1 Survival Status of the Injection Mold Manufacturing Industry
In recent years, advancements in CNC technology and intelligent manufacturing have pressured the traditional mold manufacturing industry. These changes have created major challenges. The industry now faces talent shortages, limited product diversity, and intense competition.
1.1 Talent Shortage in the Industry
The mold industry, known as the “mother of industry,” is shrinking in the secondary sector. The supply of skilled high-end professionals does not meet demand. Training programs for mid and low-end talent have disappeared. Vocational schools have reduced relevant courses. This decline has caused a shortage of skilled labor. Many mold companies in coastal regions like Guangdong struggle to find qualified workers. The industry must improve talent development to ensure long-term growth.
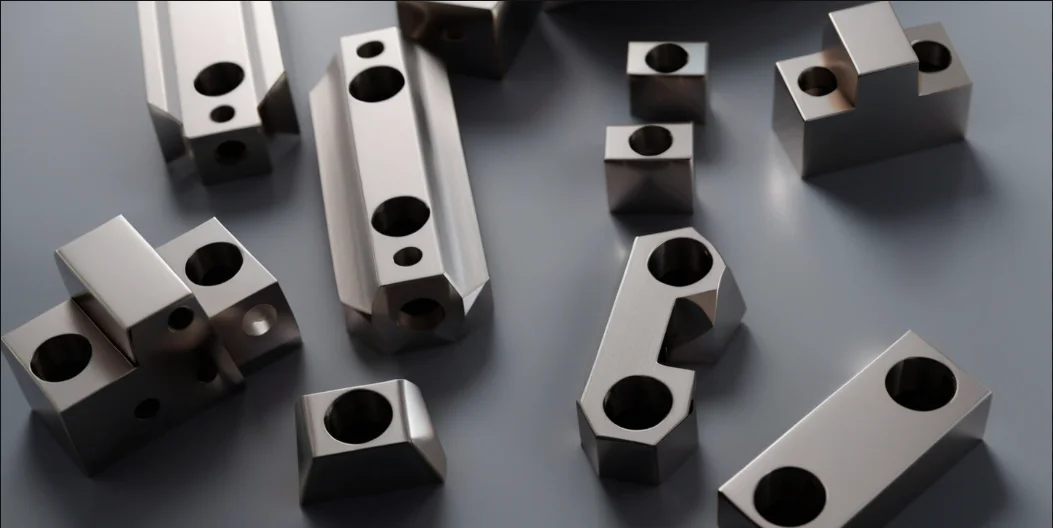
1.2 Challenges in Product Diversity and Business Flexibility
Mold manufacturing focuses on customized mass production. The production of precision injection molds requires advanced equipment and skilled workers. However, most Chinese mold manufacturers produce low- and mid-end products. The country still relies on imports for high-end precision molds. To compete, companies must innovate and upgrade their production processes. Intelligent manufacturing systems can help them improve efficiency and product quality.
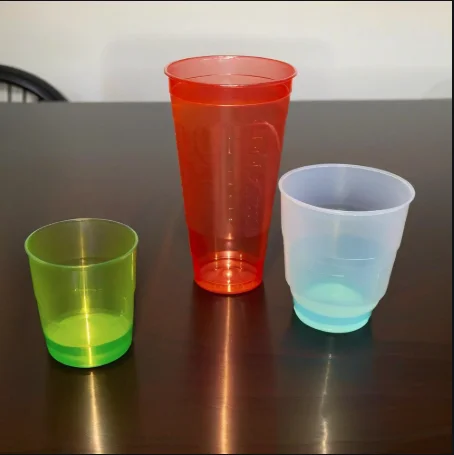
1.3 Industry Competition and Market Fragmentation
China’s mold industry operates mainly in the Yangtze River Delta, the Pearl River Delta, and the Bohai Rim. Leading companies focus on brand development, technology, and strategic planning. However, rapid expansion in previous years created oversaturation. Many regions built mold parks and attracted excessive capital. Poor planning and similar business models led to price wars. Many low-end companies failed and shut down. In contrast, firms with strong R&D and skilled workers successfully adapted. They improved their technology, management, and business strategies to survive.
2 Market Fundamentals of Injection Mold Manufacturing
2.1 Sustained Demand for Injection Molds
Injection mold design must meet national safety standards. These include fire resistance, waterproofing, and earthquake resistance. Designers must also consider cost, aesthetics, and environmental impact. They need to create reliable structures and layouts that support mass production. They should use scientific calculations to determine component specifications. Arbitrary decisions can lead to inefficiencies and increased costs. Innovation must align with industry standards and design principles.
2.2 Standardization in Injection Mold Manufacturing
Advances in information technology have improved industry collaboration. Standardized designs and interchangeable parts help mold manufacturers expand into global markets. Since joining the WTO, Chinese companies have strengthened compliance with international standards. These efforts have opened new market opportunities and supported industry transformation.
2.3 Economic Viability of Injection Mold Products
Production efficiency affects an injection mold’s economic value. Companies must balance efficiency with cost-effectiveness. They should avoid wasting resources while maximizing output. Industrialization remains the best way to increase efficiency. The widespread use of injection molds has played a crucial role in achieving this goal.
2.4 High Production Efficiency of Injection Mold Products
Injection mold manufacturing increases production speed and reduces raw material consumption. It also improves feasibility while following economic and environmental principles. Many industries use injection molds because they increase efficiency and lower labor costs. Automation and intelligent manufacturing further improve large-scale production.
3 Future Trends in Injection Mold Design and Manufacturing
Shift Toward Micro and High-Precision Mold Technology
China’s mold industry produces too many low-end products. At the same time, demand for high-end precision molds continues to grow. Companies must invest in advanced technology, better equipment, and high-end product development. Traditional manufacturing methods can no longer meet the rising need for precision.
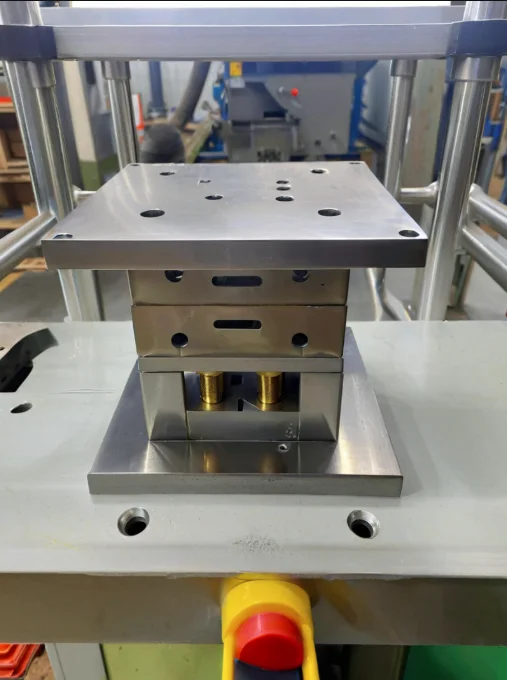
3.1 Green and Environmentally Friendly Manufacturing
In the past, mold manufacturers focused only on function and cost. They did not consider environmental impact. However, resource depletion and ecological concerns now make sustainability a priority. Companies must use eco-friendly materials and improve resource efficiency. They should also adopt pollution-free processes. These steps will help them maintain both quality and environmental responsibility.
3.2 Modularization of Mold Production Management
China’s plastic mold industry has improved, but it still lags behind Western countries. Companies lack experience in high-end design and manufacturing. This slows industry growth. Technical barriers between companies prevent the widespread use of modular production management. These challenges make it difficult for the industry to advance.
4 Conclusion
Manufacturing demands and processing capabilities are increasing. Injection mold production is shifting from manual craftsmanship and traditional machining to CNC processing and automation. These changes improve production methods, business strategies, and product quality. They also shorten production cycles and enhance supporting capabilities. Increasing self-sufficiency in high-end mold production will boost economic benefits. It will also help the industry move toward intelligence and sustainability.