Cutting processing is currently more widely used in the field of mechanical manufacturing processing methods [1], to improve the efficiency of cutting processing, reduce production costs, to promote the economy has important practical significance. With the popularization and development of CNC automation technology, the auxiliary time of workpiece processing is greatly reduced, corresponding to the proportion of time accounted for by the cutting process increases (the total processing time of the part processing for auxiliary time and cutting time and time), to further improve the processing efficiency must reduce the cutting time [2]. The main method of reducing cutting time is to increase the cutting speed and depth of cut, and with the continuous development of precision manufacturing to improve the depth of cut of large-margin cutting development prospects are limited. High-speed cutting can reduce the cutting man-hours while reducing the cutting force and improving the machining accuracy of the workpiece surface, which has been widely used and proved in the aerospace, defense industry, electronics, and precision machinery industries [3]. Therefore, high-speed cutting technology has become one of the important research contents in the current advanced manufacturing field [4].
1. Overview of high-speed cutting technology
German physicist Salomon (Carl.J.Salomon) first put forward the “high-speed cutting” this point of view, the core idea is that any kind of part material corresponds to a critical cutting speed when the cutting speed is less than the critical cutting speed, the cutting force and cutting temperature with the increase in cutting speed and increase; when the cutting speed is greater than the critical cutting speed, the cutting force and cutting temperature with the increase in cutting speed; when the cutting speed is greater than the critical cutting speed, the cutting force and cutting temperature increases; when the cutting speed is greater than the critical cutting speed, the cutting force and cutting temperature increases. cutting speed is greater than the critical cutting speed, the cutting force, and the cutting temperature with the increase in cutting speed but reduced [5]. Thus, high-speed cutting can reduce the cutting time at the same time, reduce the cutting temperature, reduce tool wear, and improve the surface quality of parts processing. At present, there is no accurate definition of the speed of high-speed cutting, there are generally the following two definition methods: one is divided into cutting speed, cutting speed more than 5 times the conventional cutting speed, that is, high-speed cutting; the other is divided into the spindle speed, when the spindle speed more than 8000 r/min, that is, high-speed cutting [6-8]. In production practice, the speed of high-speed cutting is also more closely related to the material and processing methods of parts and thus can not have a more accurate definition of its speed. In addition, high-speed cutting is not only the cutting speed of high-speed, or established in the high-speed cutting mechanism, high-speed cutting key equipment technology, high-speed cutting process on the basis of complex systematic engineering [9], with the development of related technology and the continuous pursuit of technology and efficiency of the organic unity.
2. Advantages and application of high-speed cutting technology
Compared with the traditional ordinary cutting, the advantages and applications of high-speed cutting technology are mainly manifested in the following aspects [10-15].
1) High removal rate, reduce production cost.
High-speed cutting, the spindle speed and feed rate of the substantial increase in the material removal rate per unit of time is greatly increased, cutting hours are greatly reduced, effectively improving the processing efficiency, and production costs are also reduced. In the aerospace, automotive, mold, and other manufacturing areas, some of the overall components of the material removal rate are large, and the use of high-speed cutting can produce huge economic benefits.
2) small cutting force, reduce processing deformation.
Compared with conventional cutting, the high-speed cutting force is small (at least 30% lower), and the shear angle increases, making the chip outflow speed, and cutting deformation small. The use of this feature can effectively reduce the processing deformation of less rigid workpieces, especially suitable for thin-walled, aircraft web and other parts of the processing.
3) Chip heat dissipation and thermal deformation are small.
High-speed cutting time is short, the machining process occurs in a flash, more than 90% of the cutting heat with the chip out of the machine (too late to transfer the heat to the workpiece), the workpiece surface accumulates less heat, and thermal deformation is small. The use of this feature, high-speed cutting on the processing of easy-to-heat, deform, and high precision parts and low melting point, oxidizing the material (such as magnesium) has an important practical significance.
4) Cutting smooth, high precision.
High-speed cutting, high spindle speed, rotating tool excitation frequency, and the machine system’s intrinsic frequency gap is large, will not cause the machine system’s forced vibration, the machining process is smooth; coupled with the cutting force is small, less heat buildup, the tool and the workpiece thermal deformation is small, the friction between the two is small, the machining surface accuracy is high. This characteristic of high-speed cutting makes it widely used in precision machining, special machining, the optical industry, and other fields.
5) Simplify the process and improve productivity.
Quenched material hardness, high strength, conventional cutting can not be processed, it must be processed by electrical discharge machining, and electrical discharge machining will make the surface of the workpiece harden, the need for subsequent processes, the process flow is complex. High-speed cutting can directly process materials with high hardness, eliminating some intermediate processes such as aging treatment, simplifying the process, and improving production efficiency. In addition, the cutting force of high-speed cutting is small, and can use a small radius tool processing small rounded corners and some fine structure, eliminating the subsequent clamp cleaning process.
3. High-speed cutting key technology research
3.1 High-speed cutting mechanism research
The high-speed cutting mechanism is the core and foundation of high-speed cutting technology, playing a guiding role in the entire high-speed cutting system. The high-speed cutting mechanism and the traditional general cutting mechanism are different mainly in the cutting principle, cutting heat and cutting temperature, chip forming, and other aspects. The principle of high-speed cutting is shown in Figure 1 [16-18], the increase in cutting speed of the tool makes the tool and the workpiece between the squeezing force and the tool and the friction between the chip increase, the increasing friction makes the tool and chip contact area of the temperature rises, the rising temperature reaches the melting point of the workpiece material, the part of the contact area is molten, the molten state of the part of the lubrication can play a role. The molten part can play the role of lubrication and reduce the friction factor. The reduction of regional friction makes the chip breakage an almost unopposed chip flow, which reduces the chip force on the tool. In addition, compared with the traditional ordinary cutting process, the shear angle of high-speed cutting increases, then the corresponding cross-section shear surface decreases, and the plastic deformation area of the workpiece decreases; most of the heat is gathered in the chip and discharged out of the machine, and a very small part of the heat is transmitted to the tool and the workpiece.
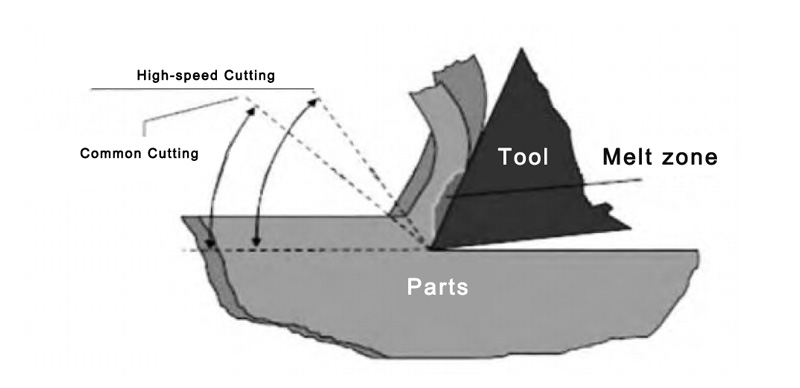
(Figure 1)
The high-speed chip forming mechanism is the core content of the high-speed cutting mechanism, sawtooth chip is the main performance form of the high-speed chip. A serrated chip is a typical material mechanics instability state, its cutting force and cutting temperature is a periodic change state [19-20], affecting the entire high-speed cutting process. There are two main theoretical systems for the study of the formation mechanism of serrated chips: the adiabatic shear theory based on thermal coupling [21-23] and the periodic brittle fracture theory based on dynamic force [24-26]. The adiabatic shear theory suggests that sawtooth shavings are thermoplastic instabilities due to the localized high temperature-induced thermal softening effect caused by heat buildup from large plastic deformations of the material at high strain rates exceeding the strain-hardening effect of the material (see Fig. 2a) [27]. The brittle fracture theory suggests that serrated chips are produced due to periodic fracture, which first produces cracks on the chip surface (see Fig. 2b) and gradually extends internally along the shear zone, ultimately leading to abrupt failure and the production of serrated chips. The theoretical basis of the former is heat transfer science, and the theoretical basis of the latter is fracture mechanics. Shandong University’s Yang Qibiao et al [28] summarized these two theories, for plastic materials or brittle materials in the cutting process transformed into plastic materials to form the sawtooth chip can be explained by adiabatic shear theory, for the formation of brittle materials sawtooth chip can be explained by the theory of cyclic fracture. In short, there is a lack of a unified understanding of the formation mechanism of serrated chips in the high-speed cutting process, which requires further research.
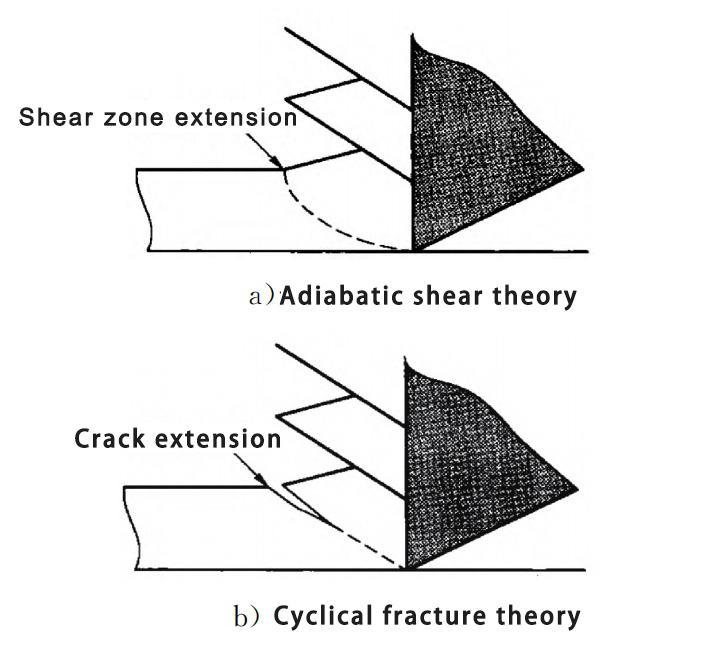
(Figure 2)
3.2 Research on high-speed cutting key equipment technology
1) High-speed cutting machine tools.
High-speed cutting machine tools, as the basic core equipment for high-speed cutting processing, mainly include spindle systems, rapid feed systems CNC control systems, and other institutions. A high-speed spindle system as the core of one of the key technologies, should have the following performance requirements [29-31]:
a. Compact structure, good start-stop performance;
b.High speed and wide speed range;
c. High stiffness and high rotary accuracy;
d. Good thermal stability;
e. Advanced and reliable lubrication and cooling system;
f. Stable monitoring and feedback system.
In order to meet the above performance requirements, high-speed spindle directly into an electric spindle (motor and spindle into one) in the form of the spindle internal AC servo motor directly driven by the integrated structure.
A high-speed spindle must be equipped with a fast feed system for use, the traditional ball screw nut sub-feeding mechanism of low transmission efficiency, is unable to meet its performance requirements. In order to adapt to the requirements of high-speed precision, the guideway adopts the linear structure with embedded ball bearings (small contact area, low friction); in order to obtain high feeding speed and acceleration, the feeding mechanism can adopt high-quality small-pitch ball screws, and the motor can adopt advanced and high-speed linear motors (linear motor eliminates the transmission gap, reduces transmission friction, and realizes “zero transmission”, high transmission accuracy). The linear motor eliminates the transmission gap, reduces transmission friction, and realizes “zero transmission” and high transmission precision [32-33]).
In high-speed cutting machining, the CNC control system is required to have the following performance:
a. The ability to process data quickly;
b. Forward-looking calculation control function;
c. Geometric and thermal compensation.
The traditional CAD data converted to point-to-point tool path trajectory has been unable to meet the above performance requirements, NURBS interpolation, smooth interpolation, bell-shaped acceleration and deceleration, and other contouring control technology.
2) High-speed cutting tools.
High-speed cutting process, tool wear, and balance failure a common phenomena in high-speed cutting processing [34]. In order to meet the requirements of modern high-speed machining technology, high-speed cutting tools should be “three high and one special” – high precision, high efficiency, high reliability and specialization [35-36], which corresponds to the technical basis for the tool material, coating and tool structure. Tool materials and coatings are of great significance to the development of high-speed cutting and machining technology, and high-speed tool materials and coatings are mainly of the following kinds: TICN-based cemented carbide tools, ceramic tools, diamond tools, PCBN (man-made cubic boron nitride) tools, etc. TICN-based cemented carbide tools and ceramic tools are mainly suitable for high-speed machining of steel and its alloys; diamond tools are mainly suitable for aluminum alloys, Titanium alloys, copper alloys, non-ferrous metals and non-metallic materials for high-speed machining; PCBN tools are mainly suitable for cast iron alloys, hardened steel, nickel-based alloys and other high-temperature alloy materials for high-speed machining. The structural parameters of the tool directly affect the service life of the tool and the machining quality of the parts. Compared with the traditional tools for general machining, the front angle of high-speed cutting tools is smaller (generally small 10°), and the rear angle is larger (generally larger 5° to 8°).
In order to improve the rigidity of high-speed cutting tools and reduce tool wear, it can be achieved by increasing the tip angle (the main and secondary cutting edge connection can be rounded tip or chamfered tip) and increasing the length of the cutting edge near the tip. In addition, due to the high speed of the spindle during high-speed cutting, high-speed rotation of the tool structure must meet the requirements of the balance quality. Under high-speed rotation, in order to avoid high-speed centrifugal force damage to the tool, the tool holder device must maintain sufficient clamping force and safety and reliability. Currently, there are two main types of two-sided positioning tool holders: one is through the technical improvement of the traditional solid BT shanks, such as Japan’s BIG-PLUS series, etc.; the other is through the innovative design of the 1:10 hollow short taper tool holder system, such as Germany’s HSK series. The traditional solid BT tool holder with a 7:24 taper has low positioning accuracy and insufficient connection rigidity to meet the requirements of high-speed cutting machining [37]. In order to ensure sufficient clamping force and positioning accuracy, a close-fitting type tool holder that is simultaneously positioned with the taper and end face of the spindle bore has been developed.
3.3 Research on high-speed cutting process technology
The high-speed cutting machining process is very different from the traditional general machining process, The high-speed cutting process design principle is to give full play to the advantages of high-speed cutting, design a reasonable process plan, so as to achieve high efficiency and high quality. The study of high-speed cutting process technology mainly includes the selection of cutting mode, cutting amount and tool walking mode. High-speed cutting should try to use smooth milling processing, which is due to the smooth milling, the cutting thickness from large to small, the teeth in the cutting surface of the sliding distance is small, the distance traveled is short, the surface of the workpiece smoothness is good;
While reverse milling, the cutting thickness from small to large, the friction between the tool and the workpiece increases, the radial force also increases greatly, coupled with the cutting edge will produce a large amount of heat resulting in easy tool wear; high-speed cutting, different tools cutting different materials of the workpiece, the choice of cutting dosage is also not the same, but high-speed milling cutting dosage selection principle is generally a medium amount of feed per tooth, a smaller axial depth of cut and appropriate large radial depth of cut [38]. The selection of tool travel mode mainly includes optimization of tool travel direction, optimization of tool travel path and flexible acceleration and deceleration. The optimization of tool travel direction should be evaluated based on the flatness of the surface; the optimization principle of tool path is simple and smooth, and the interference zone can be processed by the method of arc transition; for the flexible acceleration and deceleration, a suitable acceleration and deceleration method should be selected to reduce the start-stop impact and ensure the machining accuracy of the machine tool.
4. Prospect of high-speed cutting technology
4.1 Strengthen the in-depth study of high-speed cutting mechanism
In the theoretical aspects of high-speed cutting processing, although a lot of research has been carried out and some research results have been achieved, but overall it is still unable to meet the needs of production practice, further in-depth research is needed. Can be strengthened from the following aspects of high-speed cutting mechanism of in-depth research:
1) digital description and prediction of cutting force and cutting heat distribution law;
2) difficult-to-machine materials, composite materials, microfabrication chip formation mechanism research;
3) the description of the tribological behavior of the tool-chip interface and the study of tool wear mechanism;
4)monitoring and prediction of tool life;
5) cutting dynamics of the time domain, frequency domain modeling analysis.
4.2 Accelerate the development of ultra-high-speed high-power machine tools
Ultra-high-speed high-power machine tools is the inevitable result of the development of high-speed cutting technology, although China has conducted some research in ultra-high-speed machine tool technology, but there is still a certain gap compared with foreign advanced technology. Ultra-high-speed high-power machine tool research mainly includes:
1) high-power, ultra-high-speed spindle unit technology;
2) ultra-high-speed feed unit technology;
3) ultra-high-speed CNC system technology.
High-power, ultra-high-speed spindle technology research mainly includes spindle material and structure optimization, ultra-high-speed precision bearing design and development, spindle self-balancing technology, spindle multi-objective optimization technology. The research of ultra-high-speed feeding unit technology mainly includes high-speed linear feeding motor technology, high acceleration and deceleration control technology, the development of high-speed positional chip ring, the development of precision large lead screw vice. Ultra-high-speed CNC system technology research mainly includes smooth acceleration and deceleration characteristics of intelligent control, feed-forward control and automatic error compensation technology.
4.3 New tool materials and structure technology research tool materials and structure with the development of high-speed cutting technology needs and development. Ceramic tools in the field of high-speed cutting is more widely used, but its strength, fracture toughness and thermal shock resistance should be further optimized, can be optimized from the gradient function of ceramic tools, nano and micron composite ceramic tools and whiskers and particles of synergistic toughening of ceramic tools in several aspects to optimize the research. Coated tools have great potential in the field of high-speed cutting and machining, but the existing coating material (such as TICN, etc.) is not high in heat resistance and wear resistance, and further research should be conducted on new coating technology, coating materials, especially the research and development of self-lubricating high-speed dry cutting of coated tools. In terms of tool design, multifunctional and specialized tools are the future direction of development. The advantages of multifunctional tools are mainly reflected in the machining center, which can reduce the number of tool changes and the number of tools, improve productivity and reduce production costs. In the machining production line, special tools can be developed for a specific process, so as to improve production efficiency.
4.4 Construct intelligent high-speed cutting cloud processing database High-speed cutting processing database can intelligently provide cutting site-oriented process data according to production requirements. The core of the high-speed cutting database is based on the cutting force model, cutting temperature model, tool wear model and workpiece surface quality model of intelligent prediction, however, with the continuous development of new processes and new technologies, making the cutting database has a strong timeliness. At present, cloud computing technology and artificial intelligence theory can be used to build an intelligent high-speed cutting cloud processing database based on the physical model of high-speed cutting process, combined with production practice and a large number of cutting tests.
4.5 High-speed cutting process online monitoring technology research high-speed cutting process, tool vibration and wear on the workpiece machining surface quality of the impact is crucial to the tool state and the workpiece surface quality of online monitoring is the development direction of high-speed cutting technology. Online monitoring is the tool vibration and wear and surface quality of the workpiece to establish a link, and according to a large number of actual production experience to set a reasonable value of the can, by monitoring the tool vibration signal is normal, the surface roughness of the workpiece is qualified, the feedback adjustment process parameters, replacement of the tool, adjust the equipment to ensure that the high-speed cutting is carried out normally.
4.6 Dry cutting-based green cutting technology research high-speed cutting can reduce energy consumption to a certain extent, but in the high-speed cutting process can not be avoided using a large amount of coolant, the environment has also caused some pollution. Green, energy saving and emission reduction is the main development direction of the future manufacturing industry, dry cutting-based green cutting is the future focus of high-speed cutting research areas. Dry cutting is a kind of machining process without using or micro-use of cutting fluid processing technology, in reducing pollution at the same time, can also save the cutting fluid-related devices, simplify the production system, reduce production costs.
5. Conclusion
The following conclusions can be drawn from the above research.
1) High-speed cutting technology is the current focus of research in the field of advanced manufacturing. High-speed cutting is not only the cutting speed of high-speed but also established in the high-speed cutting mechanism, high-speed cutting key equipment technology, high-speed cutting process based on a complex system engineering, is with the development of related technology and the continuous pursuit of technology and efficiency of the organic unity.
2) Compared with conventional cutting, high-speed cutting technology mainly has the following advantages:
a. High removal rate, reduce production costs;
b. Small cutting force, reduce processing deformation;
c. Chip heat dissipation, small thermal deformation;
d. Smooth cutting, high precision;
e. Simplify the process, and improve productivity.
3) To promote the development of high-speed cutting technology mainly from the following aspects:
a. Strengthen the high-speed cutting mechanism of in-depth research;
b. Accelerate the development of ultra-high-speed high-power machine tools;
c. Strengthen the research of new tool materials and structural technology;
d. Construction of intelligent high-speed cutting cloud processing database;
e. To carry out high-speed cutting process online monitoring technology research;
f. Focus on strengthening the dry-cutting-based green-cutting technology research.
Reference:
[1]Wu Minjing. High-efficiency and high-speed machining is the main theme of the current machinery manufacturing field [J]. Aviation manufacturing technology, 2005(4):53-57.
[2] Lu Jie, Li Xiaoyou. High-speed cutting technology and its application in aircraft structural parts processing[J]. Coach, 2011(2):25-28.
[3]Yu Jing, Dong Hai, Zhang Hongtao. Research status of high-speed cutting mechanism[J]. Tool Technology, 2011, 45(11):3-6.
[4]Ai Xing, et al. High-speed cutting and machining technology [M]. Beijing: National Defense Industry Press, 2003.
[5]KahlesJF,Field M,HarveyS M. Highspeed machi-ning possibilitiesandneeds[J]. AnnalsofCIRP,1978,27(2):551-558.
[6] Gao Xiang, Wang Yong. Application of high-speed milling tools in high-speed cutting processing[J]. Combined machine tools and automatic processing technology, 2009(8):84-87.
[7]Miu Xia. Discussion of some problems in the application of high-speed cutting [J]. Equipment manufacturing technology, 2013(12):128-131.
[8] Cao Yali. High-speed cutting technology and development [J]. Light Industry Science and Technology, 2013, 29(7):57-58.
[9]Gong Houxian. CNC high-speed cutting processing technology development and application research [J]. Digital technology and application, 2011(6):7-8.
[10]Wang Li Min. Discussion on the application of CNC high-speed cutting machining technology in machinery manufacturing [J]. Internal combustion engine and accessories, 2020 (3): 77-78.
[11]Wang Jingjing, Li Xinmei. High-speed cutting machining technology and its important application areas analyzed [J]. Machine tools and hydraulics, 2015, 43(4): 177-180, 94.
[12] Li Zhongxin, Huang Chuan, Liu Yanyou. Key technology and development direction of high-speed cutting machining [J]. China Journal of Construction Machinery, 2014, 12(1):48-51.
[13]Bai Kun. Ultra-high-speed cutting processing and its key technologies [J]. New Technology and New Process, 2009(9):63-65.
[14]Pan Peidao. High-speed cutting technology and its application in mold manufacturing [D]. Hefei: Hefei University of Technology, 2007.
[15]Xiong Jianwu, Zhou Jin, Chen Xiangshun. The characteristics and application requirements of high-speed cutting technology [J]. Science, Technology and Engineering, 2006(10):1404-1406.
[16] Jiao Pixian, Li Lin, Xiao Guanglin, et al. Introduction to high-speed cutting processing technology in the use of CNC machine tools [J]. China equipment engineering, 2021(8):192-194.
[17] Liu Yang. Introduction to high-speed cutting processing technology [J]. Mold manufacturing, 2014, 14 (8): 89-93.
[18] Liang Qing. Application of high-speed cutting technology in precision parts processing[J]. Equipment manufacturing technology, 2014 (1): 72-74.
[19] Duan Chunqiang, Wang Zhaoxi, Li Honghua. Finite element modeling of high-speed cutting sawtooth chip formation process [J]. Journal of Harbin Engineering University, 2014, 35(2):226-232.
[20] Ye Guigen. Research on the mechanism of high-speed metal cutting [D]. Qingdao: China University of Petroleum (East China), 2012.
[21]DaiL H, LiuLF, BaiY L. Formation of adiabaticshearbandin metal matrixcomposites[J]. InternationalJournalofSolidsandStructures,2004,41(22): 5979-599. ): 5979-5993.
[22]SemiatinSL,RaoSB. Shearlocalizationduringmetalcutting[J]. MaterialsScienceand Engineering,1983,61(2):185-192.
[23]RechtRF. Catastrophic thermoplasticshear[J]. Jour-nal of Applied Mechanics, 1964, 31(2):186-193.
[24] VyasA, Shaw M C. Mechanicsofsaw-toothchipfor-mationinmetalcutting[J]. JournalofManufacturingScienceandEngin Journal of ManufacturingScience and Enginering, 1999, 121(2):163-172.
[25] ElbestawiM A, SrivastavaA K, El-WardanyTI. A modelforchipformationduringmachiningofhardenedsteel[J]. CIRP Annals – ManufacturingTechnology, 1996, 45(1):71-76.
[26] Shaw M C, VyasA. Chipformationinthemachiningofhardenedsteel[J]. Elsevier, 1993, 42(1):29-33.
[27]Ming Chen, Qinglong An, Zhiqiang Liu. Basis and application of high-speed cutting technology [M]. Shanghai: Shanghai Science and Technology Press, 2012.
[28] Yang Qibiao, Liu Zhanqiang, Su Guosheng. Research status and development of high-speed cutting serrated chip formation mechanism[J]. Tool Technology, 2011, 45(3):3-11.
[29]Ma Shuai, Umbrella Hongjun, Wu Zhiheng, et al. Review of high-speed electric spindle technology[J]. Machinery Manufacturing, 2014, 52(5):16-19.
[30] Guo Xudong. Analysis of high-speed electric spindle structure of CNC machine tools[J]. Science and technology innovation guide, 2010 (35): 40.
[31] Shao Chuanwei. Electric spindle and high-speed machining technology[J]. World manufacturing technology and equipment market, 2002(5):21-23.
[32]Luo Jing, Xiao Tiezhong, Huang Juan. Design and research of press machine tool driven by linear motor [J]. Machine tools and hydraulics, 2015, 43(21): 142-145.
[33] Song Hongzhi, Yang Qingdong, Mou Bing. Research on the control strategy of CNC machine tool linear motor load mutation [J]. Mechanical Engineering and Automation, 2015(4):160-161, 164.
[34]Jiaqi Xu, Dong Wang. Tool material requirements and selection in high-speed cutting machining [J]. Journal of Jiamusi University: Natural Science Edition, 2021, 39(2): 111-113.
[35]Shao Junjie. Parameterization design of titanium alloy special milling cutter and its experimental study [D]. Shanghai: Shanghai Jiaotong University, 2009.
[36]Xue kingland. Evaluation of cutting performance of coated tools and its experimental study [D]. Shanghai: Shanghai Jiao Tong University, 2008.
[37] Yuan Feng, Wang Taiyong, Wang Shuangli. Development and Research of High-speed Cutting Technology[J]. Machine Tools and Hydraulics, 2005(12):8-11.
[38] He Ning, Li Liang. High-speed cutting process technology [J]. Mechanical Engineering (Cold Processing), 2003(9):23-26.