1 Analysis of CNC Manufacturing Methods for Complex Surfaces
Blower rotor blades and steam turbine blades have complex curved surfaces. These parts need high precision and surface quality. Multi-axis linkage envelope milling improves processing efficiency, surface finish, and accuracy. This method uses annular discs and cyclone cutters to achieve better results.
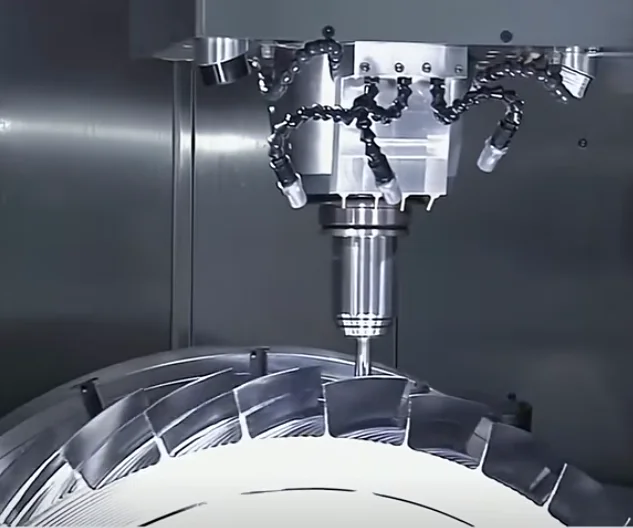
The outer annular disc milling cutter shapes the outer ring. It does this by rotating and moving in an arc. The CNC system controls four auxiliary motions. These motions create a meshing path between the tool and the workpiece. Together, these movements complete the envelope milling process.
The inner cyclone milling cutter forms a spiral surface by rotating its head and blade. This method allows for fast and accurate forming, and it is faster and more efficient than finger milling.
2 Key Considerations in CNC Machining of Complex Surfaces
2.1 Positioning Challenges
It is difficult to position complex workpieces, especially in small batches. Traditional fixtures take a lot of time and cost more. They are also hard to use for high-precision parts. To solve this, manufacturers can measure and position the workpiece directly. This method allows accurate machining even if clamping is not perfect. It reduces cost and time. It also adjusts the machining allowance based on the blank shape. This ensures that the cutting path matches the CAD model.
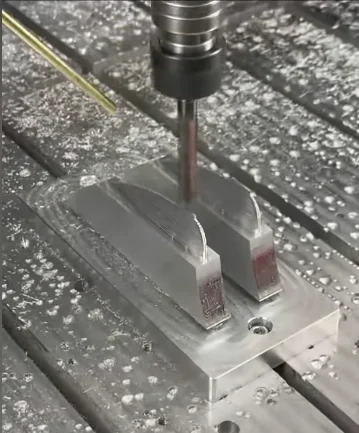
2.2 Rough Machining Techniques and CNC Tool Technology
Contour machining is common for large, complex surfaces like car body panels. However, cast blanks often deform, causing empty tool paths and wasting time.
To avoid this, engineers use the contour surface method. This method limits the tool path to a 2D plane. It reduces the chance of empty cutting. However, it uses an octree to model the 3D surface. This makes it hard to calculate the machining allowance accurately. Many of these surfaces use parametric models, which adds more problems.
So, engineers should analyze the rough machining allowance more carefully. This helps avoid inefficient tool paths.
Modern CNC tools and machines have advanced a lot. But many people still use conservative parameter settings. These settings limit performance. In the future, CNC machining should focus on better efficiency. Engineers need to set parameters that maximize performance without going beyond machine limits.
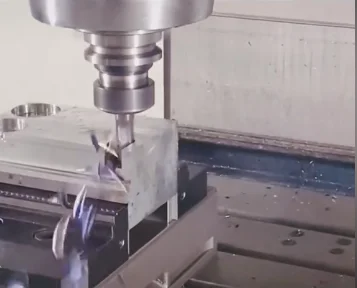
2.3 Cost Control in CNC Machining of Complex Surfaces
The cutting volume affects machining efficiency. But complex part shapes and safety risks often force manufacturers to reduce the feed rate. This lowers productivity. During rough machining, high cutting forces can wear out tools. They can also cause machine vibration and reduce accuracy. These issues increase manufacturing costs.
Right now, engineers still lack good solutions to optimize the feed rate. To finish parts efficiently, they must balance tool life, cutting parameters, and part quality. This helps avoid scratches and reduces the number of tool changes.
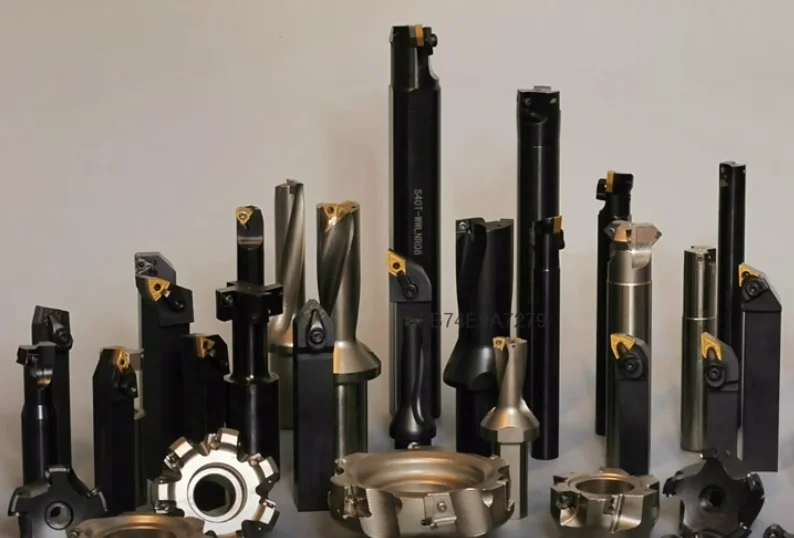
One possible solution is to build a real-time cutting force model. Engineers can use regression analysis to calculate the cutting force coefficient. But this method still needs more testing before it can be used widely.
3 Conclusion
Multi-axis linkage milling uses outer annular discs and inner cyclone trajectories. This method offers high efficiency, flexibility, and low cost. It works well for spiral and slender surfaces. As this technology improves, it will offer better accuracy and handle harder materials in CNC manufacturing.