1. How Machine Tool Fixtures Have Changed
Machine tool fixtures have evolved through three key phases. Initially, they simply helped speed up manual work.
In the second phase, fixtures became a crucial link between operators and machines. Their main job became positioning and securely holding workpieces. People increasingly realized that fixtures greatly affected operator productivity and machine performance.
The current, third stage involves fully integrating fixtures with machine tools. Now, they are essential for mechanical processing. Designing them requires carefully considering workpiece positioning and clamping. However, even with this understanding, small design errors can cause operational problems and reduce workpiece accuracy.
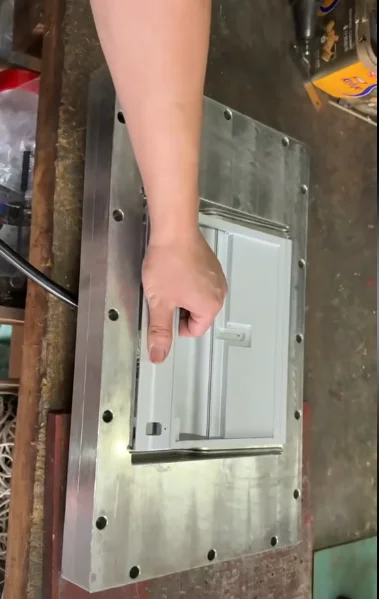
2. Modern Machine Tool Fixture Development
Four main advancements define the direction of modern machine tool fixtures: standardization, precision, efficiency, and flexibility.
(1) Standardization:
Standardizing and generalizing machine tool fixtures offer mutual benefits. Existing national standards cover fixture parts, components, and general and combined fixtures. This enhances the commercial viability of fixtures. This standardization also streamlines production preparation and lowers overall costs.
(2) Enhanced Precision:
The increasing accuracy demands of mechanical products have raised the precision requirements for fixtures. Modern precision fixtures have various designs. High-accuracy indexing multi-tooth discs achieve ±0.1″ indexing accuracy. Precision turning three-jaw chucks boast a 5µm centering accuracy.
(3) Increased Efficiency:
Efficient fixtures aim to minimize fundamental and auxiliary processing times. This boosts productivity and reduces the physical strain on workers. Common examples include automated fixtures, high-speed fixtures, and fixtures with clamping force mechanisms. Using electric vises on milling machines can increase efficiency by about five times. High-speed three-jaw chucks can still clamp firmly at 9000r/rpm. This significantly increases cutting speeds. Today, production lines and CNC machine tools widely use efficient, automated fixtures and automatic replacement devices. This fully utilizes the performance of CNC machine tools.
(4) Enhanced Flexibility:
The flexibility of machine tool fixtures means they can adapt to changes in processes, production batches, and workpiece shapes and sizes. They do this through adjustment and modularity. This includes combination fixtures, universally adjustable fixtures, grouped fixtures, modular fixtures, and CNC fixtures. To meet the needs of diverse, small to medium-volume production, the main focus in fixture development is to improve flexibility. This involves changing fixed special fixtures into detachable structures. It also involves developing more adaptable fixture designs.
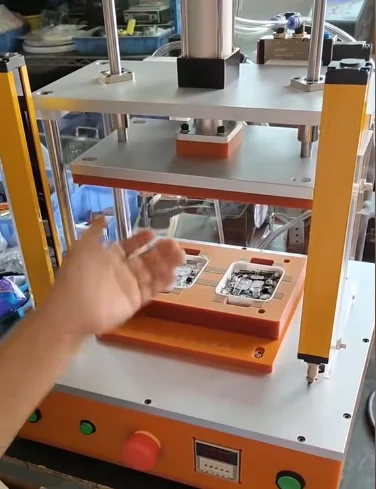
3. Conclusion
The increasing demands of modern bow and arrow manufacturing have driven the evolution of machine tool fixtures. They are moving towards standardization, precision, efficiency, and flexibility. The characteristics of high efficiency and precision in modern fixtures directly help reduce processing times. They also improve productivity and lessen the physical demands on workers. Therefore, deeply understanding fixture principles and designing new, practical fixtures are very important in today’s manufacturing world.