Physical modeling and simulation of high-speed cutting process and cutting parameter optimization on this basis is the most effective way to solve the low efficiency of CNC machine tool machining. Process physical modeling and simulation refers to the cutting process for the physical quantities (such as chip thickness, cutting force, power, torque, cutting temperature, surface morphology, etc.), physical phenomena (such as chatter, tool wear, etc.) and the interrelationship between the cutting parameters to establish a mathematical model and the physical quantities and physical phenomena to predict the process. Optimization of cutting parameters refers to the process of selecting one or more variables as the objective function on the basis of physical modeling and simulation, and taking certain physical quantities in the machining process as constraints to obtain optimized cutting parameters.
Since most of the current research on modeling and simulation of milling process is limited to constant cutting conditions, the cutting that occurs in the actual engineering mostly belongs to the category of Variant Cutting Process or Complex Cutting Condition Cutting. In order to facilitate the modeling and simulation of complex cutting conditions milling process for systematic research, this paper first of all complex cutting conditions cutting the following definition: complex cutting conditions cutting refers to the use of complex structural tools, along the non-linear trajectory or for the complex processing of the object for cutting, cutting conditions in the cutting process with the time constantly changing.
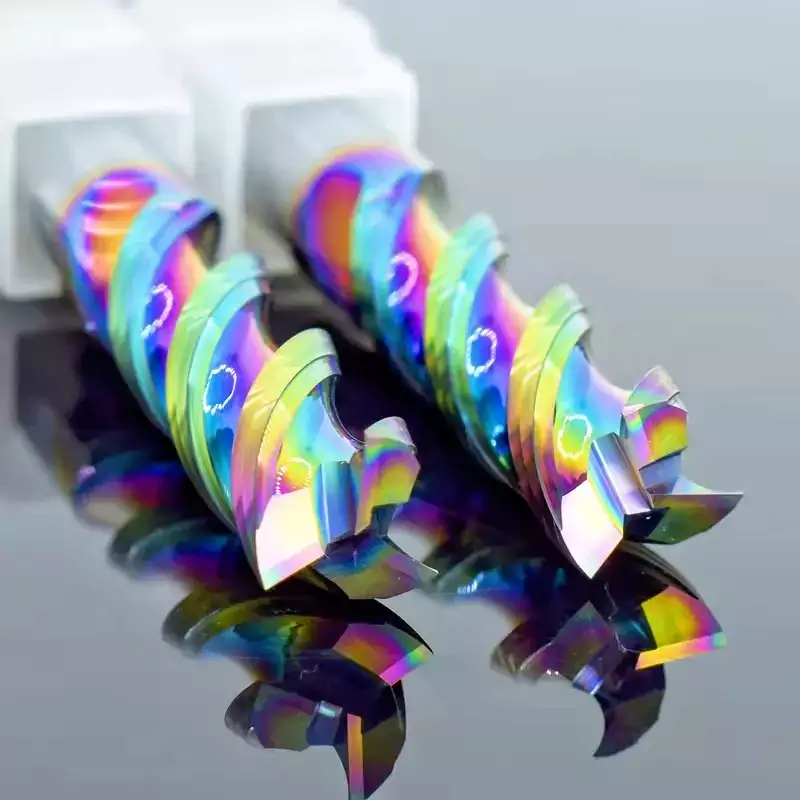
Among all the physical quantities involved in the modeling and simulation of high-speed milling under complex cutting conditions, the modeling and simulation of cutting force is the most critical. Cutting force not only directly affects the service life of tools and machine tools and the machining accuracy of parts, but also is a prerequisite for machining deformation, chatter and surface morphology prediction. Chatter is a strong self-excited vibration that occurs during the cutting process, which originates from the coupling between cutting force and tool-workpiece vibration [1-3].
The occurrence of chatter will seriously limit the efficiency of cutting, reduce the machining accuracy of parts, damage to the tool and machine tool spindle, the study of chatter aims to find out the conditions under which chatter occurs, through the selection of suitable process programs and cutting parameters to avoid chatter in the cutting process. Surface quality directly affects the performance of parts, cutting tool geometry, tool and spindle eccentricity, process system dynamics parameters and cutting parameters and other factors will have an impact on the surface quality of machined parts.
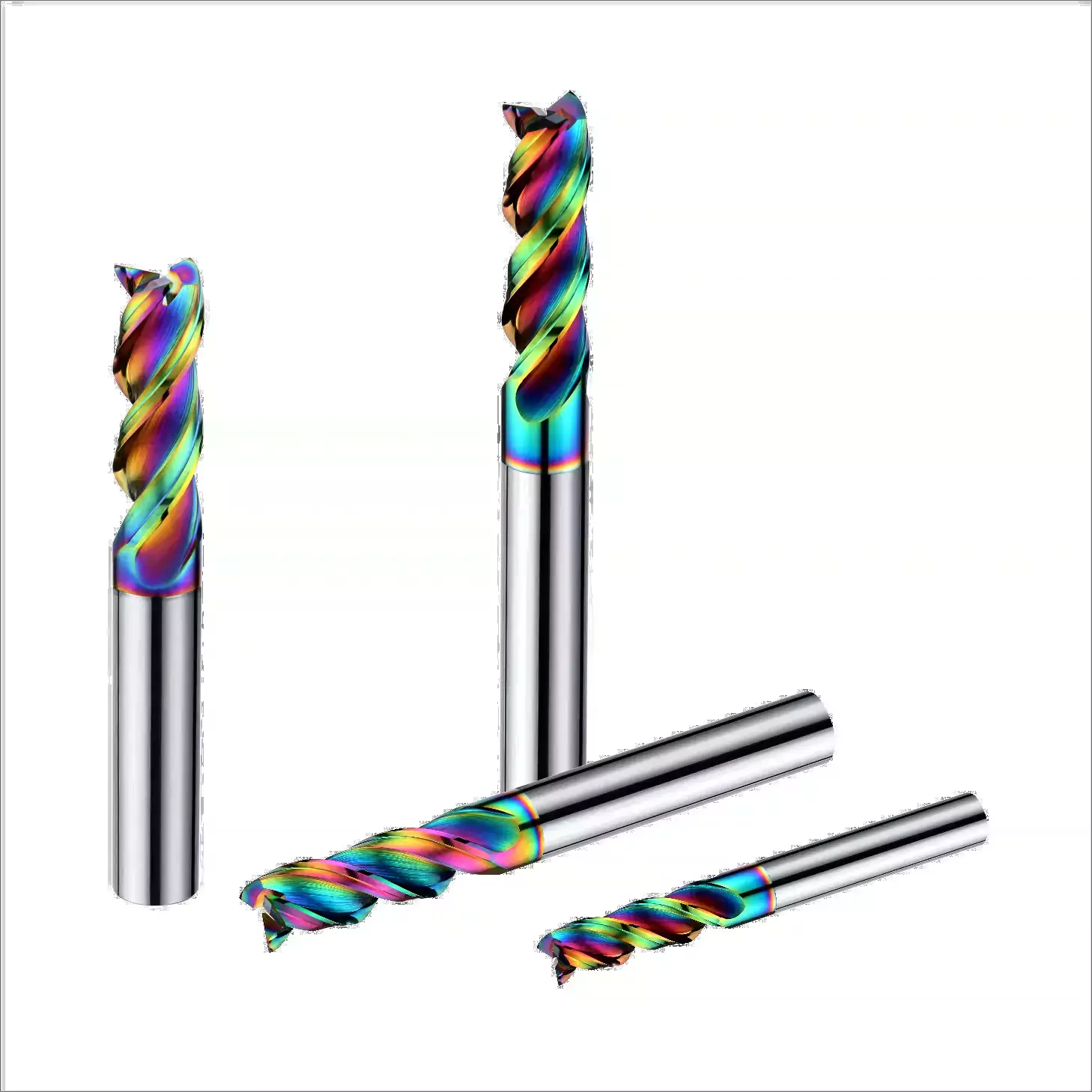
The study of surface quality generation mechanism is aimed at finding out the relationship between surface quality and various influencing factors, through the control of the influencing factors so that the surface quality of machined parts to meet the design requirements. The importance of cutting temperature prediction is that cutting temperature affects tool wear and restricts the efficiency of cutting and machining, and the temperature in the contact zone between the tool and the workpiece plays a decisive role in the wear rate of the tool [4]. When machining advanced materials such as titanium alloys and nickel-based alloys, cutting temperature is the main limiting condition that determines the selection of machining parameters except for chatter [5].
To make accurate predictions of physical quantities and physical phenomena such as cutting forces and chatter, it is crucial to obtain the kinetic characterization parameters (tip point frequency response function) of the process system, especially the machine-tool system. Although the hammering experiment method is very effective, the experiment needs to be repeated once a certain part of the machine-tool system (shank, tool, tool mounting overhang length, etc.) is changed.
To address this situation, a comprehensive experimental modal technology and dynamics theory analysis methods, the construction of the shank (spindle) – milling tool response coupling model, through a small number of experiments with analytical methods to obtain the process system dynamics parameters, you can save a lot of test time, but also a systematic analysis of which variable factors on the process system stiffness and vibration stability domain of the influence of the cutter, easy to achieve cutting parameter optimization.
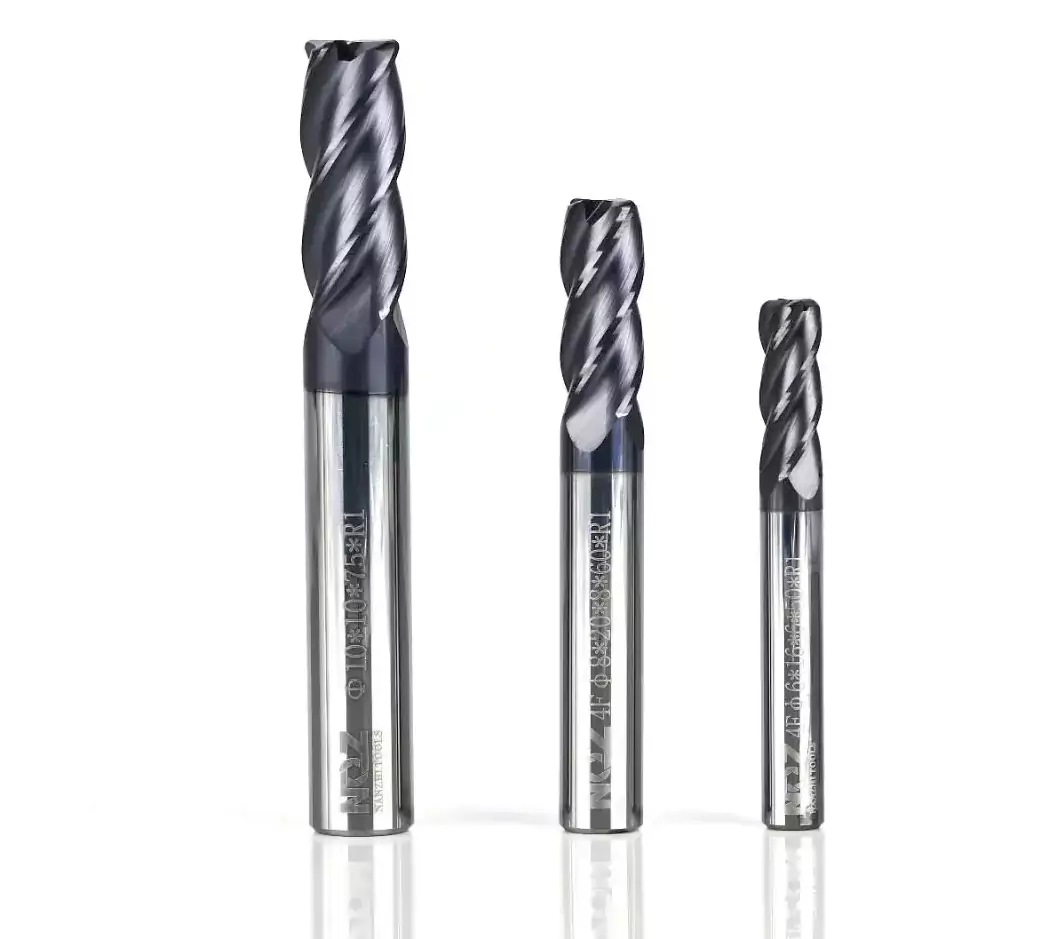
Modeling and simulation of physical quantities in high-speed milling process under complex cutting conditions are aimed at optimizing the processing scheme and cutting parameters. For the high-speed CNC milling of highly rigid structural parts that require large amounts of metal removal, the conventional optimization with the material removal rate as the objective function has a significant effect; for the high-speed CNC milling of weakly rigid parts, the primary task is to ensure that qualified products are processed by means of reducing the machining deformation and avoiding the occurrence of chatter, and machining efficiency has been relegated to the second place.
In the CNC machining of such parts, on the one hand, the parts are thin-walled, weak rigidity, easy to produce machining deformation; on the other hand, some special parts structure leads to the need to use a thin and long cutting tool, in the cutting force is prone to “let the knife” phenomenon. Weak rigidity of the tool and weak rigidity of the joint role of the workpiece, so that the machining process is more prone to vibration. Therefore, it is necessary to systematically analyze the process system (machine tool – workpiece system and machine tool – tool system) dynamics parameters of dynamic deformation, surface morphology and chatter and other factors closely related to the quality of parts machining, as well as machining process parameters on the process system dynamics parameters.
In summary, the kinetic modeling and simulation study of high-speed milling under complex cutting conditions, and the optimization of cutting parameters according to the simulation results are not only theoretically innovative, but also of great practical significance for the improvement of the machining efficiency of CNC machine tools and product quality.
Reference
- [1] Tobias S.A. Machine Tool Vibration Research [J]. International Journal of Machine Tool Design Research, 1961, 1(1): 1- 44
- [2] Tlusty J., Polacek M. The Stability of Machine Tools Against Self Excited Vibrations in Machining [J]. ASME International Research in Production Engineering, 1963, 1(1): 465 – 474
- [3] Merritt H.E. Theory of Self-Excited Machine-Tool Chatter [J]. Journal of Engineering for Industry, 1965, 87(4): 447- 454
- [4] Usui E., Shirakashi T. Kitagawa T. Analytical prediction of three-dimensional cutting process, Part 3: Cutting temperature and crater wear of carbide tool [J]. Transactions of ASME, Journal of Engineering for Industry, 1978, 100(1): 236 – 243
- [5] Klocke F., Konig W. Gerschwiler. Advanced Machining of Titanium and Nickel-Based Alloys [J]. Advanced Manufacturing Systems and Technology, Springer Verlag, New York, USA, 1996