitable for complex machining tasks.
Table 1 Types of tool magazines
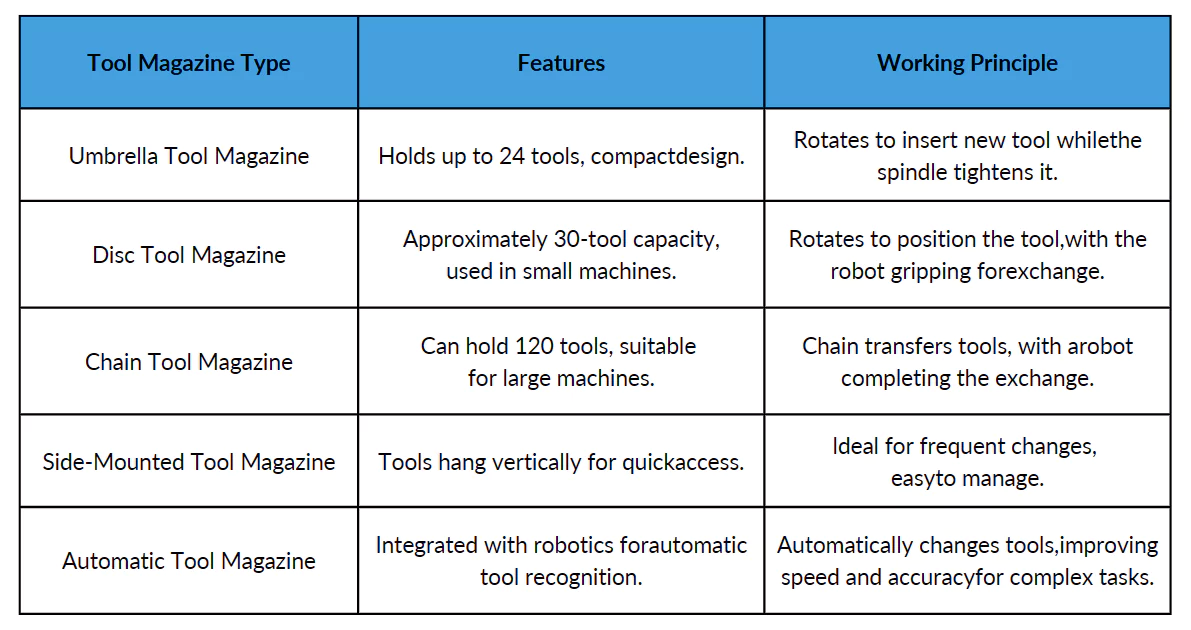
China’s external research status and development direction
1. The origin of the automatic tool changer
Since the 1950s, the United States successfully launched a machining center with an automatic tool changer. Countries have invested in the research and development of their machining centers.
By the 1970s, CNC machine tools entered a golden period of development. A variety of high-performance, high-reliability, and high-transmission-accuracy machining centers emerged.
Germany, Japan, and other developed countries made remarkable achievements in this area. For example, Austria developed a tool change time of only 0.4 seconds for automatic tool change machine tools. This set a world record.
By configuring independent drive motors for each spindle on multi-spindle machines, manufacturers can significantly reduce tool change time.
2. Current status of research and development in China
Compared with these countries, China’s research and development of automatic tool changers started relatively late. Developed countries started their research in the 1950s, while China only started to follow suit 30 years later. Due to the late start, China’s automatic tool changer production technology is still immature, and the performance gap is obvious compared with developed countries.
However, China is increasing its emphasis on the equipment manufacturing industry, clarifying the development direction of CNC machine tools and striving to shorten the research and development cycle.
At the same time, more and more scholars began to pay attention to CNC machine tools and their auxiliary components, set up independent research and development teams, and strive to develop high-performance CNC machine tools with independent intellectual property rights.
3. Composition of automatic tool changer
The automatic tool changer mainly consists of tool magazines, robots, and drive devices. It is usually divided into five types: bucket hat type, disk type, chain type, side hanging type, and automatic tool magazines.
A computer program controls the operation of the tool magazine. The computer sends commands to the drive unit’s motor. The position detection device monitors the tool’s position after startup.
When the tool reaches the specified position, the computer receives a feedback signal. It then instructs the motor to stop. At this point, the robot completes the tool change under control.
4. Current Challenges
Currently, the main problem facing the tool changer system is that the transmission accuracy decreases over time. For example, the cam mechanism may wear out due to prolonged operation, leading to a reduction in transmission accuracy.
In addition, the tool change time is an important indicator for evaluating the performance of the tool magazine, which is strongly influenced by the sensitivity of the knife-flipping device. Currently, tool change times are generally long, which poses a productivity challenge.
5. Types of drives
The knife magazine drive device is mainly divided into a knife turning device, a manipulator drive device, and a knife storage bin drive mechanism. Common drive methods include pneumatic drive, hydraulic drive, and mechanical-hydraulic linkage drive.
Researchers have found that the cam mechanism is excellent in dynamic characteristics and can maintain high transmission accuracy at high speeds, so the automatic tool changer for tool magazines using the cam mechanism is gradually becoming a trend.
However, cams require high machining accuracy and relatively high costs.
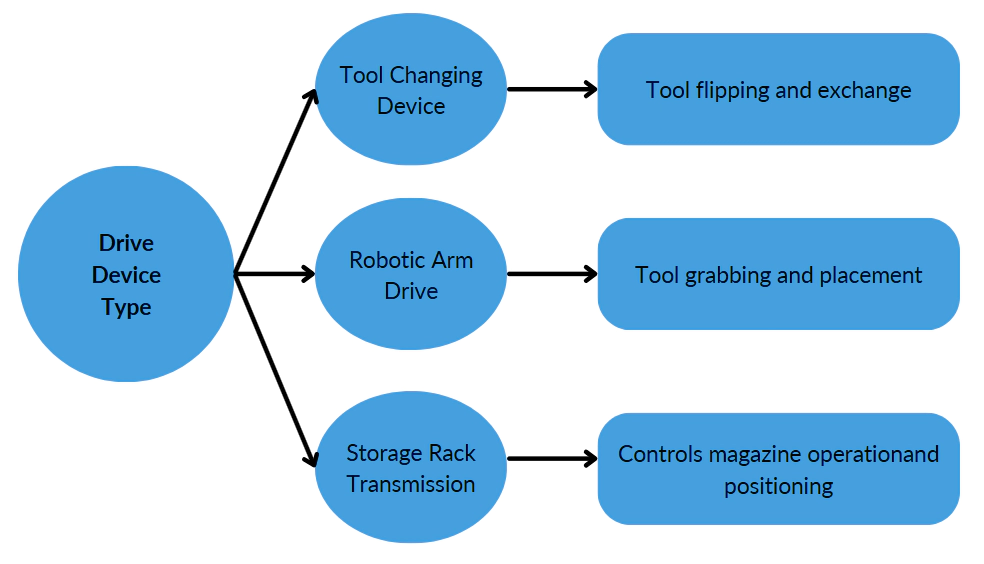
Fig. 3 Types of drives
6. Future development trend
With the continuous progress of CNC technology and automatic control technology, CNC machine tools are developing in the direction of high-speed, high-precision, and multifunctionalization. This will certainly put forward higher requirements for the tool magazine system.
In the future, the tool magazine system needs to be able to store more tools to meet diversified machining needs, and at the same time realize faster tool change speed and more accurate tool change positioning.
Conclusion
In conclusion, the continuous development of the tool magazine system results from the technological progress of CNC machine tools. It also helps enhance the competitiveness of China’s manufacturing industry.
Through continuous technological innovation and research, we believe that China’s future in the field of automatic tool changers will be brighter. China will also have a strong position in the global manufacturing industry.