What is A CNC Milling Machine?
A CNC (Computer Numerical Control) milling machine is a computer-controlled tool that uses a rotating cutting tool to remove material from a workpiece to shape it into the desired form. CNC milling machines are widely used in various industries, including manufacturing, aerospace, automotive, and engineering, for the precise and efficient production of parts and components.

The Main Components of CNC Milling Machine
The main components of a CNC milling machine include:
Machine Base: The machine base is the foundation of the CNC milling machine. It provides stability and support for all other components and the workpiece.
Worktable: The worktable is where the workpiece is secured and held in place during the machining process. It can move along multiple axes to position the workpiece accurately.
Spindle: The spindle is a high-speed rotating shaft that holds and drives the cutting tool. It is responsible for rotating the cutting tool and controlling its vertical movement.
Cutting Tool: The cutting tool, such as an end mill or drill bit, is the component that removes material from the workpiece. It is attached to the spindle and cuts into the workpiece as it rotates.
Tool Changer: Some CNC milling machines are equipped with an automatic tool changer that can store and switch between various cutting tools. This feature allows for versatility in machining operations without manual tool changes.
Control Panel: The control panel contains the user interface, typically a computer with software that allows operators to input and control the machining parameters. This is where the CNC program is loaded and where the operator can monitor and adjust the machine’s operations.
Drive Motors: Drive motors are responsible for moving different components of the CNC milling machine along various axes (typically X, Y, and Z). These motors provide precise control over the positioning and movement of the worktable, spindle, and cutting tool.
Guideways: Guideways are linear or sliding mechanisms that provide precise movement and support for the different machine components. They ensure that the worktable, spindle, and other parts move accurately along their respective axes.
Coolant System: A coolant system is essential for maintaining the cutting tools and workpiece at an optimal temperature during machining. It helps dissipate heat, reduce friction, and remove chips and debris, thereby improving tool life and workpiece quality.
These components work together to automate the milling process, allowing for the precise and efficient removal of material from a workpiece to create complex shapes and precision parts. CNC milling machines are highly versatile and are used in a wide range of industries for various machining tasks.
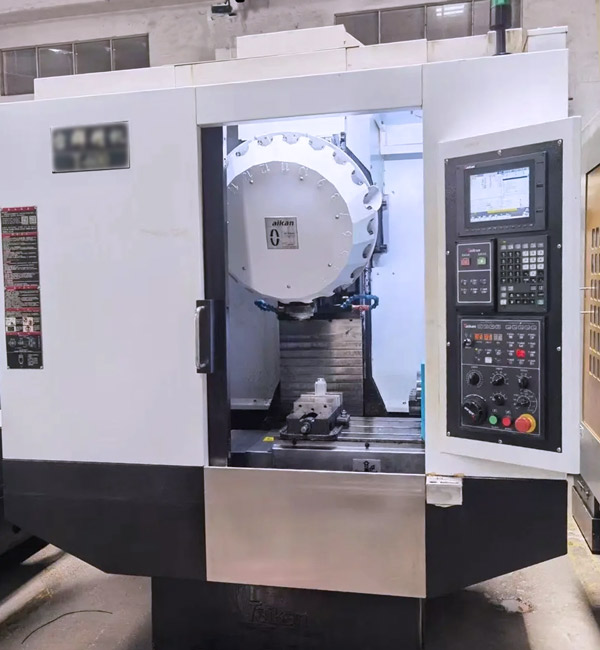
Function of CNC Milling Machine
The primary function of a CNC milling machine is to automate the process of removing material from a workpiece to create precise and complex shapes or parts. It accomplishes this function through the following key operations:
Material Removal
The CNC milling machine uses a rotating cutting tool, such as an end mill or a drill bit, to remove material from a workpiece. The cutting tool is controlled by computer programs that dictate its path and depth of cut, allowing for precise material removal.
Here’s an overview of how material removal occurs in a CNC milling machine:
Workpiece Setup:
The workpiece, which is typically a block or piece of material, is securely clamped or fixtured onto the machine’s worktable. It’s important to ensure that the workpiece is firmly held in place to prevent movement during the machining process.
CNC Programming:
A CNC program, generated using computer-aided design (CAD) and computer-aided manufacturing (CAM) software, is loaded into the CNC milling machine’s control system. This program contains instructions for the tool’s movement, including the toolpath, feed rates, cutting speeds, and other parameters.
Tool Engagement:
The CNC milling machine engages the selected cutting tool, which is held in the machine’s spindle. The spindle rotates the tool at high speeds, and the tool is positioned above the workpiece.
Material Removal:
The CNC program directs the tool to move along a predefined toolpath, which may involve making cuts in multiple axes (X, Y, and Z). As the tool moves, it comes into contact with the workpiece, and material is progressively removed through a combination of cutting and chip formation.
Feed Rates:
The CNC machine controls the feed rate, which is the rate at which the tool is moved into the workpiece. This determines the depth of cut and the speed at which material is removed. The optimal feed rate depends on factors such as the material being machined, tool type, and toolpath complexity.
Coolant and Chip Management:
During material removal, heat is generated, and chips are produced. A coolant system is often used to manage the temperature and prevent tool overheating. The coolant also helps flush away chips and debris, keeping the cutting area clear and reducing friction, which extends tool life.
Multiple Passes:
Depending on the desired part geometry and machining requirements, multiple passes or toolpath strategies may be employed. The CNC program will specify the number of passes and any necessary tool changes.
High Precision Machining:
CNC milling machines are capable of extremely high precision and accuracy. They can produce parts with tight tolerances and complex geometries, making them suitable for applications where precision is crucial.
Versatility:
CNC (Computer Numerical Control) milling machines are highly versatile and can be used for a wide range of applications across various industries. Their versatility stems from their ability to work with different materials, create complex shapes, and perform various machining operations. Here are some aspects of their versatility:
Materials: CNC milling machines can work with a wide range of materials, including but not limited to:
Metals: Such as aluminum, steel, stainless steel, brass, and titanium.
Plastics: Including acrylic, nylon, and polycarbonate.
Composites: Like carbon fiber and fiberglass.
Wood: Used in industries like furniture making and cabinetry.
Ceramics: For precision components.
Exotic materials: Such as superalloys and advanced engineering materials.
Complex Geometry: CNC milling machines are capable of producing parts with intricate and complex geometries, including pockets, holes, curves, angles, and bevels. This makes them suitable for applications that require intricate designs.
Precision:
They can achieve high levels of precision and accuracy, making them ideal for applications where tight tolerances are critical, such as aerospace, medical devices, and automotive components.
3D Machining:
CNC milling machines have multiple axes (typically X, Y, and Z), which allow for 3D machining. This is essential for creating parts with varying contours and complex shapes.
Prototyping and Production: CNC milling machines are suitable for both prototyping and production. They can create one-off custom parts as well as large batches of identical components, making them adaptable to the needs of different manufacturing scenarios.
Customization:
CNC milling machines can be programmed to produce custom parts, allowing manufacturers to meet specific design requirements.
Reduced Lead Times:
They can significantly reduce lead times compared to traditional manual machining methods, enabling faster product development and delivery.
Industry Applications:
CNC milling machines find applications in various industries, including aerospace, automotive, medical, electronics, tool and die making, mold making, woodworking, and more.
Multiple Axes of Motion:
Most CNC milling machines have multiple axes of motion, typically three (X, Y, Z), which allows for 3D machining. Some advanced machines have additional axes, enabling even more complex operations.
Automated Operation:
CNC milling machines operate based on computer programs (G-code or CAM files). The computer-controlled machine can work continuously, with minimal operator intervention, reducing the need for manual labor.
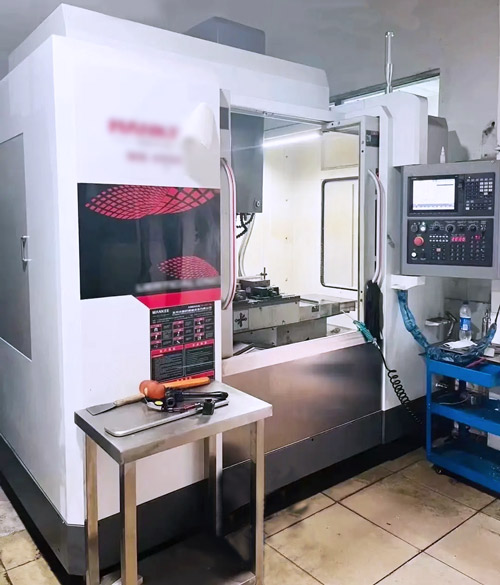
Working Principle of CNC Milling Machine:
The working principle of a CNC (Computer Numerical Control) milling machine involves the automation of the material removal process, where a computer controls the movement of a cutting tool to shape a workpiece. Here is a detailed explanation of the working principles of a CNC milling machine:
Design and Programming
The process begins with the design of the part or component using computer-aided design (CAD) software. Once the design is complete, the CAD file is converted into a CNC program using computer-aided manufacturing (CAM) software. This CNC program contains all the instructions for machining the workpiece.
Workpiece Setup
The workpiece, typically a block or sheet of material (such as metal, plastic, or wood), is securely clamped or fixtured onto the machine’s worktable. The workpiece’s position and orientation are set according to the CAD/CAM design.
Tool Selection and Setup
The appropriate cutting tool is chosen based on the material, desired machining operations, and toolpath requirements. The selected tool is mounted in the machine’s spindle and properly aligned.
CNC Control
The CNC program, generated in the previous steps, is loaded into the CNC milling machine’s control system. This program is interpreted by the machine’s controller, which contains a computer and software.
Toolpath Execution
The CNC machine follows the toolpath defined in the program. It uses precision drive motors to move the worktable and the spindle along multiple axes (commonly X, Y, and Z) with high accuracy. The toolpath instructs the machine to engage with the workpiece and remove material.
Material Removal
As the CNC milling machine follows the toolpath, the cutting tool is rotated at high speeds by the spindle, and it is fed into the workpiece. The tool’s contact with the workpiece results in material removal through cutting and chip formation.
Control Parameters
The CNC control system manages various parameters, including the feed rate (how fast the tool moves into the workpiece), spindle speed (rotation speed of the cutting tool), and depth of cut (how much material is removed during each pass). These parameters are critical for achieving the desired machining results.
Coolant and Chip Management
A coolant system is often used to dissipate heat generated during machining and to remove chips and debris. The coolant system helps maintain the tool’s temperature and prevents overheating. It also flushes away chips from the cutting area to avoid interference with the cutting process.
Tool Changes
Some CNC milling machines are equipped with automatic tool changers. When different cutting tools are needed for the machining process, the machine can automatically change the tool as specified in the CNC program.
Quality Control
Quality control measures may be in place, such as probes or sensors to verify part dimensions and alignment during the machining process.
Completion
Once the CNC program is executed, the machining process is complete, and the finished part or component is removed from the machine.
The working principle of a CNC milling machine revolves around the automation of tool movement, precise control of parameters, and the ability to produce parts with high precision and repeatability. CNC milling machines are used in various industries for producing parts with intricate geometries and tight tolerances, making them a fundamental tool in modern manufacturing processes.
Conclusion
In conclusion, a CNC milling machine is a critical tool in modern manufacturing. Its main components, including the machine base, worktable, spindle, cutting tool, control panel, drive motors, tool changer, guideways, and coolant system, each play a specific role in automating the material removal process. The machine’s working principle involves precise control of tool movement based on computer-generated programs, resulting in the creation of complex and precise parts with high efficiency. CNC milling machines are versatile, offering the capability to work with various materials and perform a wide range of machining operations, making them a cornerstone of modern industrial production.