Hot runner for injection molding is a heating method that ensures the plastic in the runner and gate remains molten. The placement of heating rods and rings near or at the center of the runner keeps the entire runner, from the injection molding machine’s nozzle outlet to the gate, in a high-temperature state.
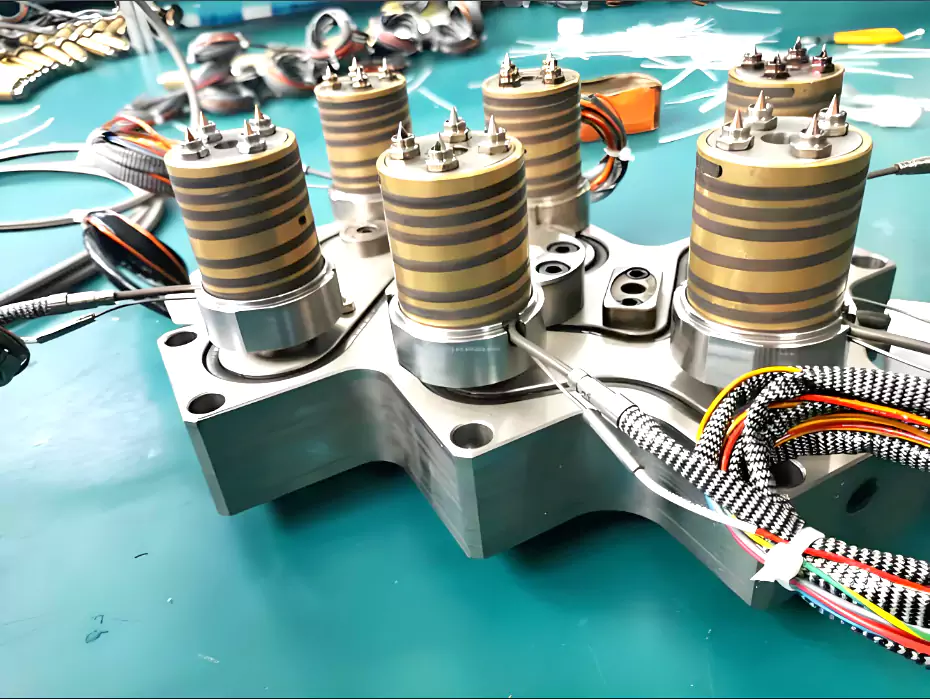
After shutdown, operators avoid opening the runner to remove condensed material; instead, they simply heat the runner to the required temperature when restarting the machine. The application and promotion of hot runner technology are strong driving forces for developing thermoplastic injection molding in the direction of energy savings, low consumption, and high efficiency.
The hot runner injection molding method, introduced in the 1950s, has seen gradual application and promotion over time. Its market share continues to increase annually. By the mid-1980s, hot runner molds accounted for 15% to 17% of all injection molds in the United States, 12% to 15% in Europe, and about 10% in Japan. By the 1990s, U.S. hot runner molds made up more than 40% of plastic injection molds overall and over 90% of molds for large products.
4o The injection mold of large products accounted for more than 90%.
The essential characteristics of the hot runner system
(1) Hot runner molds are most significant for Saving raw materials and reducing product costs.
Ordinary injection molding systems produce a large number of molding systems recycled to the material; in the production of small products, the weight of the injection molding system condensate may exceed the weight of the product.
Since the plastic in the hot runner mold is always molten, the product does not need to trim the gate. This process eliminates waste processing and saves a significant amount of raw materials. Since there is no need for recycling, selection, crushing, dyeing, and other processes, it saves labor, time, and energy.
(2) Improve product quality.
The process improves product quality by preventing the injection material from mixing with the repeatedly processed gate material.At the same time, because the injection molding system keeps the plastic molten, flow pressure loss is small, and it is easy to achieve multiple gates, multi-cavity molds, and large products of low-pressure injection. Hot gating facilitates pressure transfer, and to a certain extent, it can overcome defects such as depression, shrinkage, and deformation of plastic parts due to insufficient replenishment.
(3) Simplified operation and shortened cycle time.
Eliminate the work of taking out the casting system condensate, in operation compared with ordinary runners, shorten the opening and closing stroke, not only the parts of the mold and molding cycle shortened, and is conducive to the realization of automated production. Statistics show that switching to hot runners shortens the molding cycle by 30% compared to ordinary runners.
(4)Wide range of applicable resins, easy-to-set molding conditions.
Advancements in hot runner temperature control system technology now allow the processing of a wide range of materials. Manufacturers can use hot runners for high-melting-temperature plastics like polyethylene (PE) and polypropylene (PP), as well as for heat-sensitive plastics with narrow temperature ranges, such as polyvinyl chloride (PVC) and polyformaldehyde (POM). Additionally, valve-type hot nozzles enable hot runner molding for materials prone to salivation, like polyamide (PA).
(5) Multiple gating methods, feeding balance.
For a mold with multiple cavities or feeding points, operators can balance feed by adjusting the temperature of each runner section and inlet and controlling the gate’s opening and closing times.
Advantages and disadvantages of the hot runner system
Advantages
1.Reduced Material Waste
The hot runner system eliminates the need for traditional cold runners, eliminates gating material, and reduces material waste, especially when processing expensive plastics.
2.Increase productivity
A fast injection cycle reduces mold cooling time and is suitable for mass production.
3.Improve product appearance quality.
There are no sprue marks on the product surface, and the consistency is higher. It is especially suitable for parts with high appearance requirements.
4.Reduced post-processing
Eliminates the shear gate step, reducing labor and subsequent processing costs.
5.Greater Design Freedom
Designers can optimize molds to support complex shapes and multi-cavity configurations.
6.Energy saving and environmental protection
The process reduces material recycling and minimizes energy consumption.
Disadvantages
1.High initial cost
Hot runner molds are expensive to design and manufacture and may be uneconomical for small-batch production.
2.Complicated maintenance
Since the system includes heating elements, controllers, and other precision components, maintenance and replacement are more complex and costly.
3.Difficulty of temperature control
High-temperature control requirements and temperature fluctuations may lead to material degradation or blockage of the channel.
4.Not applicable to certain materials
Some temperature-sensitive materials may decompose due to prolonged heating, affecting product quality.
5.High technical requirements
Operation and commissioning require experienced technicians, and there are certain requirements on the technical level of enterprises.
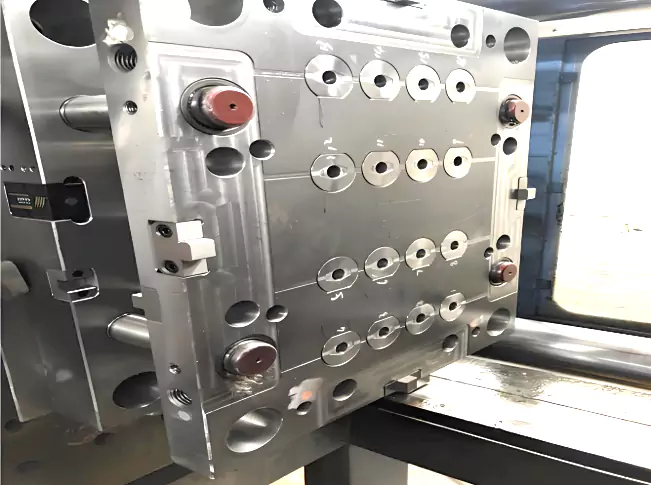
Conclusion
Hot runner, molding technology development, has been quite mature and achieved large-scale industrial applications. With the increasing maturity of hot runner technology, the hot runner system is getting more and more attention and favor. The promotion and application of hot runner molding technology to promote the reform and development of the mold industry has a positive role. Its significant superiority and continuous improvement performance will undoubtedly make this technology faster in the country to get greater popularization and application.